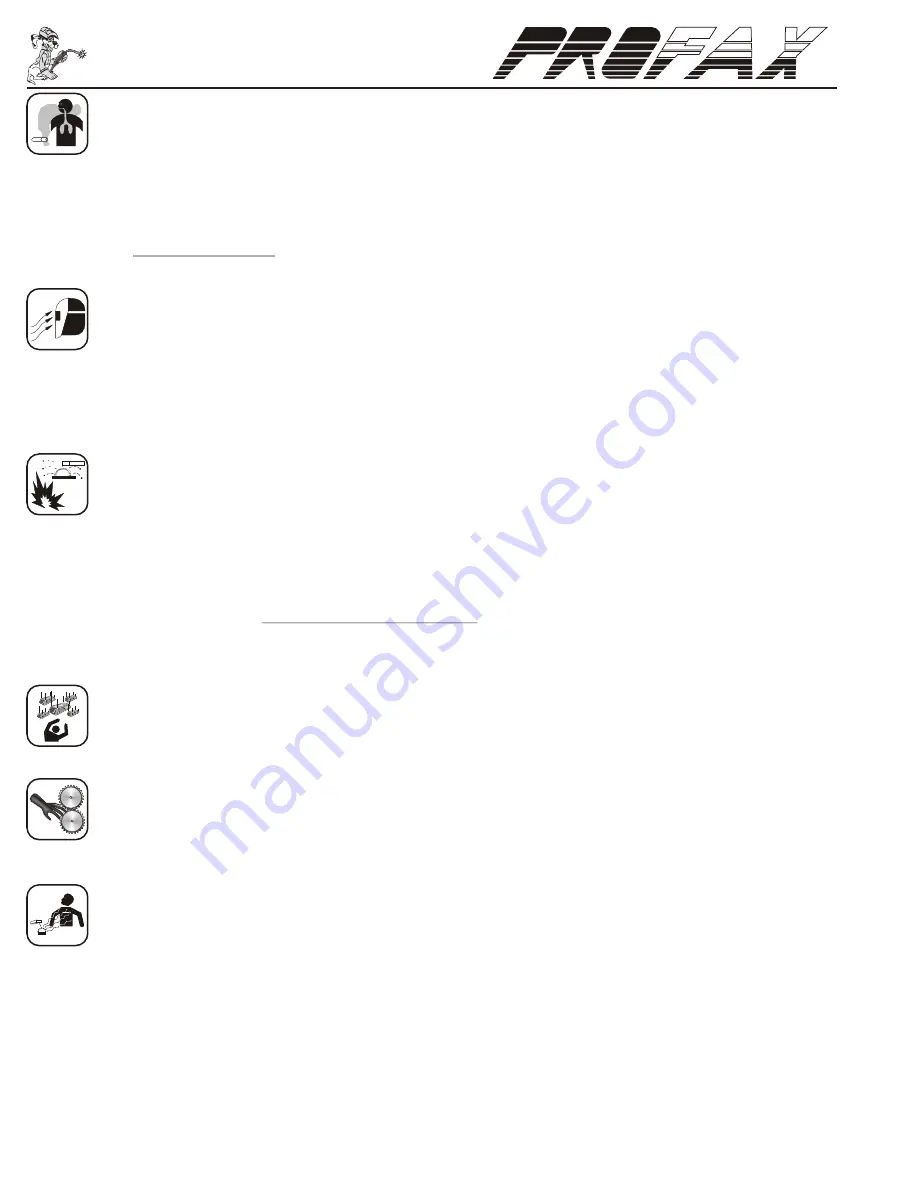
®
®
®
Safety
®
3
2
Safety
SMOKE, FUMES, AND GASES CAN BE DANGEROUS TO YOUR HEALTH
Keep smoke, fumes, and gases from your breathing zone and the general area. Smoke, fumes, and gases from the welding or cutting process are of
various types and strengths, depending on the kind of base metal being welded on. To ensure your safety, do not breathe these fumes or gases.
Ventilation must be adequate to remove smoke, fumes, and gases during the welding procedure to protect operators and others in the immediate area.
