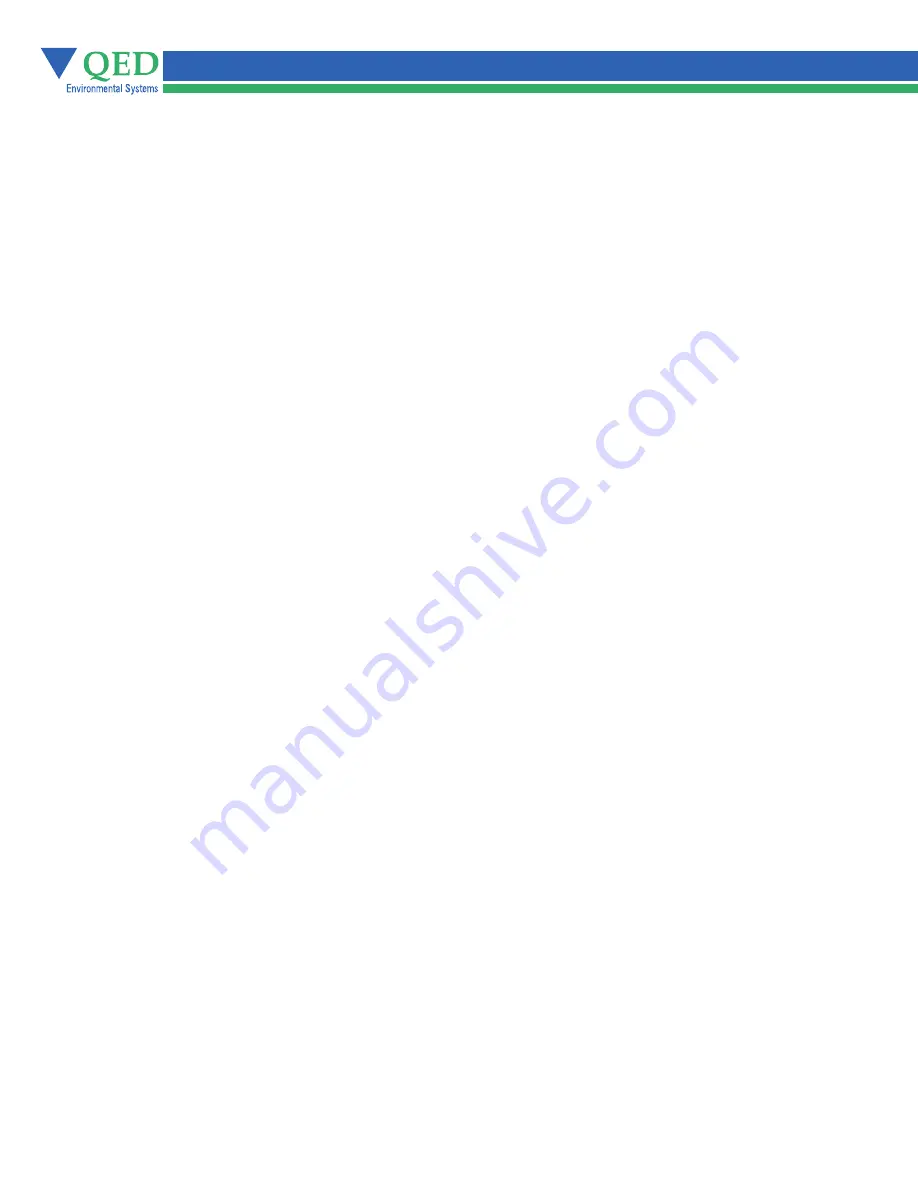
Chapter 3: Overview
The AutoPump is very versatile and available in a wide range of lengths, valve arrangements, and materials of
construction to meet particular site specifications.
Equipment will vary by application and site specifications. (See Chapter 3)
Pump Diameter:
Pressure Range:
High Pressure Option:
Flow Ranges:
3.6 inch (91 mm)
5 - 120 psi (0.4 - 8.5 Kg/cm²)
5 - 200 psi (0.4 - 14.1 Kg/cm²)
0-14 gallons per minute (0-53 liters per minute)
This is How it Works
General Specifications
The AutoPump® fills and empties automatically, and is very easy to install, use, and maintain.
NOTE:
The figures shown here are simplified schematics.
5
Revision 3 - December, 2013
Revision 3 - December, 2013
The AutoPump is a pneumatic fluid extraction pump that pumps in pulses. It handles any liquid which flows freely
for vertical operation in well casings with a 3.75-inch
(9.53cm)
or greater internal diameter. It can pump particles up
to 1/8-inch in diameter.
The AutoPump is a submersible compressed air-driven pump which fills and empties automatically. It also controls
the fluid level in a well automatically. The pump fills (
See Figure
3
) when fluids enter either the top or bottom check
valve. Air in the pump chamber exits through the exhaust valve as the fluid fills the pump. The float inside the pump
is carried upwards by the fluids rising in the casing until it pushes against a stop on the control rod, forcing the valve
mechanism to switch to the discharge mode.
The switching of the valve causes the exhaust valve to close and the air inlet valve to open. This causes the pump
to empty (
see Figure
3
) by allowing compressed air to enter the pump. This pressure on the fluid closes the inlet
check valve and forces the fluids up the discharge line and out of the pump through the outlet check valve. As the
fluid level falls in the pump, the float moves downward until it pushes against the lower stop on the control rod, forcingthe
valve mechanism to switch to the fill mode. The outlet check valve closes and prevents discharged fluids from re-entering
the pump. The filling and discharging of the pump continues automatically.
into the pump and is compatible with the component materials and with the connecting hoses. The AP
Ultra
is intended