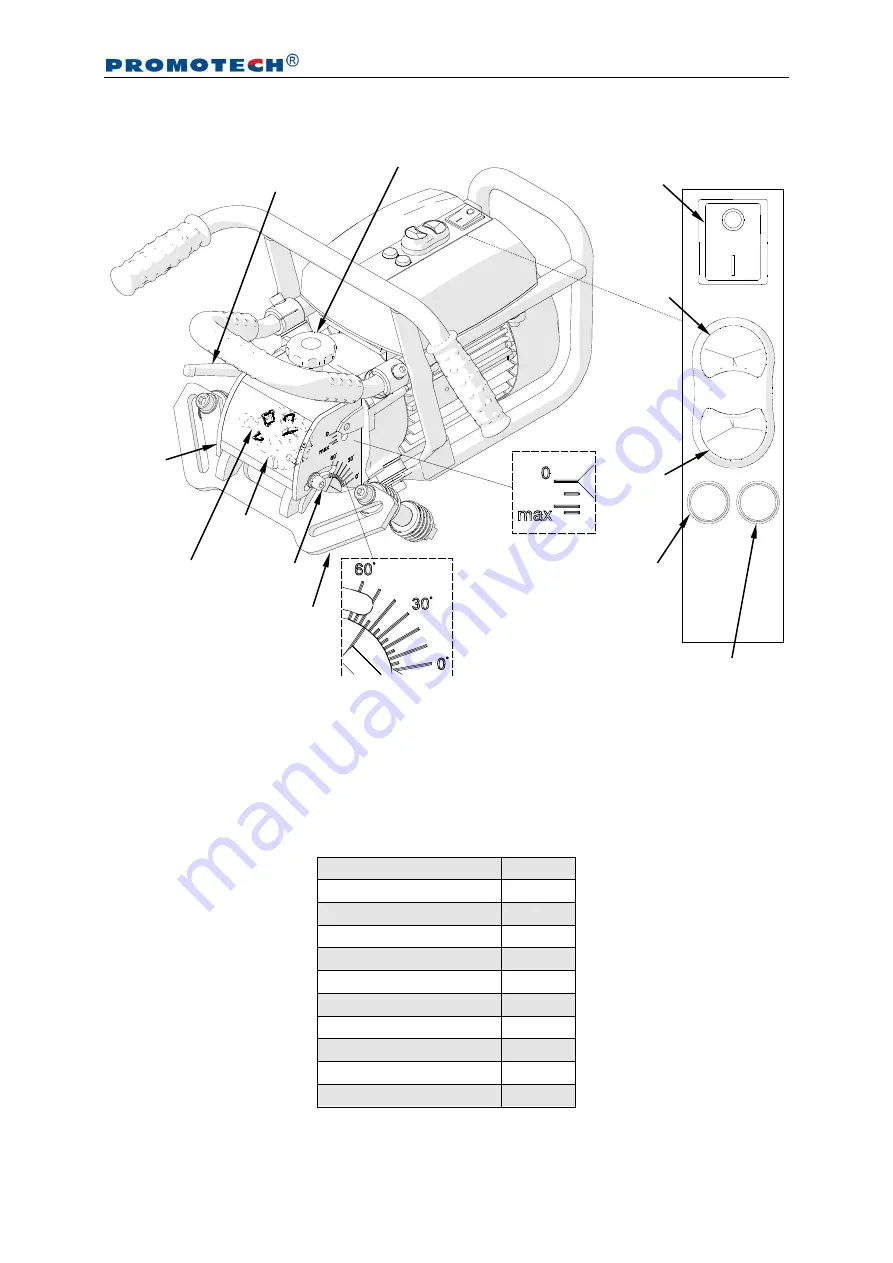
BM-21S
This document is protected by copyrights.
Copying, using, or distributing without permission of PROMOTECH is prohibited.
5
1.3. Design
Fig. 2.
View of the machine and the control panel
1.4. Equipment included
The
BM-21S
is
supplied
in
a
metal
box
with
complete
standard
equipment.
The
included
equipment consists of:
Bevelling machine
1 unit
Cutting insert
10 units
Metal box
1 unit
8 mm hex wrench
1 unit
6 mm hex wrench
1 unit
4 mm hex wrench
1 unit
12 mm flat wrench
1 unit
T15P torx screwdriver
1 unit
Oil for stainless steel
1 unit
Grease for screws
1 unit
Operator’s Manual
1 unit
Depth knob
Bevel width scale
Bevel angle scale
Screws locking the bevel angle
Depth lock lever
Power switch
START
STOP
Operating
mode
lamp
Overload lamp
Guide set
Milling
head
Milling
head
cover