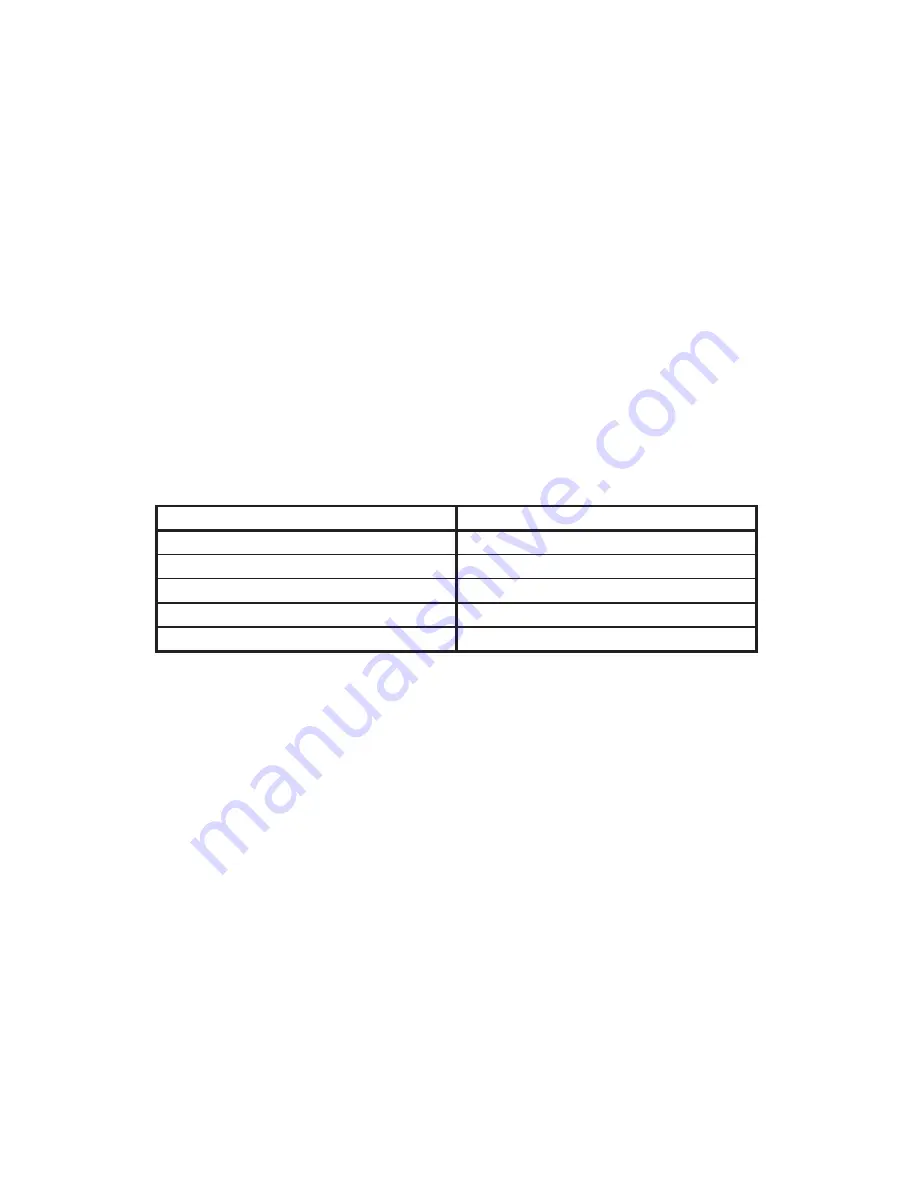
4222MCM101 1
INTRODUCTION
This configuration manual
contains the necessary information for configuring a PR 4222 device which is connected to a
PR 4511 Modbus RTU enabler.
Modbus
is a “master-slave” system,
where the “master” communicates with one or multiple “slaves”.
The master typically is a PLC (Programmable Logic Controller), DCS (Distributed Control
System), HMI (Human Machine Interface), RTU (Remote Terminal Unit) or PC.
The three most common Modbus versions used are: MODBUS ASCII, MODBUS RTU and
MODBUS/TCP.
In Modbus RTU, data is coded in binary, and requires only one communication byte per data
byte. This is ideal for use over multi-drop RS485 networks, at speeds up to 115,200 bps.
The most common speeds are 9,600 bps and 19,200 bps.
Modbus RTU is the most widely used industrial protocol and is supported by the 4511.
Modbus RTU
To communicate with a slave device, the master sends a message containing:
Device Address - Function Code - Data - Error Check
The Device Address
is a number from 0 to 247.
Messages sent to address 0 (broadcast messages) will be accepted by all slaves, but numbers
1-247 are addresses of specific devices. With the exception of broadcast messages, a slave
device always responds to a Modbus message so the master knows the message was received.
4511 Supported Modbus Function Codes
Command
Function code
Read Holding Registers
03
Read Input Registers
04
Write Single Register
06
Diagnostics
08
Write Multiple Registers
16
The Function Code
defines the command that the slave device is to execute, such as
read data, accept data, report status. Some function codes have sub-function codes.
The Data
defines addresses in the device’s memory map for read functions,
contains data values to be written into the device’s memory, or contains other information
needed to carry out the function requested.
The Error Check
is a 16-bit numeric value representing the Cyclic Redundancy Check (CRC).
Maximum number of registers which can be read or written at once:
For a read command, the limit is 8 registers at a baud rate up to 38,400 bps,
16 registers @ 57,800 bps and 32 registers @ 115,200 bps.
For a write command, the limit is 123 registers at baud rates up to 115,200 bps.
4511 Modbus parameter settings
Automatic Baudrate Detection:
Yes - can be configured ON or OFF
Supported baudrates:
2400, 4800, 9600,
19.2k
, 38.4k, 57.6k, 115.2k bps
Parity Mode:
Even
, Odd or None parity
Stop Bits:
1
or 2 stop bits
Response delay:
0...1000 ms
(0 ms = default)
Modbus slave addressing range:
1 - 247
(247 = default address)
Modbus Parameter Storage:
Saved in non-volatile memory in the 4511 device
(Factory Default Values are marked in
bold
)
Modbus RTU segment line termination
A 120 Ohm resistor should be installed on both ends of a RS485 Modbus RTU segment loop to
prevent signal echoes from corrupting data on the line.