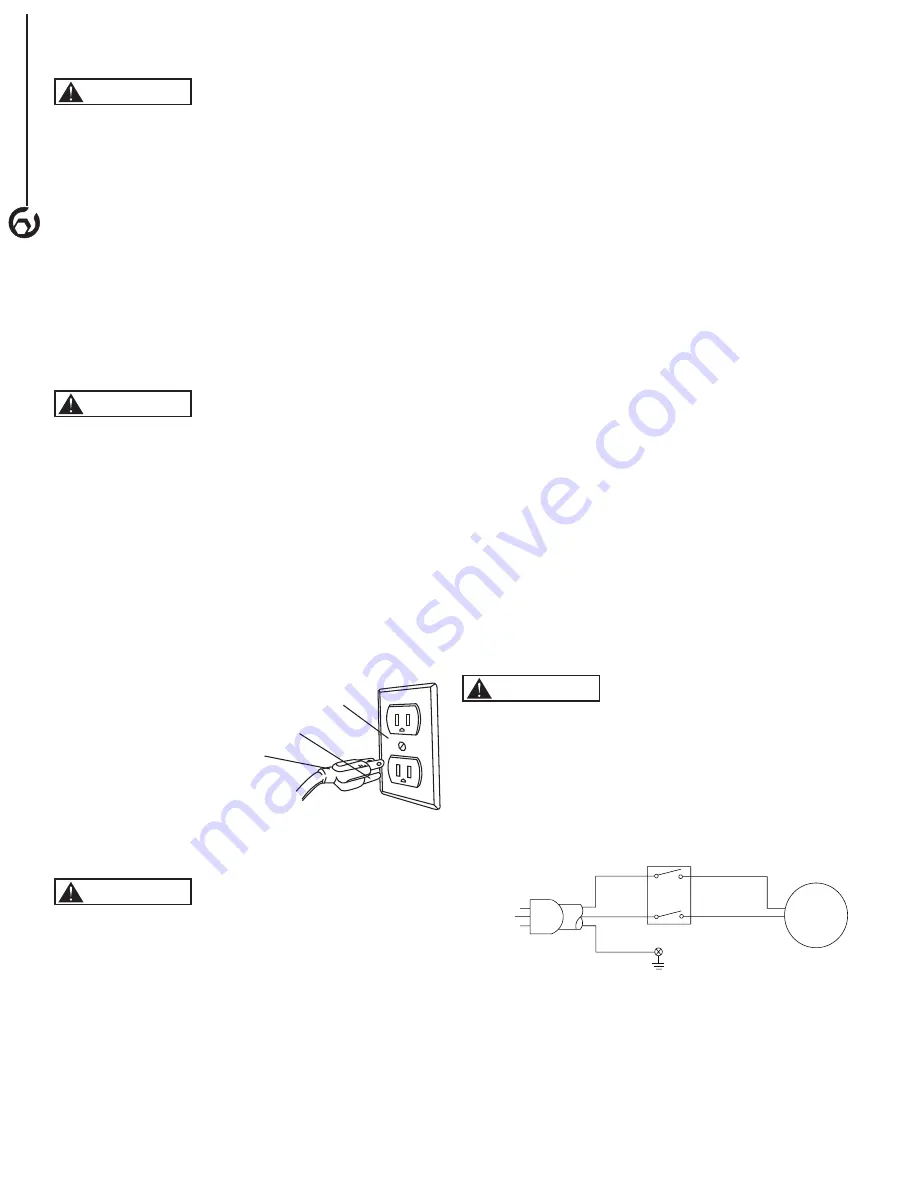
POWER SOURCE
WARNING
Do not connect sander to the power source until
all assembly steps have been completed.
The motor is designed for operation on the voltage and
frequency specified. Normal loads will be handled safely
on voltages not more than 10% above or below specified
voltage. Running the unit on voltages which are not within
the range may cause overheating and motor burn-out.
