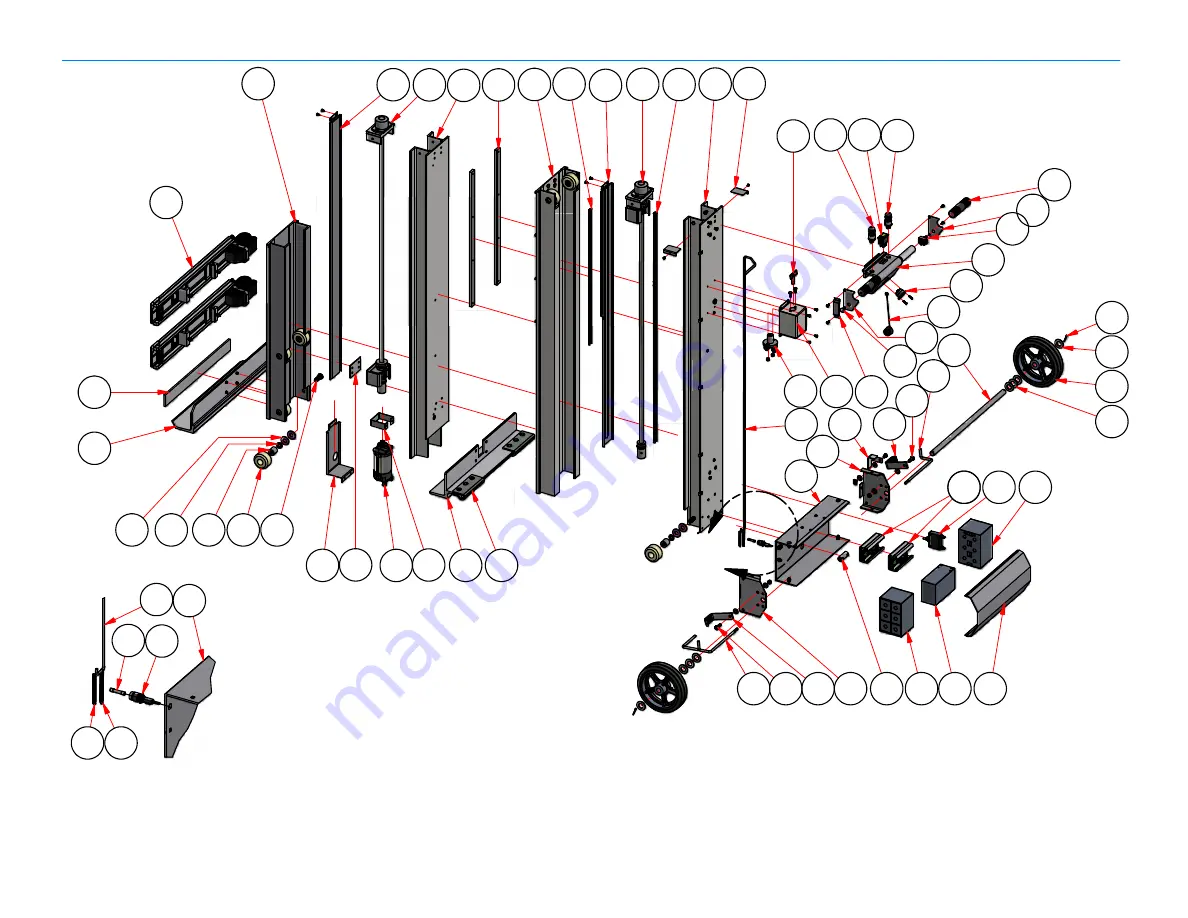
DETAIL A
POWERMATE MODEL LE-1, LE-2 with BATTERY SWITCH
REPLACEMENT COMPONENT DRAWING
PowerMate
®
Operation Manual
A
61
57
62
48
48
43
60
42
41
46
45
44
24
25
36
34
32
33
32
31
30
27
26
56
22
58
50
6
59
2
7
3
6
19
11
21
17
16
1
15
14
13
12
20 18
10
4
8
9
39
54
52
40
28
47
22
35
51
5
40
44
55
47
23
49
38 37
35
29
26
27
4.03
PN 013500 Rev.D2 EC
1st sheet of 013500 EC
Eng. 12/ 12/ 12