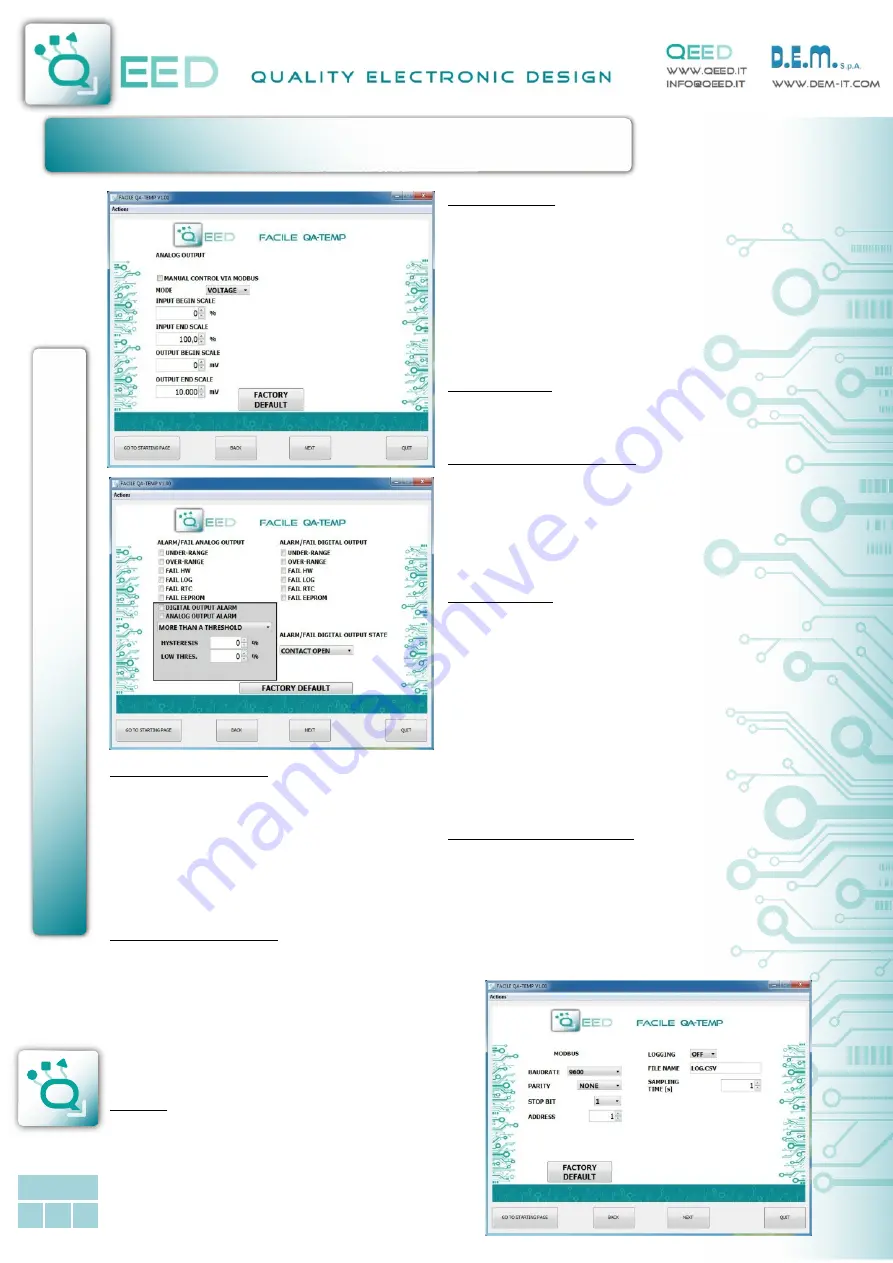
FAIL MESSAGE/ ANOMALY:
FAIL HW:
problems in the measurement chain (electrical
connections,
microprocessor
that
manages
the
measurement, sensor disconnected or faulty).
FAIL LOG:
problem on recording data (without the
availability of stick usb memory stick usb not recognized).
FAIL RTC:
problem on backup battery (dead or defective).
EEPROM FAIL:
problem microprocessor configuration (not
calibrated module, takes no configuration).
