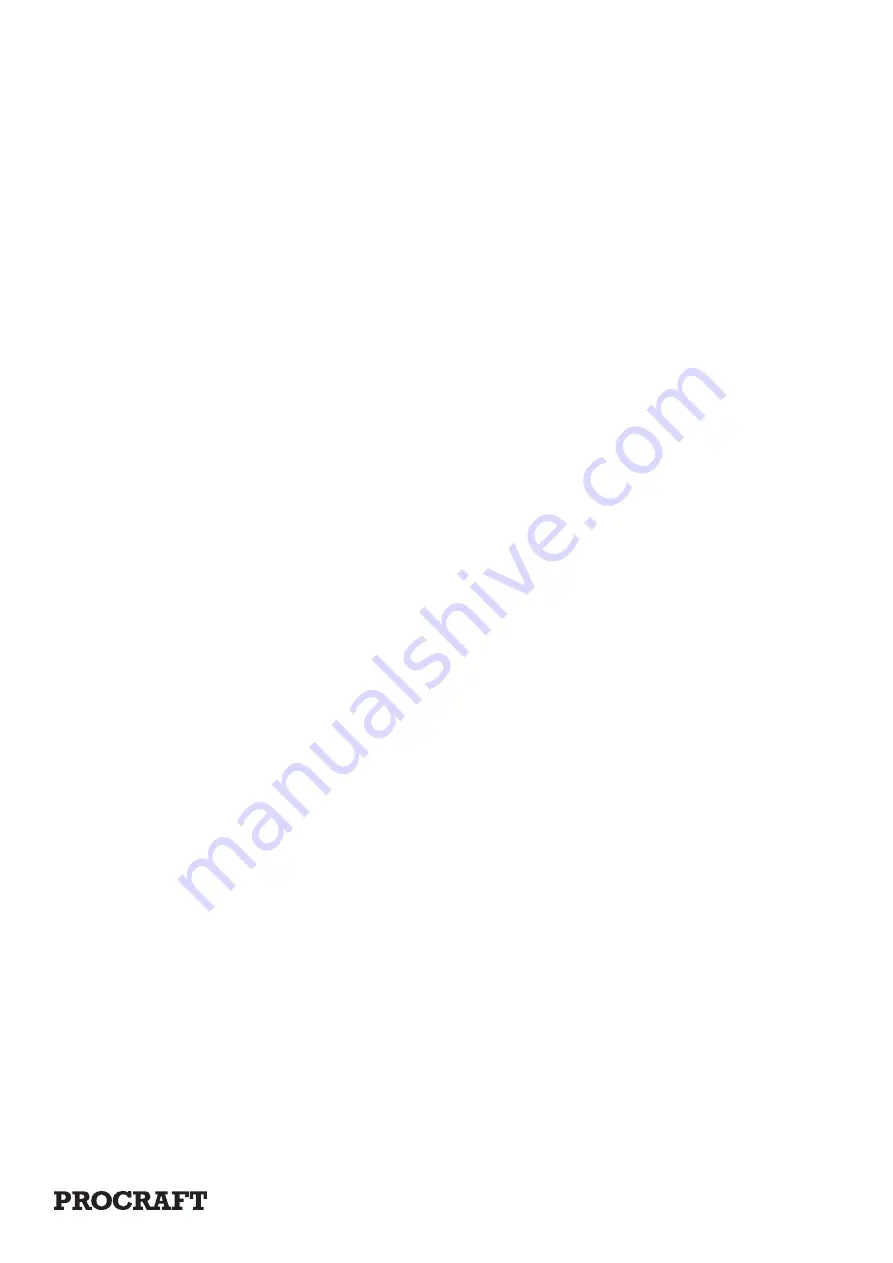
Page 10
MAINTENANCE
WARNING! Make sure the Power Switch of the WELDER is in it’s “OFF” position and that the tool is unplugged from the
electrical outlet before performing any inspection, maintenance, or cleaning procedures.
1. Before each use, inspect the general condition of the Welder. Check for loose cable connections, misalignment or
binding of the fan, cracked or broken parts, damaged electrical wiring, and any other condition that may affect its safe
operation. If abnormal noise or vibration occurs, have the problem corrected before further use. Do not use damaged
equipment.
2. Periodically recheck all nuts, bolts, and screws for tightness.
3. Periodically blow the dust from the cooling vents with compressed air.
4. Verify that the cooling fan is operational before welding.
5. If the unit repeatedly shuts down from thermal overload, stop all use. Have the welder inspected and repaired by a
qualified service technician.
6. Store the welder and accessories in a clean and dry location.
7. Periodically disassemble and clean the Torch Head components with steel wool. Replace burnt, cracked, distorted, or
coated components, Refer to the assembly drawing on page 11.
1. To gain access to the internal components of the unit, remove screws from Main Body Cover. The home user is strongly
advised not to remove the tool covers and not to attempt any electronic repairs. Any repairs must be completed by a
qualified technician. Opening the tool will void any warranties, and may result in damage to equipment or possible per-
sonal injury. Don’t do it.
2. On a daily basis check for any of the following problems: If any are found, take the tool to a qualified repair technician.
a. Abnormal vibration, sound or smell.
b. Abnormal heating at any cable connection.
c. Then fan does not work properly.
d. Any switch or control does not work properly.
e. Any damage to cables.
Storage: For your safety, please pile up the machines for less than three tiers, and fix them up with ropes.
6) Surrounding requirements:
• Dry and clean in-door place. Do not use in the rain.
• Surrounding temperature: -10°C~40°C
• Relative humidity:
≤
50% at 40°C;
≤
90% at 20°C
Keep the distance between the
• Surrounding temperature: -10°C~40°C
• Relative humidity:
≤
50% at 40°C;
≤
90% at 20°C
• Altitude level < 1000 m
Keep the distance between the
• Altitude level < 1000 m
Keep the distance between the Ø machine and walls above 20cm
• Keep the distance between two machines above 30cm
Protect the machine and gas cylinders from shakes and Ø shocks.
• Store machine in ventilation place and keep away from rain, snow and any caustic material.