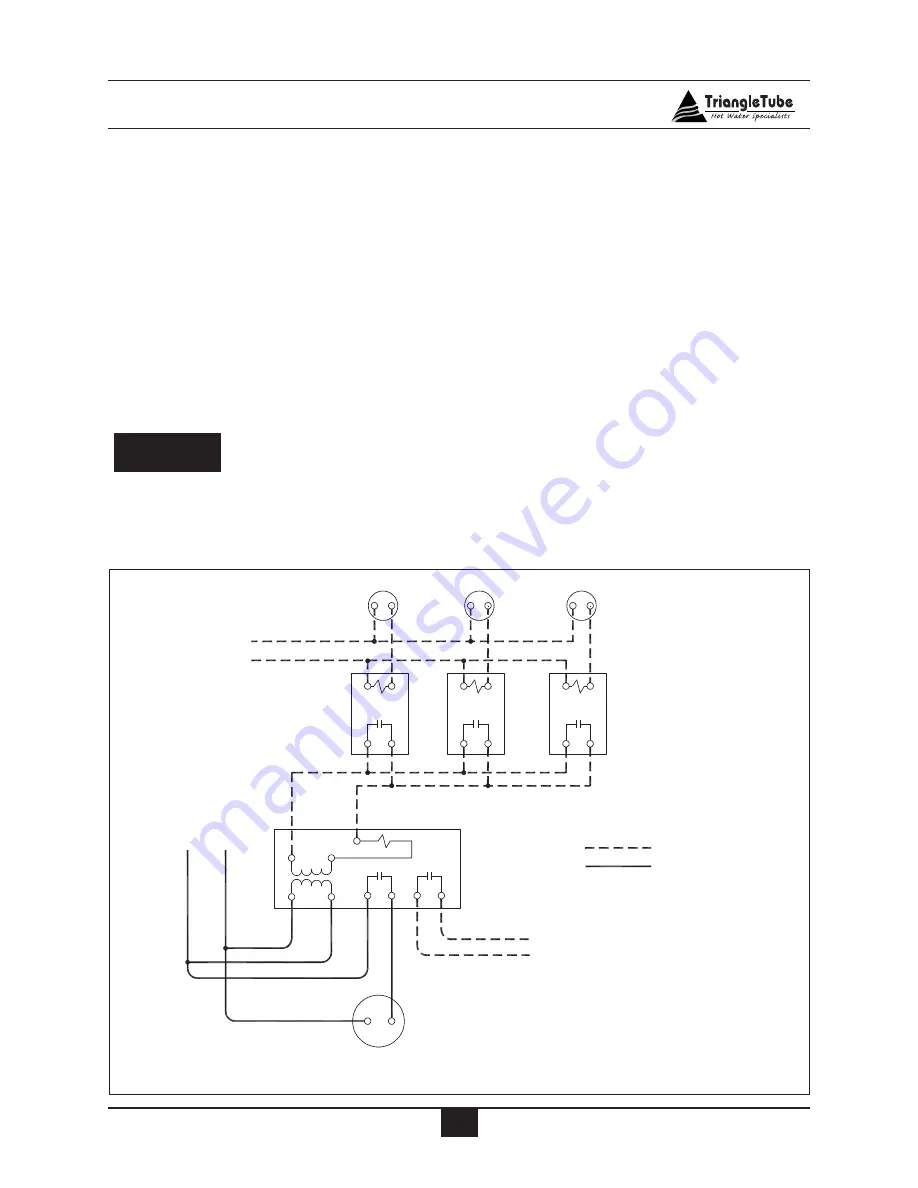
34
External Wiring
System Circulator - Zone Valve Application
To energize the system circulator shown as
item 12 in Fig. 11 page 22 reference Fig. 21.
Installer to provide a Transformer / Relay such
as Honeywell R8285 or equivalent and Zone
Valves with isolated end switch such as
Honeywell V8043 or equivalent.
Outdoor Temperature Limit
1. The PRESTIGE may operate with a vari-
able boiler operating temperature using the
Triangle Tube outdoor sensor, see pages 48
through 50 for installation and set-up.
If the installer opts for a fixed operating
temperature for the boiler system, the
outdoor sensor is not required and
should not be installed.
Additional 24V Limit Wiring
The PRESTIGE provides 24V terminal con-
nections for additional limit controls as shown
in Fig. 20 page 32. These limit terminal con-
nections will provide a "hard" lockout requir-
ing a manual reset of the PRESTIGE control,
or a “soft” lockout in which the PRESTIGE
will automatically reset.
NOTICE
24 V
Transformer
by Others
Honeywell V8043
Zone Valves
or Equivalent
Honeywell R8285D
Transformer / Relay
or Equivalent
24V Terminal Strip
System Circulator
24V Low Voltage Wiring
120V High Voltage Wiring
Room Thermostats
H
N
120V
R
C
G
1
3 4
6
7
8
To Prestige
Fig. 21: Secondary System Circulator Wiring