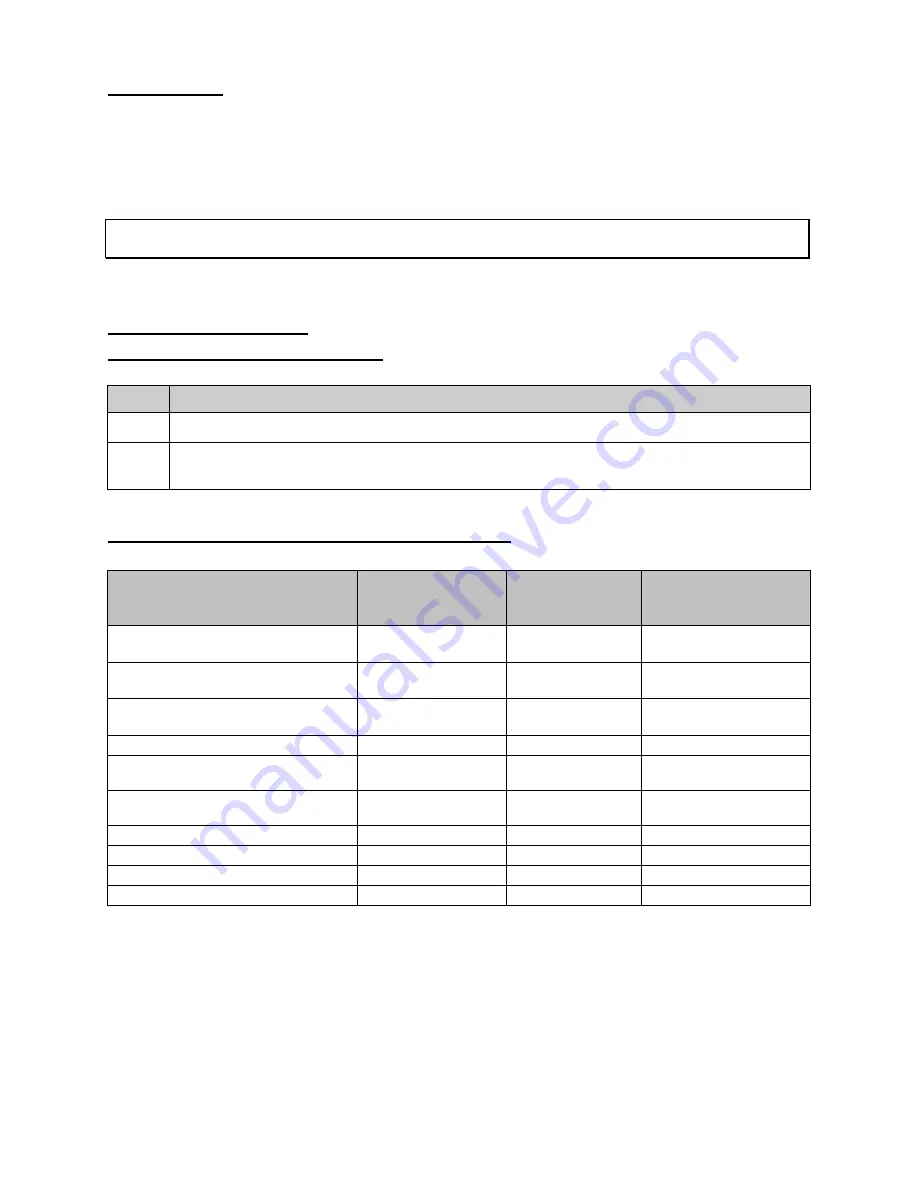
43
M-43-25
LUF-Series Lufran Manual
Revision - Date 03-01-04-18 Standard outlet, Standard Interface
Maintenance:
The LUF-series Lufran fluoropolymer inline water heater requires only a routine inspection every 6
months to check the operation of the various operation and safety devices. The maintenance procedures
listed here should only be performed by qualified technicians. Many of these devices require the control
system to remain operational during inspection, while others may be checked while the unit is completely
powered down.
Note:
Several maintenance tasks can be completed simultaneously while the cabinet access covers
are open and lockout/tagout procedures are in place.
Maintenance Schedule:
Categories of Electrical Hazards
Type
Description
1
Equipment is energized, but live circuits are covered or insulated to prevent accidental shock.
2
Equipment is energized and energized circuits of less than 24 VDC, 240 VA and 20 joules are
exposed to accidental contact.
Maintenance To Be Performed Every 6 Months:
Item to Inspect
Lockout / Tagout
Required (Y/N)
Electrical Hazard
Category (1-2)
Procedure Number
Outlet plumbing liquid level sensor,
top-half plumbing
N
1
M1
Outlet process sensor, column TC
sensor
N
1
M2
Leak detector (Optional)
N
1
M3
Purge gas flow switch
N
2
M4
Humidistat purge exhaust, humidistat
switch
N
2
M5
Pressure relief valve (PRV), bottom-
half plumbing
N
1
M6
Cabinet cooling fans
N
1
M7
SSR heat sink cooling fans
N
1
M8
Circuit breaker
N
2
M9
Safety Contactor
Y
2
M10
Summary of Contents for Lufran LUF Series
Page 63: ......