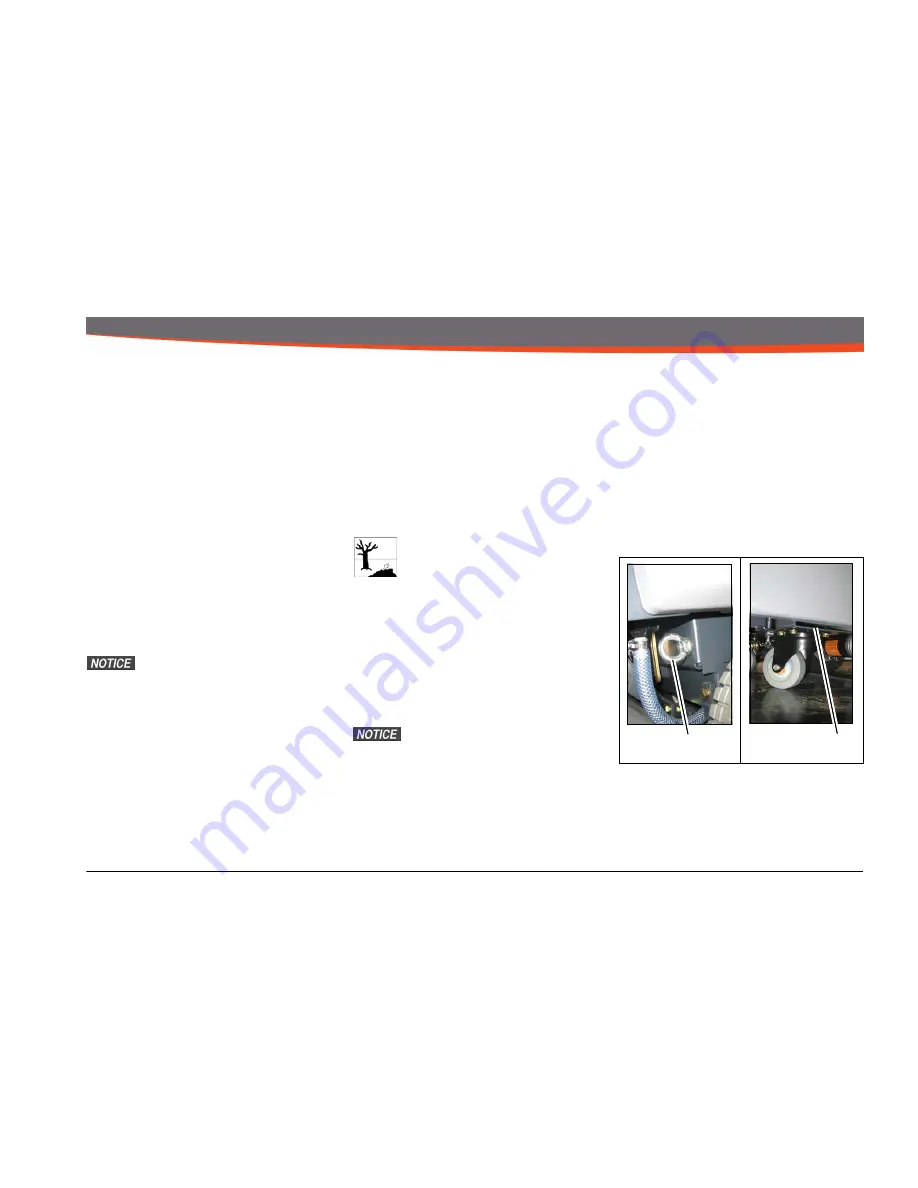
11
First Operation
2.5
Operation
1. Switch on the machine.
2. Use lever (Fig. 5/3) to lower squee-
gee. Vacuum motor switches on au-
tomatically.
3. Switch on solution supply by means
of tip-switch (Fig. 4/14).
4. Adjust solution amount by means of
tip-switch (Fig. 4/13) to lower brush
deck. Solution supply switches on
automatically.
5. Use the speed control knob (Fig. 4/
16b) to adjust the work speed. Use
the direction switch (Fig. 4/16a) to
select forward or reverse. Pull the
bail handle (Fig. 4/16c) to start mov-
ing.
Start moving machine imme-
diately after switching on the
brush deck, otherwise the
brushes leave traces on the
floor. Lift brush deck before
passing over steps and other
obstacles.
2.6
Stop Machine
When the bail handle is released it au-
tomatically returns to the neutral positi-
on. The machine stops. Protect the
machine against unintentional move-
ments or against being inadvertently
started.
2.7
After Work
1. Move machine to a suitable site for
maintenance.
2. Stop machine, lift squeegee and
brush deck and remove the key.
3. Empty and clean recovery tank.
Observe the legal directives
and local regulations for dispo-
sal of detergents.
4. Check solution filter.
5. Check seals and suction hose.
6. Check operating fluid levels, function
and setting.
7. Charge batteries.
8. Clean the machine.
Empty the solution tank before shutting
down the machine for a longer time.
Do not clean the electrical
parts by means of high-pressu-
re cleaning equipment.
2.8
Transporting the machine
To transport the machine to the work ar-
ea, switch it on, lift-out squeegee and
brush deck, pull the bail handle start
movement.
2.9
Tie-down points
IWhen transporting on a vehicle or trai-
ler, the machine has to be secured. Tie
the machine down firmly by using the
front eye bolts (Fig. 2/1) and the rear
chassis (Fig. 2/2) as tie-down points.
Fig.2
1
2
Summary of Contents for Phoenix 24
Page 1: ...User Manual Phoenix 24...
Page 39: ...39 Maintenance and Care NOTES...
Page 40: ...40 Maintenance and Care...
Page 41: ...41 Maintenance and Care...