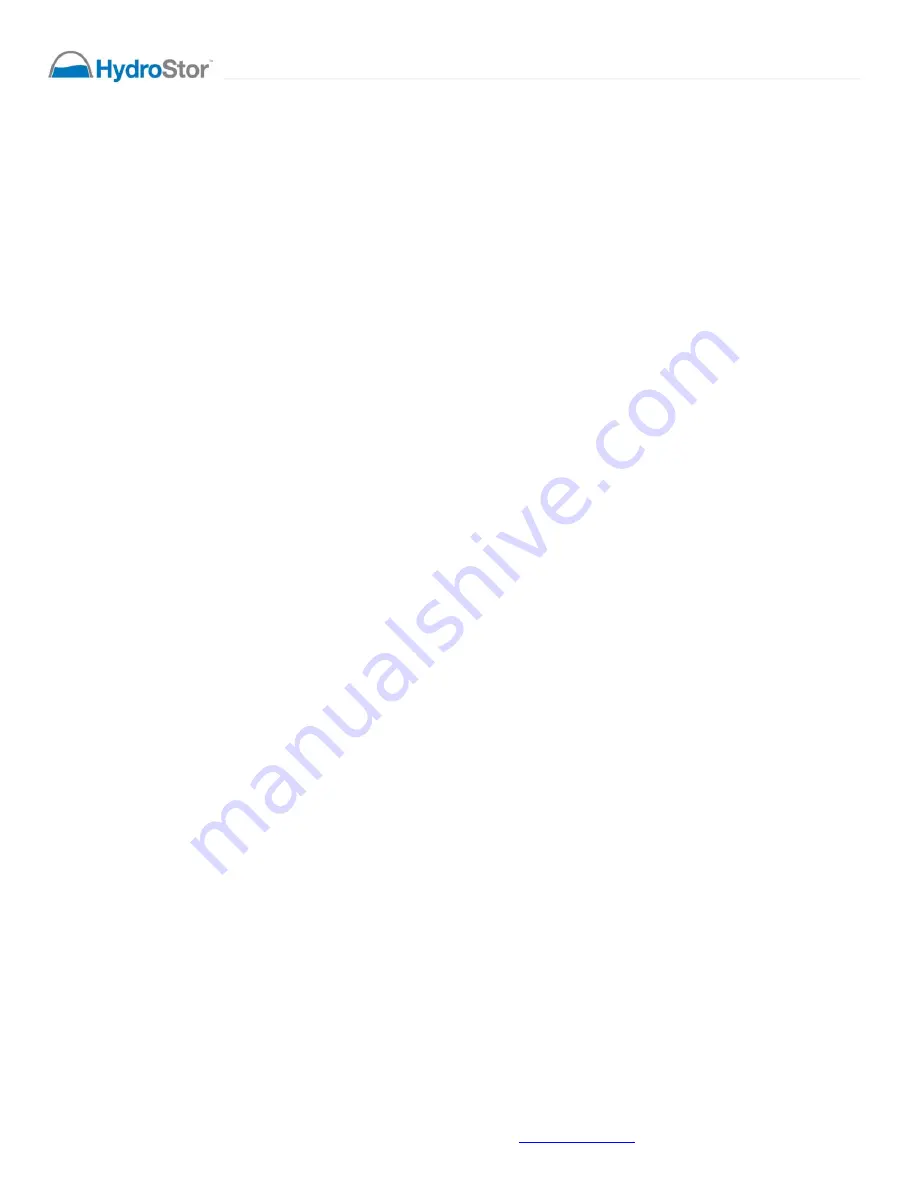
Design Guide
Page 8
©2015 Prinsco, Inc | 800.992.1725 |
05/15
3.0
Structural Design
3.1
Design
Installation of HydroStor Chambers should be accomplished in accordance with the manufacturer’s
instructions. When installed correctly the HydroStor product line is designed to meet or exceed the
American Association of State Highway and Transportation Officials (AASHTO) Load Resistance
Factor Design (LRFD) design factors for dead loads (earth fill) and live loads (vehicular traffic).
AASHTO vehicular live loads are designated as either a single axle 32kip load or tandem 25kip axle
loads. The conservative design is based on additional factors for impact and multiple vehicles. The
dead load applied is also subject to additional factors for safety.
Three dimensional models for the chambers were created. A Finite Element Analysis (FEA) was
then utilized to determine required part thickness, weight, and shape to maximize the structural
capacity of the product with an optimized profile. Maximum thrust, moment, local buckling, and
deflection as well as other factors in both short term and long term configurations were determined
from the FEA.
The HydroStor chambers are designed for use in normal buried conditions and are not
recommended for installation under structures, such as buildings, parking garages, or retaining
walls as these could provide additional loading for which the chambers were not designed.
3.2
Testing
As part of the design and evaluation program, HydroStor chambers have been installed in field
conditions to perform a variety of tests, including short term traffic loading, and continuous long
term testing and monitoring. The full scale testing was designed to test the limits of the chambers
and provide conclusive evidence that the product performs as designed and intended. Long term
testing of HydroStor products is ongoing.
3.3
Molding
HydroStor chambers are constructed of polypropylene resin by injection molding. The entire
system meets the design requirements of the AASHTO LRFD specifications as well as ASTM F2787
and ASTM F2418. The injection molding of the chambers provides a highly repeatable process for
maintaining precise quality control of the parts as well as several other benefits including
o
Precise control of minimum wall thicknesses
o
Precision fit for joints and end caps
o
Engraved instructions for installation
o
Handles on the Chambers
o
Uniform Material Placement
o
Consistent Structural Strength
3.4
Quality Control
HydroStor chambers are manufactured with stringent quality control measures in place. The
incoming raw materials are routinely tested to ensure compliance with the minimum requirements
of the resin for processing and end product performance. The chamber properties are measured at
industry standard intervals, ensuring proper performance when installed in accordance with the
manufacturer’s instructions.
Summary of Contents for HydroStor HS180
Page 1: ...DESIGN GUIDE...
Page 35: ......