Heavy loads require that the voltage at motor terminals be
no less than the voltage specified on nameplate.
• Power supply to the motor is controlled by a single pole
locking rocker switch. Remove the key to prevent
unauthorized use.
GROUNDING INSTRUCTIONS
WARNING
Improper connection of equipment grounding conductor
can result in the risk of electrical shock. Equipment should
be grounded while in use to protect operator from
electrical shock.
• Check with a qualified electrician if you do not
understand grounding instructions or if you are in doubt
as to whether the tool is properly grounded.
• This tool is equipped with an approved cord rated at
150V and a 3-prong grounding type plug (see Figure 6)
for your protection against shock hazards.
• Grounding plug should be plugged directly into a
properly installed and grounded 3-prong grounding type
receptacle, as shown (see Figure 6).
• Do not remove or alter grounding prong in any manner.
In the event of a malfunction or breakdown, grounding
provides a path of least resistance for electrical shock.
WARNING
Do not allow fingers to touch the terminals of plug when
installing or removing from outlet.
• Plug must be plugged into matching outlet that is
properly installed and grounded in accordance with all
local codes and ordinances. Do not modify plug
provided. If it will not fit in outlet, have proper outlet
installed by a qualified electrician.
• Inspect tool cords periodically, and if damaged, have
repaired by an authorized service facility.
• Green (or green and yellow) conductor in cord is the
grounding wire. If repair or replacement of the electric
cord or plug is necessary, do not connect the green (or
green and yellow) wire to a live terminal.
Properly Grounded Outlet
3-Prong Plug
Grounding Prong
Power Cord
Switch
Motor
4
ASSEMBLY
Figure 6
Figure 7
EXTENSION CORDS
• The use of any extension cord will cause some drop in
voltage and loss of power.
• Wires of the extension cord must be of sufficient size to
carry the current and maintain adequate voltage.
• Use the table to determine the minimum wire size
(A.W.G.) extension cord.
• Use only 3-wire extension cords having 3-prong
grounding type plugs and 3-pole receptacles which
accept the tool plug.
• If the extension cord is worn, cut or damaged in any
way, replace it immediately.
Extension Cord Length
Wire Size…………….. A.W.G.
Up to 25 ft…………… 16 gauge
NOTE:
Using extension cords over 25 ft. long is not
recommended.
MOTOR
The sander is assembled with motor and wiring installed.
The electrical wiring schematic is shown in Figure 9.
The permanently split capacitor motor has the following
specifications:
Horsepower (Peak HP) . . . . . . . . . . . . . . . . . . . . . . . . . 1/3
Voltage . . . . . . . . . . . . . . . . . . . . . . . . . . . . . . . . . . . . 120
Amp. . . . . . . . . . . . . . . . . . . . . . . . . . . . . . . . . . . . . . . . 5.5
Hertz . . . . . . . . . . . . . . . . . . . . . . . . . . . . . . . . . . . . . . . .60
Phase. . . . . . . . . . . . . . . . . . . . . . . . . . . . . . . . . . . . .Single
RPM. . . . . . . . . . . . . . . . . . . . . . . . . . . . . . . . . . . . . . .3450
ELECTRICAL CONNECTIONS
WARNING
All electrical connections must be performed by a qualified
electrician. Make sure tool is off and disconnected from
power source while motor is mounted, connected, recon-
nected or anytime wiring is inspected.
Motor and wires are installed as shown in wiring schemat-
ic (See Figure 7). Motor is assembled with approved,
3-conductor cord to be used at 120 volts.
The power lines are inserted directly onto the switch. The
green ground line must remain securely fastened to the
frame to properly protect against electrical shock. The
power supply to the motor is controlled by a single pole
locking rocker switch.
• Remove the key to prevent unauthorized use.
Summary of Contents for BD4800
Page 12: ...4 X 8 BELT DISC SANDER PARTS ILLUSTRATION 10 PARTS LIST 10 ...
Page 16: ......