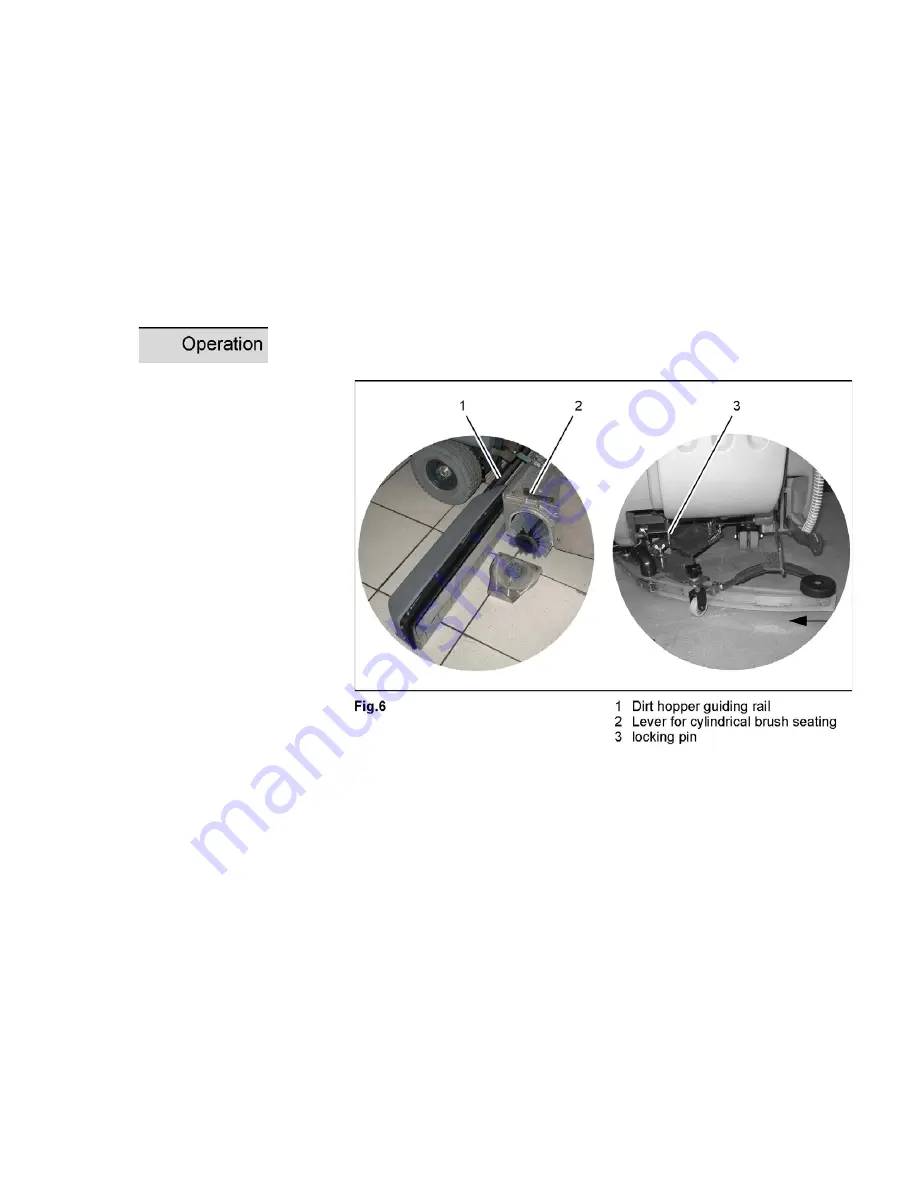
Dirt hopper guiding rail (Fig. 6/1)
The dirt hopper located at the cylindrical
brush deck is fastened by a guiding rail.
This dirt hopper may be easily removed for
cleaning.
Lever for cylindrical brush seating (Fig.
6/2)
This lever (both sides) is used to re-
lease/lock the cylindrical brush seating. The
cylindrical brushes may be easily removed
without tools.
Swing aside squeegee
Swing the squeegee aside in lifted position
to allow passage through narrow
clearances. This can be done by foot or by
hand by swinging the squeegee to the left
in the area of the deflector bail / roller
bumper until the locking pin (Fig. 6/3)
catches. In order to release locking of the
squeegee, actuate the hand lever (Fig. 5/3)
of the squeegee lift mechanism (lowering).