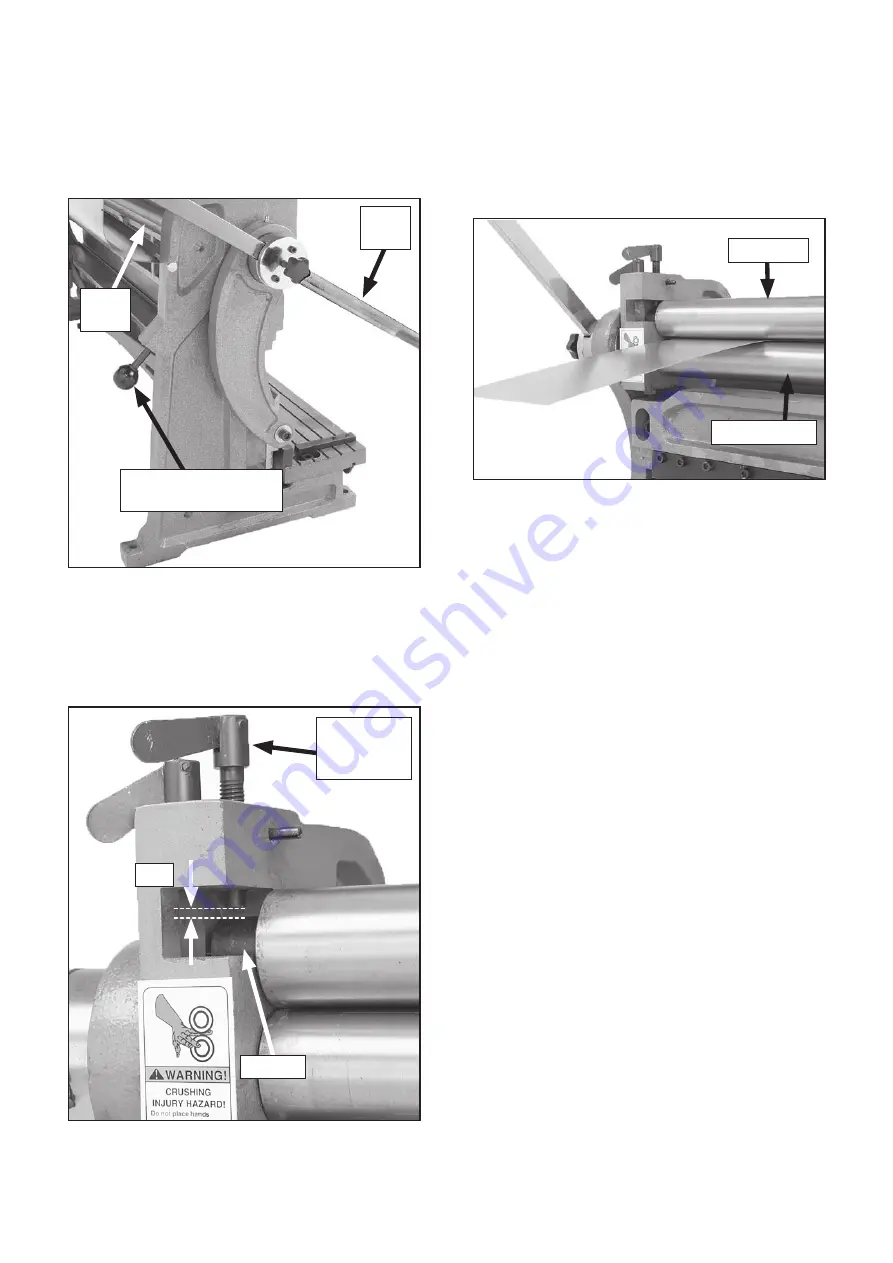
8.
Unscrew the thickness adjustment leaf bolt
until the gap (Figure 7 ) between the leaf
bolt and the bushing is wider than the thick-
ness of the workpiece.
7.
Unscrew the diameter adjustment knobs
until the rear roller is backed-off completely
(Figure 6 ).
Figure 6
Diameter Adjustment
Knob
Work
Lever
Rear
Roller
Gap
Figure 7
Thickness
Adjustment
Leaf Bolt
9. While rotating the work lever, feed the sheet
metal between the top and bottom rollers
(Figure 8 ) until approximately 1-inch pro-
trudes through the other side.
10.
With the metal positioned between the top
and bottom rollers, tighten the thickness
adjustment leaf bolts until they are snug.
11.
Tighten the diameter adjustment knobs to
raise the rear roller a few millimeters to get
your initial bend setting.
Note: The heavier the gauge of metal, the
less aggressively you can adjust the rear
roller. With rigid metals such as aluminium,
you may have to leave the rear roller at the
lowest position and make more rolling repeti-
tions to achieve the needed bend radius.
Tip: To ease feeding the workpiece past the
third roller on the first rolling operation, use
the brake first to make a slight initial bend
in the workpiece, so the workpiece does not
butt up against the rear roller, but rather rides
up and over the roller.
Figure 8
Top Roller
Bottom Roller
Bushing
Summary of Contents for Bernardo 1320 S
Page 10: ...Parts Drawing for 3 in 1 1320mm ...
Page 12: ...Maschinen Austria ...