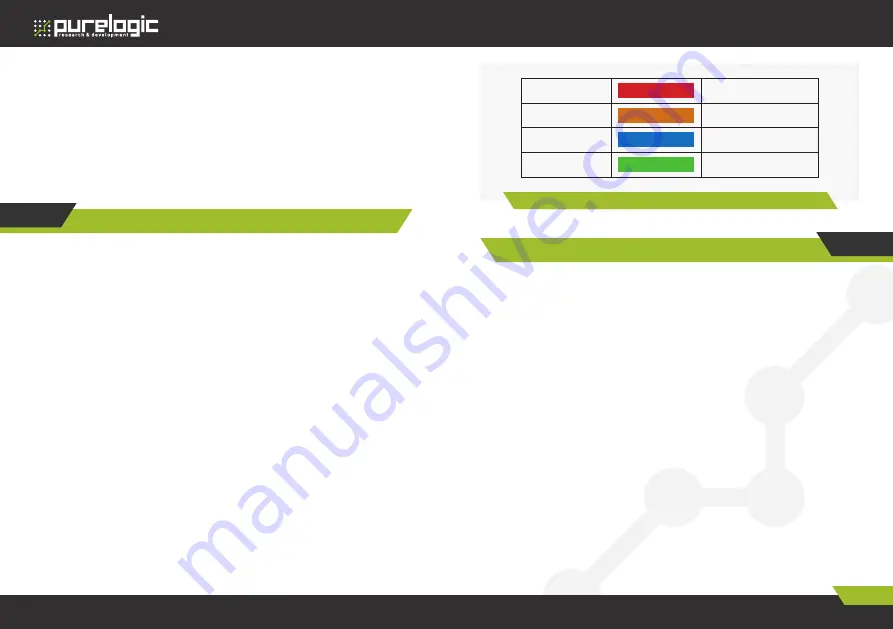
Edition from 23.11.2017
7
PLD442.
Microstepping stepper motor driver
www.purelogic.ru
8 (800) 555 63 74
06. Controlling signals connection to stepper motor driver
Fig. 3.
Purelogic R&D stepper motor connection to the driver
07
Stepper motor connection
PLD442 driver is optimal for bipolar and unipolar stepper motors
Purelogic R&D series PL42/PL57. Stepper motor connection to the
driver is performed to XP6 and XP7 connectors as it is shown in fig.5
(clips PH1.1[+A], PH1.2[-A] и PH2.1[+B], PH2.2[-B]).
The driver has protection against coils linked together.
Purelogic R&D stepper motor connection to the driver is performed
according to fig. 3.
Please note in case of changing phases PH1.x<>PH2.x , the motor
will start rotating in the opposite direction ( inversion analogue of DIR
signal).
The length of wires leading to the stepper motor from the driver
must not exceed 10 meters. Longer wires can lead to driver’s work
failures.
It is strongly recommended to interlace the stepper motor wires per
phase, then put this braid to the screened metal sheath. Sheathes and
stepper motor frame must be grounded.
ENABLE signal’s characteristics – working voltage 3 ... 5V, current
consumption is 20mА, action time is 100 ms.
When logic «1», module is switched on, «0», module is switched off.
STEP/DIR/ENABLE are signaled by: STEP – LED4; DIR – LED5;
ENABLE – LED3.
Power source connection
Power source connection is performed according to fig.5.
Voltage supply is indicated by POWER (LED1).
PH1.1 [+А]
Red (RED)
PH1.2 [-А]
Orange (ORG)
PH2.1 [+B]
Blue (BLU)
PH2.2 [-B]
Green (GRN)
Current and supply option
Max supply voltage driver option depends on the applied stepper
motor and desired max rotation speed. Optimal supply voltage
calculation for the stepper motor is carried out according to the
formula U=32*v (stepper motor phase inductance mH), but not more
than 38V.
Supply current must be chosen 50...70% from the claimed stepper
motor coil current.
Working current setting is carried out with trimming resistor R1 (fig.
5).
When there is no STEP signal more than 1 sec, the driver goes to
Sleep mode.
Power off device before making any connections.
08