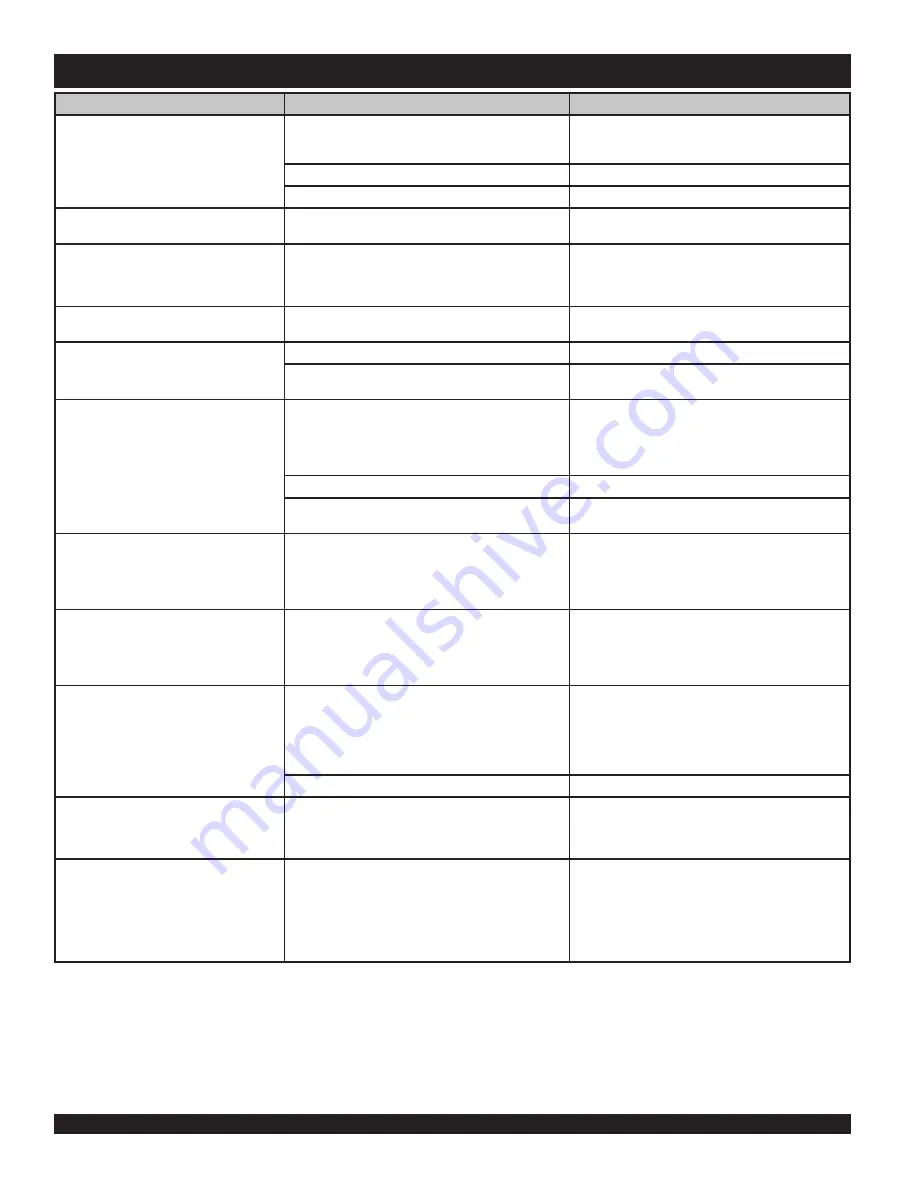
TroubleshooTIng
28
EmpyrE ElItE Xt InstallatIOn and OpEratIOn manual
prOBlEm
pOssIBlE CausE
sOlutIOn
Blower will not come on.
High limit switches may be shut off because
the water temperature is higher than aqua-
stat setting permits.
Wait for the water to cool down. Reset snap
disc, see page 9.
No electricity.
Check power supply.
Blower overheated.
Wait for blower to cool down.
Blower is on but no air in firebox.
Flapper unit flap stuck shut.
For information on a sticking flapper see
page 24.
The water overheated and boiled over.
After refilling the water, temperature is
below operating range, but there is no
power coming through to the blower.
The high limit switch (snap disc) has tripped
the circuit.
The high limit switch (snap disc) has a
manual reset. Press button to reset. To
locate snap disc see page 9.
There is some smoke coming from
the chimney most of the time.
Wood is too dry or bridged.
Burn only seasoned wood. Reposition wood.
Furnace overheats and boils.
Main door has been left open.
Close door.
Main door and/or ash clean out gaskets are
leaking.
Replace gaskets or adjust latches and/or
hinges.
Low heat output.
Wood moisture is too high causing the wood
to bridge. Note: when bridging happens there
is an air space between the wood and the
firebox floor. The air then exits the firebox
without causing the wood to burn.
Use seasoned wood. Cut wetter pieces 8
inches (20 cm) shorter than the firebox and
load the logs centered in the firebox. Split
the bigger logs. Place the logs carefully so
they will not bridge.
Fire has almost died out before refuelling.
Add wood before the fire has burned down.
Wood is hung up and bridged because of
incorrect length and loading.
Place logs centered over the brick slots/air
passage on the firebox floor.
Low heat output.
The brick slots/air passage in the firebox
floor is blocked by charcoal/ash.
Using the ash rake, always stir the firebox
charcoal/ash into the lower ash chamber
before adding wood. Limit the charcoal/
ash buildup and let the charcoal burn down
before adding wood.
It is difficult to get a fire started.
Brick slots on the floor of the firebox are
blocked.
Place small pieces of wood so air can flow
through. Avoid flat pieces of wood that could
block the air when laid flat on the firebox
floor. As you add more wood place the wood
so air can flow through.
Fire dies out with wood still left in
the firebox.
The furnace has been on the off cycle for too
long causing the wood to bridge or hang up.
Flapper is stuck shut from the furnace idling
too much.
In spring/fall when one load of wood lasts
more than 16 hours do not fill up the firebox.
To further avoid bridging, stack the wood so
the lowest part of the stack is in the centre.
In spring/fall use only 6 inch (15 cm) diam-
eter and smaller seasoned logs.
Not drawing enough heat from the furnace.
Increase the heat draw on the furnace.
Furnace water temperature is over
180°F (82°C) but no heat in the
building.
Circulating pump is off due to one or more of
the following: a bad connection, temperature
is set too low, valves are closed, air is in the
system or the water level is low.
Check for loose connections; open valves if
closed; bleed air out of system; add water if
level is too low.
Smoke coming from open loading
door.
Cause could be one or more of the follow-
ing: opening door too quickly, opening door
soon after loading wood, furnace blower is
off, loose wires, faulty switch/timer, too small
or too short a chimney, negative pressure in
furnace room.
Open slowly waiting 30 seconds after mov-
ing lever to the left; do not open when fire
is hot; switch blower on; move lever left
and right, blower should be on in the load
position; check limit switches/timer and
wire connections; install longer and bigger
chimney; increase venting to furnace room.
Summary of Contents for Empyre Elite XT
Page 1: ...Installation and Operation Instructions Empyre Elite XT Model 100 and 200...
Page 2: ......
Page 31: ......