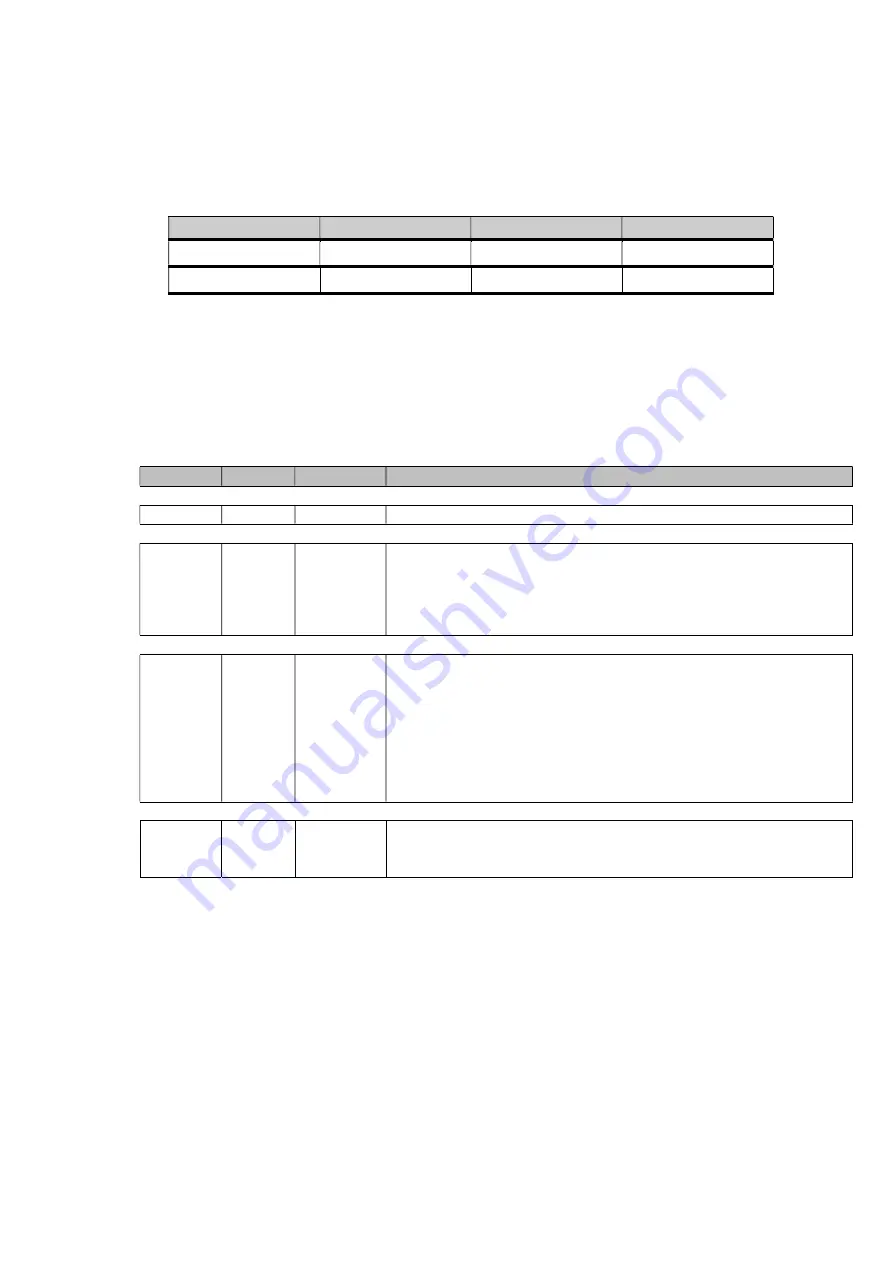
8.3 KOPkit numbers by model:
Pump Model
Wetted Material
Connection Type
KOPkit number
DM7
Polypropylene
NPT / ISO / FLG
KD7P
DM7
316
NPT
KD7A
NOTES:
(1) DM1 through 6 models are covered in a separate publication
(2) Polypropylene KOPkits are identical as only balls and insert o-rings are supplied
9. Model Number Identification
Position Sample Specifies Options
1 – 4
DM
Size/Flow
DM
GLM
5
Y
Motor
Frame and
Size
3
3PH 220/380V (and 460V) MOTOR IEC Frame, TEFC
[50/60 Hz]
Y
NO MOTOR - IEC frame (IEC71 for DMC1-6, IEC90 standard
for DM7)
6
P
Wetted
Materials
A
316L SS Liquid End - PTFE Diaphragm and PTFE O-rings –
316SS Ball Valves
F
PVDF/Viton - PVDF Liquid End - PTFE Diaphragm and Viton®
O-rings - Ceramic Ball Valves
P
PP/Viton - PP Liquid End - PTFE Diaphragm and Viton®
O-rings - Ceramic Ball Valves
7
P
Connection
P
1.5” FNPT with 1.5” ANSI/DIN flange ring as standard
25
Summary of Contents for PULSA GLM7
Page 23: ...22 Figure 14 Check valves metal construction...
Page 30: ...29 12 Dimensional Draw ings...
Page 31: ...30...
Page 32: ...31 13 Parts Diagrams and Parts Lists...
Page 35: ...34...