MODBUS COMMUNICATION:
This is the last window of the device configuration. The left
column contains the parameters to be set for the
communication speed BAUDRATE (from 1200 to 115200),
the PARITY (None, Odd, Even), the STOP BIT (1 or 2), the
Modbus address to be assigned to the device . You do not
need to configure these parameters for the use of the
module with digital / analog output. It is possible to use the
module with RS485 serial output with Modbus output
analog and digital simultaneously.
LOGGING:
On the right side of the window you can enable the feature
LOG for the acquisition of data on usb pendrive. You can
assign a name to the log file by associating the extension.
Xls,. Xlsx,. Csv,. Txt,. Dat. Logs. The default file is in text
format. The minimum sampling time is 1 second, the
maximum is about 18 hours.
PROGRAMMING THE DEVICE BY SOFTWARE
FACILE QA-TEMP
P
R
O
G
R
AM
M
IN
G
T
H
E
D
E
V
IC
E
B
Y
S
O
F
T
W
AR
E
FA
C
IL
E
Q
A
-T
E
M
P
4
09
2015
ANALOG OUTPUT:
You can associate the analog output to a single INPUT
(you have already performed the selection in the previous screen). The mode
of the analog output could be VOLTAGE or CURRENT. The QA-TEMP has the
ability to scale the inputs and outputs as required, then select the range of
measurement inputs (INPUT BEGIN SCALE and INPUT END SCALE) to assign
to the analog output signal (OUTPUT BEGIN SCALE and OUTPUT END SCALE).
Depending on the choices you make will change the units of the values in
the input and output. If you select MANUAL CONTROL VIA MODBUS, you can
manage the module as an AO (Analog Output) or a DO (Digital Output), thus
freeing the analog output and digital input selected.
The analog output will be handled via RS485 Modbus RTU (see register map).
DIGITAL OUTPUT:
The digital output starting as OPEN CONTACT (that is if
there is an alarm already set or active). If you want to change the initial status
of the digital output select CONTACT CLOSED from the dropdown in the
upper right.
ALARM/ FAIL ANALOG OUTPUT:
It is possible to use the analog output to
control any supervening anomaly Hardware HW FAIL, FAIL RTC Real Time
Clock anomaly that stores the date and time, FAIL EEPROM for the anomaly
on the microprocessor, FAIL LOG if an anomaly occurred during data
acquisition, UNDER RANGE scale of measurement set, OVER RANGE scale of
measurement set. It is possible to select multiple items in the menu. In case
of alarm the analog output will go to 21mA or 10.5 V depending on the
selection made in the previous window.
ALARM WINDOW:
You can activate the ALARM functionality (in the gray
box), on the digital output or on the analog output, or both simultaneously.
In this window you can manage HOW and WHEN activate the alarm by
selecting the options from the dropdown menu : MORE THAN A THRESHOLD,
LESS THAN A THRESHOLD, NOT BETWEEN TWO THRESHOLDS, BETWEEN TWO
THRESHOLDS. We therefore have the possibility to insert the values of
THRESHOLD (Upper and Lower) and the value of HYSTERESIS. In the case
where it is selected the value of a
Higher threshold
when the signal falls
below, the alarm switched off at the threshold value minus the value of
hysteresis. In the event that you have chosen the value of a
Minor threshold
,
when the value exceeds the threshold plus the hysteresis value, the alarm
switch off. In the case where it is selected
between two thresholds
, the
hysteresis is external. In case you have selected
Not included between two
thresholds, the hysteresis
is internal.
ALARM/ FAIL DIGITAL OUTPUT:
It is possible to use the digital output to
control any supervening anomaly Hardware HW FAIL, FAIL RTC Real Time
Clock anomaly that stores the date and time, FAIL EEPROM for the anomaly
on the microprocessor, FAIL LOG if an anomaly occurred during data
acquisition, UNDER RANGE scale of measurement set, OVER RANGE scale of
measurement set. It is possible to select multiple items in the menu. The
alarm can be associated with the state of the digital input (HIGH or LOW) for
up to 15 cycles per minute. STATE DIGITAL ALARM / FAIL allows you to define
the status of contact in case of alarm (CONTACT OPEN or CLOSED).
ENGLISH