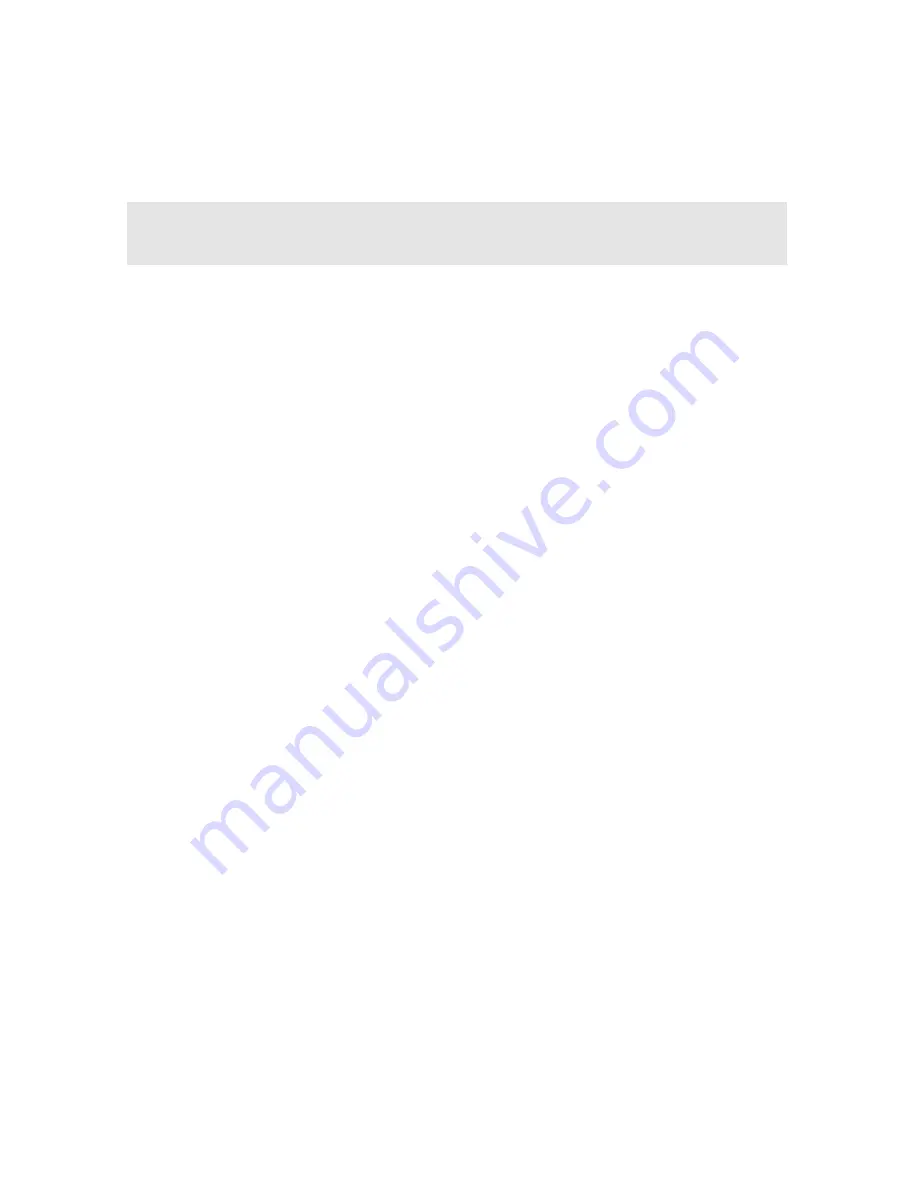
P
U
R
O
F
L
U
X
C
O
R
P
O
R
A
T
I
O
N
PAGE # 16
PF-50 Series Filter (ver. 4/5/05)
START-UP PROCEDURE
Before initial start-up or after a long shutdown period, the filter unit should be thoroughly inspected.
1. Close all isolation valves in interconnecting piping and relieve all pressure from the filter system by
opening the manual air relief valve.
2. If supplied, loosen the four hex bolts around the pump pre-strainer lid. Remove the lid, inspect gasket
and lubricate if necessary. Clean debris from the pump pre-strainer basket. Prime the pump and associated
piping by filling the pre-strainer housing. Replace the basket, lid and tighten bolts.
3. Turn the pump and motor shaft by hand to ensure free rotation.
4. Remove the top handhole/manhole cover by removing the hex nut on the crab clamp by pushing the
handhole/manhole into the vessel (do not drop handhole/manhole). Remove and inspect the gasket.
(replace if necessary)
5. Inspect the internal assembly for any damage. Install media as described in loading media (page 7).
6. Inspect the handhole/manhole, gasket, ring, and cover for foreign matter, and clean all surfaces. Place
the handhole/manhole cover into the vessel. Slip the gasket over the handhole/manhole and reinstall the
crab clamp and hex nut. Align the gasket and crab clamp properly with the handhole/manhole and ring,
before tighten the hex nut. Do not overtightening the hex nut. Overtightening hex nut can damage gasket.
7. Prime pump by filling the pre-strainer and associated piping with water. Refer to pump pre-strainer (page 12).
Check pump rotation by bumping the motor. Verify rotation with the arrow on the pump volute. DO NOT
run the pump for an extended period of time in reverse direction or dry. Have a qualified electrician change
leads to correct rotation.
8. Open the service valves in the filter inlet, outlet, and backwash lines. Before starting the pump verify all
valves are open. Open the manual air relief valve on top of the filter vessel. Start the pump and fill filter vessel.
Once a steady stream of water is coming out the manual air relief valve, and all air has been evacuated,
the manual air relief valve can be closed. Verify the auto air vent is open by turning the knob located on
the top of the unit one half turn
9. Check the voltage and current of all leads on the pump motor. The correct amperage draw can be found
on the motor nameplate. (Refer to table 5, page 9)
10. Check the filter unit for any unusual noise or vibration. Shut filter unit off and contact your local PUROFLUX
representative or the factory direct if there are any questions about the performance of the filter unit.
11. Check the filter unit and all integral piping to the unit for any air or fluid leaks. All air leaks must be found
and repaired. Failure to do so could result in poor performance and/or personal injury.
12. Backwash the filter. See Backwash Cycle (page 13) and Table III (page 7). After backwashing the
filter, check the pressure gauge on top of the filter vessel and record the clean start up pressure. Use the
starting pressure as a bench mark whenever routine maintenance is preformed.
13. After several hours of run time from start up, perform steps 8 through 12 again.
NOTE:
Perform the first five recommendations with the electrical power off and locked out. Refer to
the section under "Safety" regarding the safeguarding of maintenance personnel from biological
contaminants prior to start-up.