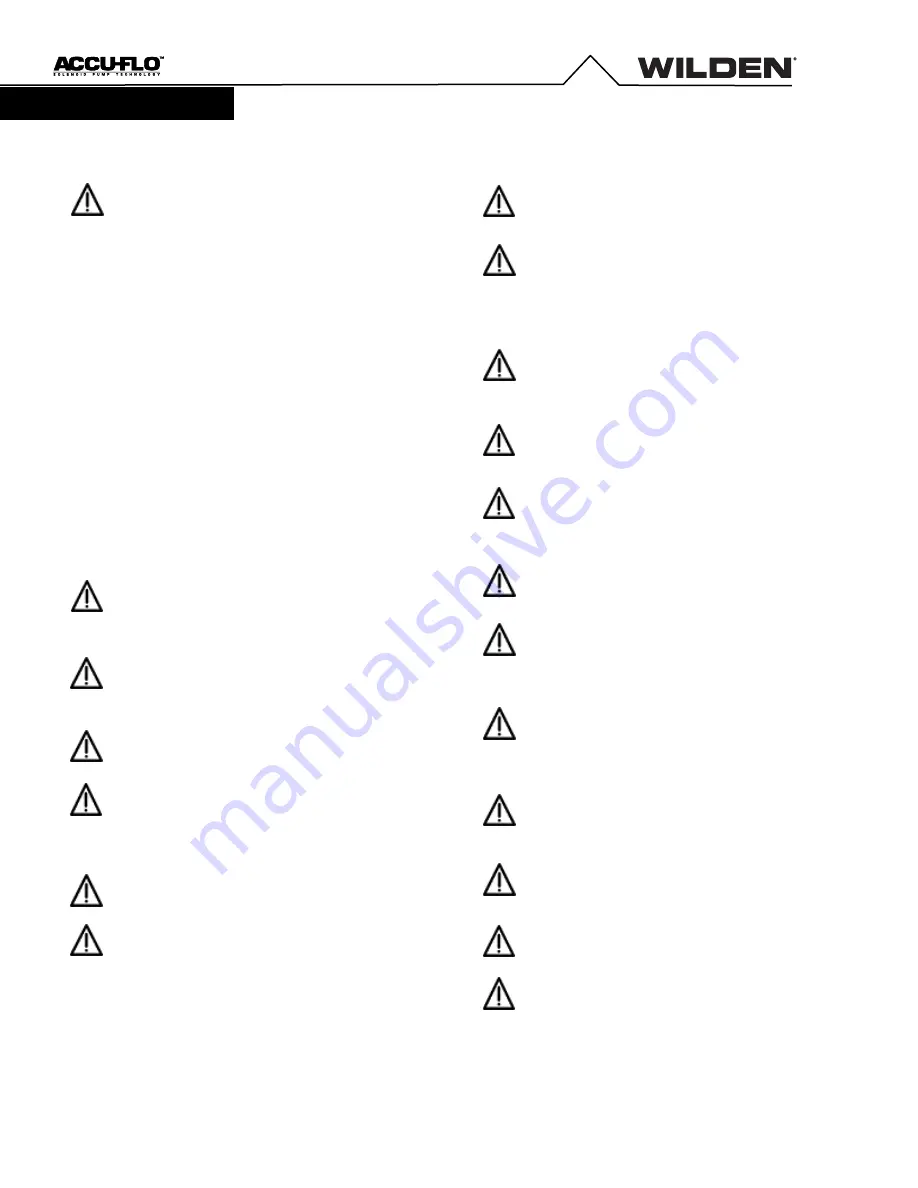
WIL-11060-E-03
Wilden
®
4
Precautions - Read First!