Do not weld in locations where chlorinated hydrocarbon vapors are coming from degreasing, cleaning, or spraying operations. Vapors of chlorinated solvents can form
the toxic gas “phosgene” when exposed to ultraviolet radiation from an electric arc. All solvents, degreasers, and potential sources of these vapors must be removed
from the welding area. Shielding gases used for arc welding can displace air and cause injury or death. Fumes produced by welding or cutting, especially in confined
areas, can cause discomfort and physical harm if inhaled over an extended period of time.
Always provide adequate ventilation in the welding and cutting area to insure breathing air is safe. Use air-supplied respirators if ventilation is not adequate to remove
all fumes and gases.
Never Ventilate with Oxygen
, because oxygen supports and vigorously accelerates fire.
REFERENCES: See Safety and Operating References A,B,C,H, and I.
ARC RAYS, MOLTEN MATERIAL, AND SPARKS CAN CAUSE EYE AND SKIN INJURY
Always wear approved eye, ear, and body protection. Remove any and all combustible material from the work area. Never attempt to weld or cut
without a proper head shield, and lens, that conforms to federal guidelines. A number 12 to 14 shade filter lens provides the best protection from arc
radiation. A cover plate protects your eyes from sparks. Protect other nearby personnel from arc rays and sparks. Use approved shielding curtains and
appropriate goggles. Warn them not to watch the arc or expose themselves to arc rays, sparks, or molten material.
Always wear protective clothing and gloves which will not allow skin to become exposed to arc rays, heat, or molten material. Wear ear plugs to protect ears from
sparks. Flammable hair preparations should not be used when welding or cutting. If possible, welding should be done in a booth that has been painted with an
ultraviolet absorbing material such as zinc oxide and a low reflective finish such as lamp black, or shall be enclosed by similarly painted and noncombustible screens.
REFERENCES: See Safety and Operating References A,B,H, and I.
WELDING SPARKS CAN CAUSE FIRES AND EXPLOSIONS
Remove any and all combustible materials from the work area. If this is not possible, cover them to prevent the welding sparks from starting a fire.
Fires & explosions are caused by any combustibles reached by the arc, flame, flying sparks, hot slag, or heated materials. Do not wear any gloves or
clothing that has oil or a fuel type material on it. Always have a properly working and OSHA approved Fire Extinguisher near and be sure everyone has
proper training in its use.
Do not weld, heat, or cut drums or containers that have held combustibles. All hollow spaces, cavities, and containers should be vented prior to cutting, welding, or
heating for they may explode. Make sure proper steps have been taken to insure that venting procedures will not form flammable or toxic vapors from substances
inside containers. Purging with inert gas is recommended. Use only iner t gases or inert gas mixes as required by the process.
Special precautions should be used to prevent hazardous situations when using compressed gas. Use of combustible compressed gases can cause
explosions resulting in personal injury or death.
Never Use Oxygen for Cleaning or Purging.
Arcing against any compressed gas cylinder can cause cylinder damage
or explosion. Read and follow the instructions on compressed gas cylinders, Associated Equipment, and CEA Publication P-1, “Precautions for safe handling of
compressed gases in Cylinders” available from the Compressed Gas Association, 1235 Jefferson Davis Hwy, Arlington, Va. 22202.
REFERENCES: See Safety and Operating References A,D,E,F,G, and H.
FALLING EQUIPMENT
Lift only the unit to be moved without any running gear, accessories or gas cylinders that may be attached to it. Use equipment of a proper size to lift
and move the unit. Falling equipment can cause personal injury and equipment damage.
MOVING PARTS MAY CAUSE INJURY
Have only qualified people remove guards or covers for performing maintenance and troubleshooting. Moving par ts such as cooling fans can maim
fingers or hands and catch loose clothing. Keep tools, hands, hair and clothing away from moving parts. Be sure to reinstall all panels and guards before
operating equipment.
"EMF" ELECTRO MAGNETIC FIELDS
The study of the biological effects of low frequency electric and magnetic fields does not yet let us interpret the results in a single coherent context.
