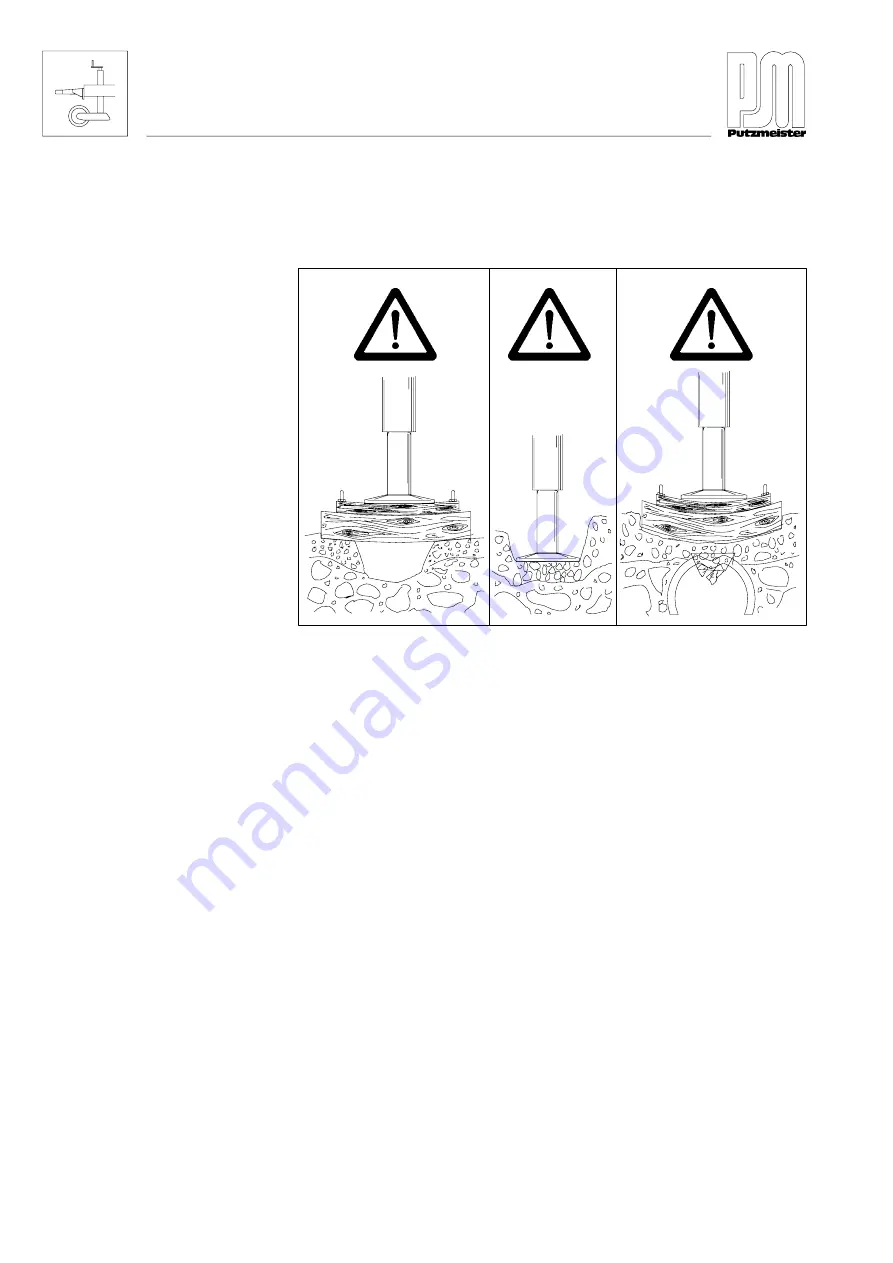
Transport,settingupandconnection
512
AP06_005_1508EN
The supporting ground must be firm enough to absorb the forces
conducted by the support feet into the ground. There must not be
any voids or ground unevenness under the support feet.
22102802
No voids or ground unevenness under the support feet
"
Always rest the support feet on support plates, timber blocks
or other suitable construction timber.
It is recommended that you select a set
−
up site which has been con
creted if the concrete pump is to remain on the same set
−
up site for
a prolonged period.
It is recommend that concrete pumps working at high
−
pressure and
high delivery rate are securely anchored.
Supporting ground
Summary of Contents for 210109379
Page 4: ......
Page 16: ......
Page 18: ......
Page 24: ......
Page 26: ......
Page 88: ......
Page 170: ......
Page 192: ......
Page 220: ......
Page 222: ......
Page 268: ......
Page 270: ......
Page 290: ......
Page 292: ...7 22...
Page 296: ...Maintenance card 03 002 Page 2 of 2 7 26 WK03_002_1109EN...
Page 312: ...Maintenance card 04 013 Seite 6 von 6 7 42 WK04_013_1109EN...
Page 324: ...Maintenance card 07 069 Page 6 of 6 7 54 WK07_069_1109EN...
Page 340: ...Maintenance card 07 070 Page 16 of 16 7 70 WK07_070_1109EN...
Page 354: ...Maintenance card 07 071 Page 14 of 14 7 84 WK07_071_1109EN...
Page 362: ...Maintenance card 07 072 Page 8 of 8 7 92 WK07_072_1109EN...
Page 376: ...Maintenance card 07 074 Page 6 of 6 7 106 WK07_074_1109EN...
Page 390: ...Maintenance card 07 075 Page 14 of 14 7 120 WK07_075_1109EN...
Page 404: ......
Page 410: ......
Page 412: ......
Page 434: ...Glossary G 22 BP14_002_0501EN...