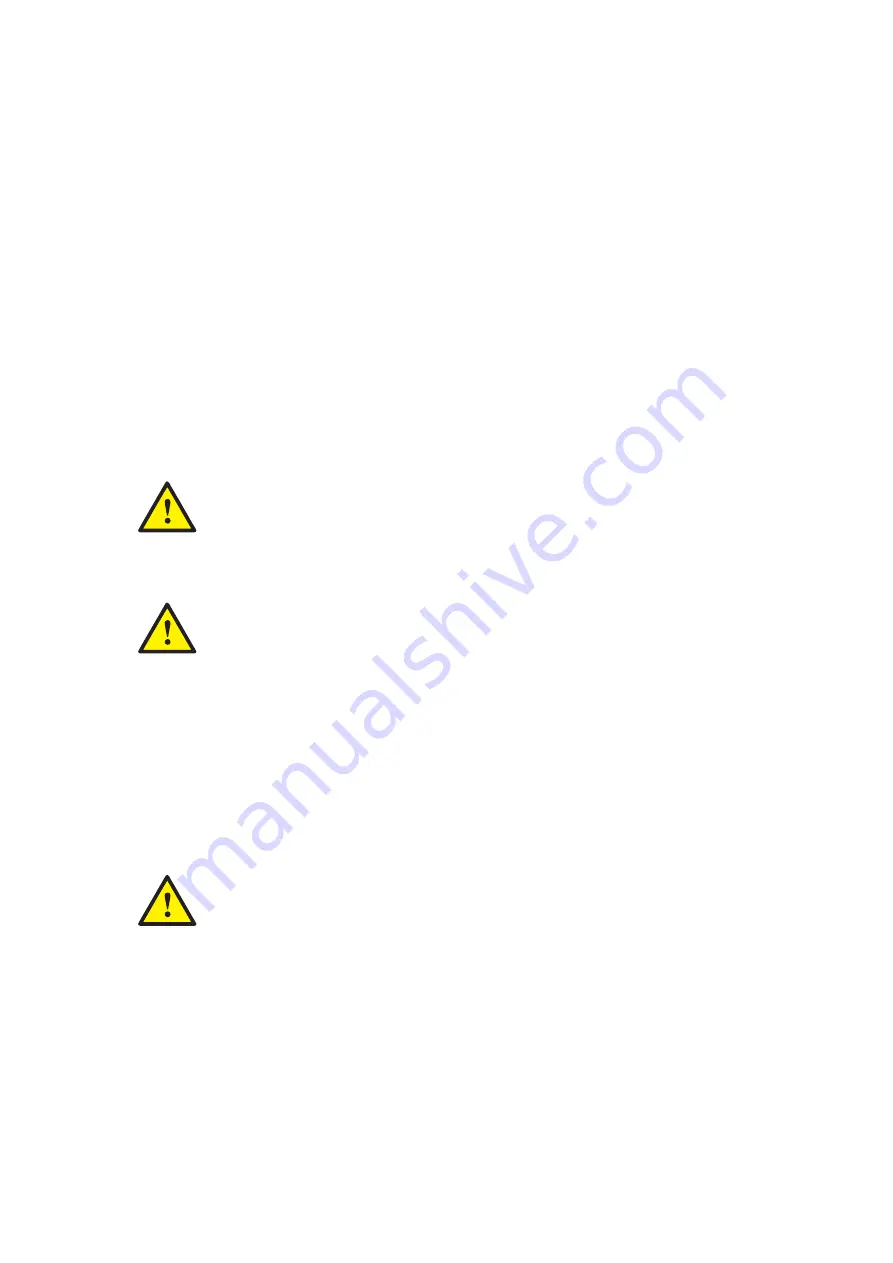
Operating and maintenance instructions
EN
5
LI 3019.03
2.2 Expected use
These vacuum pumps have been designed to handle air and small quantity of water
vapour only. They are suitable to evacuate closed systems or to operate at a constant
vacuum within the following vacuum range:
PVL 401 - PVL 541 from 0.5 to 400 mbar (absolute)
PVL 401/B - PVL 541/B from 10 to 850 mbar (absolute)
The ambient temperature and the inlet temperatures must be included between 5° and
40°C.
In case you get temperatures outside this range, please get in touch with us.
Handling of other types of gas or vapours must be declared in advance to P.V.R. that will
give the conformity to the specific use.
2.3 Forbidden use
ATTENTION:
The pump MUST NOT handle:
- liquids or solid substances;
- dangerous, explosive or aggressive gases and vapours;
- pure oxygen or air mixtures enriched with oxygen;
It is forbidden to use the discharge of the pump to create even limited pressures.
ATTENTION:
It is forbidden to install the pump in a potentially explosive environment.
2.4 Protections
The pump must be protected against suction of dust, solids or liquids.
For those applications where such a protection is not ensured, a vacuum gauge must be
installed on the oil tank for a visual check of the exhaust filter clogging.
In order to get an automatic pump stop, a pressure switch set at 0.7 bar can be installed.
The pump is supplied without electric control panel. The electric motor must be protected
according to the regulations in force.
ATTENTION:
In case of applications where the pump stop or failure can cause damages to people
or things, safety measures for the system must be adopted.
2.5 Accessories
The following accessories useful for the installation and for the control of the operation
parameters of the pump are available:
- external inlet filter
- connection fittings
- vacuum meters/ vacuum switches
- pressure meters/ pressure switches
- temperature switch
- low oil level switch