TEMPERATURE LIMITS:
Wetted Path
Polypropylene (PP)
0°C to 79.4°C
32°F to 175°F
Polyvinylidene fluoride
(PVDF)
-12.2°C to 107.2°C
10°F to 225°F
PTFE PFA
-28.9°C to 87.8°C
-20°F to 190°F
Elastomers
Neoprene
-17.8°C to 93.3°C
0°F to 200°F
Buna-N
-12.2°C to 82.2°C
10°F to 180°F
EPDM
-51.1°C to 137.8°C
-60°F to 280°F
FKM
®
-40°C to 176.7°C
-40°F to 350°F
Wil-Flex™
-40°C to 107.2°C
-40°F to 225°F
Polyurethane
12.2°C to 65.6°C
10°F to 150°F
Tetra-Flex™ PTFE
w/Neoprene
4.4°C to 107.2°C
40°F to 225°F
Tetra-Flex™ PTFE
w/EPDM
-10°C to 137°C
14°F to 280°F
Polytetrafluoroethylene
(PTFE)
4.4°C to 104.4°C
40°F to 220°F
*Elastomer choice may change temperature limits.
NOTE: Not all materials are available for all models. See "Wilden Pump Designation
System on page 5 for material options for your pump.
CAUTION: When choosing pump materials, be sure to check
the temperature limits for all wetted components. Example:
FKM
®
has a maximum limit of 176.7°C (350°F) but
polypropylene has a maximum limit of only 79.4°C (175°F).
CAUTION: Maximum temperature limits are based upon
mechanical stress only. Certain chemicals will significantly reduce
maximum safe operating temperatures. Consult engineering
guide for chemical compatibility and temperature limits.
CAUTION: Always wear safety glasses when operating pump.
If diaphragm rupture occurs, material being pumped may be
forced out air exhaust.
WARNING: Prevention of static sparking — If static sparking
occurs, fire or explosion could result. Proper grounding of
pump, valves, and containers is critical when handling
flammable fluids or whenever discharge of static electricity
is a hazard.
NOTE: Do not exceed 5.2 bar (75 psig) air supply for
PFA pumps.
CAUTION: Do not exceed 8.6 bar (125 psig) air supply on
polypropylene and PVDF pumps.
CAUTION: Advanced™ series plastic pumps are made with
plastic that is not UV stabilized. Direct sunlight for prolonged
periods can cause deterioration of plastics.
CAUTION: Before any maintenance or repair is attempted,
the compressed air line to the pump should be disconnected
and all air pressure allowed to bleed from pump. Disconnect
all intake, discharge and air lines. Drain the pump by turning
it upside down and allowing any fluid to flow into a suitable
container.
CAUTION: Blow out air line for 10 to 20 seconds before
attaching to pump to make sure all pipe line debris is clear.
Use an in-line air filter. A 5µ (micron) air filter is
recommended.
NOTE: Tighten all bolts prior to installation. Fittings may
loosen during transportation.
NOTE: When installing polytetrafluoroethylene (PTFE)
diaphragms, it is important to tighten outer pistons
simultaneously (turning in opposite directions) to ensure
tight fit.
CAUTION: Verify the chemical compatibility of the process
and cleaning fluid to the pump’s component materials in
the Chemical Resistance Guide (see E4).
CAUTION: When removing the end cap using compressed
air, the air valve end cap may come out with considerable
force. Hand protection such as a padded glove or rag should
be used to capture the end cap.
CAUTION: Do not over-tighten the air inlet reducer
bushing. Additionally, too much torque on the muffler
may damage the air valve muffler plate. Do not exceed
0.9 N·m (8 in-lbs).
CAUTION: Only explosion proof (NEMA 7) solenoid valves
should be used in areas where explosion proof equipment
is required.
CAUTION: Do not lubricate lube-free pumps.
CAUTION: The A200P pump is not submersible.
NOTE: When reinstalling the outer pistons, apply two (2)
drops of Loctite
®
246 to the shaft internal threads before
the diaphragm assembly
Section 1
Summary of Contents for WILDEN A200B Advanced Plastic
Page 19: ...WIL 11060 E 03 Wilden Notes...