However, there now seems to be an extremely large amount of scientific analysis based on experimentation, at the cellular level and from studies on
animals and humans, that clearly show low frequency magnetic fields interacting with and producing changes in biological systems. Current scientific
understanding of the evidence does not allow definite conclusions concerning advise on avoiding risks. Therefore, the current procedures recommended for
*pacemaker users are also recommended for all humans and other biological systems. To reduce the effects of low frequency electric and magnetic fields, use the
following recommendations:
1. Welding cables should be kept close together by twisting or taping together.
2. Draping or coiling welding cables around the body should be avoided.
3. Welding cables should be kept away from the operator to one side.
4. Work clamp should be connected as close as possible to the area being welded.
5. Operator should not be between the work clamp and the location of the weld being made.
6. Welding power source and cables should be kept as far away as practically possible.
*
Note
: Pacemaker Wearers - Consult your doctor for complete information.
REFERENCES: See Safety and Operating Reference J.
CYLINDERS
Shielding gas cylinders are under high pressure and if damaged can explode. Protect from welding and electrical arcs, excessive heat and mechanical
shocks. Secure cylinders in an upright position by changing to a cylinder rack or stationary support. Use only the cor rect shielding gas for the process.
Never use unmarked cylinders or rely on color markings to denote contents. Keep cylinder caps securely on cylinders unless in use. Turn face away
when opening a cylinder valve. Open cylinder valves slowly then backseat or fully open valve to prevent valve body leaks. Use regulators and hose of a sufficient type
for the compressed gas used. Never connect a regulator to a cylinder with a gas it is not compatible with. Do not transfill cylinders and keep valves closed and
cylinder caps installed on empty cylinders. Never use a cylinder for other than its intended use.
REFERENCES: See Safety and Operating Reference G.
HOT PARTS
Hot parts can cause serious burns. The area at and near the work being welded should be handled with proper gloves. Proper clothing should be worn
to prevent spatter or chipped slag from causing burns. Never pick up welded material until it has properly cooled.
REFERENCES: See Safety and Operating References A, B, H, & I.
FLYING DEBRIS CAN INJURE EYES
Wearing proper eye protective lenses can prevent debris from damaging the eye. Wear safety glasses with side shields or face shields.
REFERENCES: See Safety and Operating References B.
WELDING WIRE CAN PUNCTURE SKIN
Position the unit away from any part of the body, other people, and metal when threading.
REFERENCES: See Safety and Operating References A.
Safety and Operating References
A) ANSI Z49.1, “Safety in Welding and Cutting”
B) ANSI Z87.1, “Practice for Occupational and Educational Eye and Face Protection”
C) ANSI Z88.2, “Standard Practice for Respiratory Protection”
ANSI: American National Standard Institute, 1430 Broadway, New York, NY 10018
D) AWS F4.1, “Recommended Safe Practices for Welding and Cutting Containers”
AWS: The American Welding Society, P.O. Box 351040, 550 NW Lejeune Rd., Miami, FL 33135
E) NFPA 51B, “Fire Prevention in Cutting and Welding Processes”
F) NFPA-70, “National Electrical Code”
NFPA: National Fire Protection Association, Batterymarch Park, Quincy, MA 02269
G) CGA P-1, “Precautions for Safe Handling of Compressed Gases in Cylinders”
CGA: Compressed Gas Association, 1235 Jefferson Davis Hwy., Arlington, Va 22202
H) Code of Federal Regulations (OSHA) 29 CFR 1910
US: U.S. Government Printing Office, Washington, DC 20402
I) CSA Standard W117.2, “Safety in Welding, Cutting and Allied Processes”
CSA: Canadian Standards Association, 178 Rexdale Blvd., Rexdale, Ontario, Canada M9W 1R3
J) OTA-BP-E-53 Biological Effects of Power Frequency Electric & Magnetic Fields - Background Paper US Congress,
Office of Technology Assessment, General Conclusions Section, Washington D.C: US Government Printing Office, May 1989.
Summary of Contents for PRO II
Page 15: ... 13 Section 6 Parts PARTS MANUAL ...
Page 20: ......