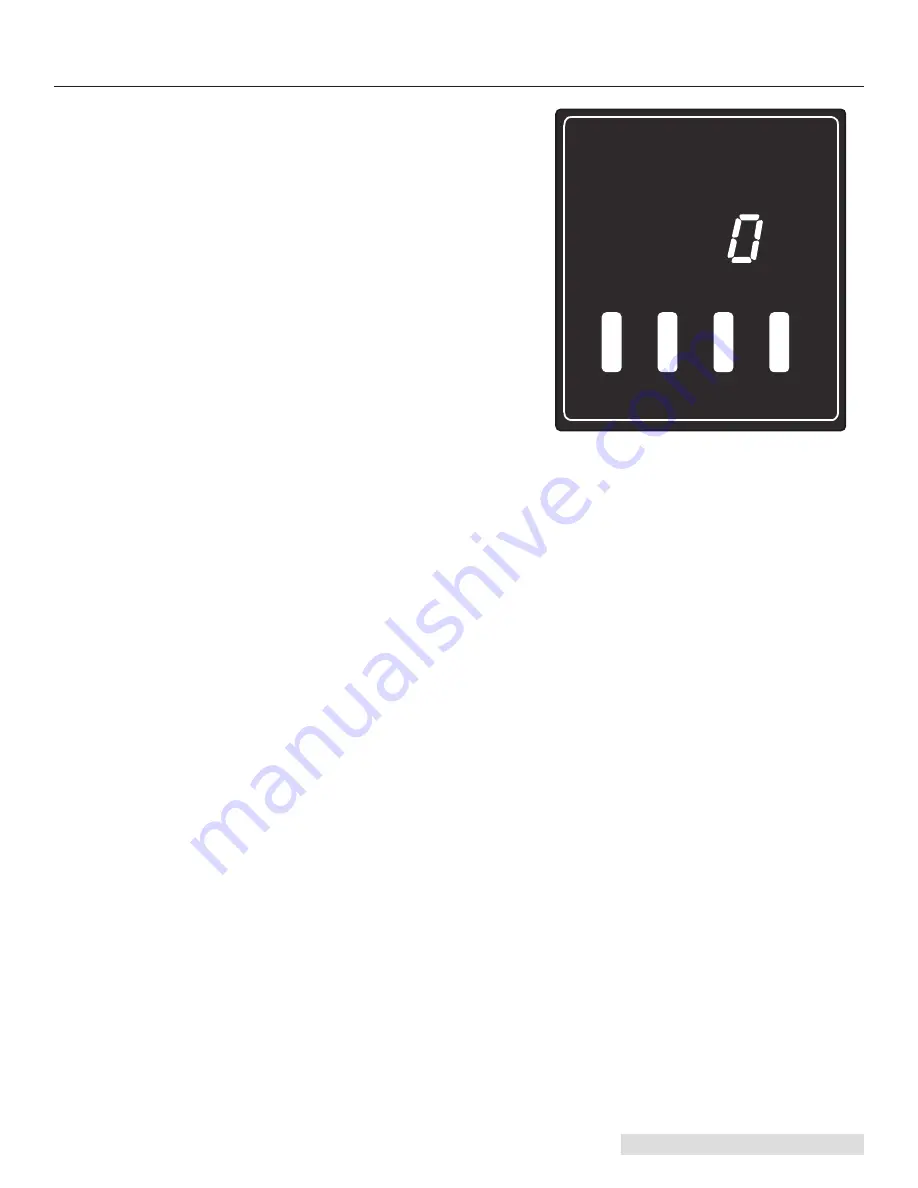
DX850e Label Dispenser 11
The Control Panel can be used to start and stop
dispensing of labels, display label counts and
other advanced functions.
Start/Stop Button:
Starts or stops the motor
depending on whether or not the label sensor is
tripped. Note: If sensor does not get triggered in
a 24” run, the motor will stop.
a. If the motor is in Stop Mode the display
flashes. Otherwise the display is on
solid.
b. If held for 2 seconds it will toggle the
label counter between Decrement and
Increment Mode as indicated by the
lower right decimal point. If the
decimal point is on, the label counter
is in Decrement Mode.
Counter Reset Button:
Pressing this button will
reset the label counter if held for 2 seconds.
+ Button:
Pressing this button for 2 seconds will increase the label counter. It will repeat
advance if held.
- Button:
Pressing this button for 2 seconds will decrease the label counter. It will repeat
advance if held.
Special Setup Modes:
1. To set the LED Display Intensity: Press and hold the Start/Stop Button and the + Button until
the display changes to “LED”. Then press the + or – buttons to adjust the LED intensity.
2. Half-Speed Mode: To start system in Half-Speed Mode for wide label stock: Pr ess and hold
the – Button during power-up.
Section 4: Using the Control Panel
Counter
Reset
+
-
Start/
Stop
Summary of Contents for DX850e
Page 15: ......
Page 16: ...P N 511260 201011...