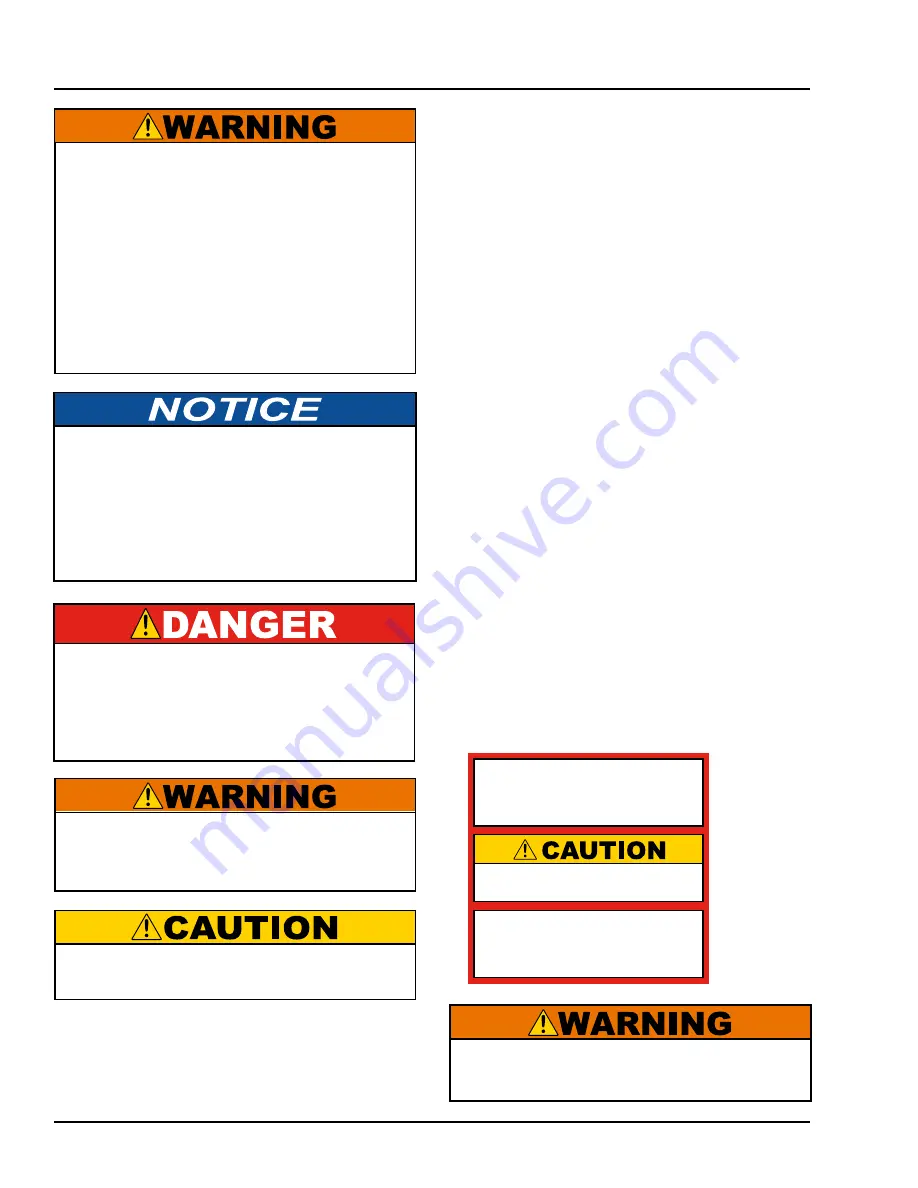
16
4111-0008 — April 2017
June 2017
1. Disconnect the external lifting device and chains
from the lifting brackets.
2. Complete all welding. Clean and paint all welds.
3. Install hydraulic hoses and fill system.
4. Connect all electrical connections .
5. Purge system (see p.17).
6. Connect hoist cylinder (see p.17)
7. Lower dock leveler check to make sure the
leveler goes into float mode (about 15” above
dock floor) allow to dock to float to full below
position. Make sure the dock makes contact with
pit floor. Push and hold the RAISE button until
the leveler turns off and the BLUE stored light
comes on.
8. Check the lip operation: Lower dock leveler
check to make sure the leveler goes into float
mode (about 15” above dock floor) allow to dock
to float to below dock. Push and hold the RAISE
button until the leveler turns off and the Blue
stored light comes on.
9. Install the Placard(s) (D), in close proximity to the
control box and in plain sight.
10. Test leveler for operation.
Put New Dock Leveler Into Service
INSTALLATION
File Name: 1751-0490 REV B
Decal Size: 3 x 2.875
ATTENTION INSTALLER:
Replace rear plug with
breather cap
Do not overfill
Oil should fill ½ site glass
Use ULTRA VIS HVI 15 or
MIL SPEC 5606
Questions Call: 800.643.5424
1751-0490 Rev B
Following start-up or if the platform is raised using
an external lifting device or the hydraulic system
is opened to atmosphere, air will enter into the
hydraulic system.
Whenever this happens, purge air from hydraulic
system fully.
DO NOT grind or weld if hydraulic fluid or other
flammable liquid is present on the surface to be
ground or welded.
DO NOT grind or weld if uncontained hydraulic
fluid or other flammable liquid is present. Stray
sparks can ignite spills or leaks near the work area.
Always clean up the oil leaks and spills before
proceeding with grinding or welding.
Always keep a fire extinguisher of the proper type
nearby when grinding or welding.
DO NOT connect the dock leveler electrical wiring
and ground connections until all welding has been
completed.
DO NOT ground welding equipment to any
hydraulic or electrical components of the dock
leveler. Always ground welding equipment to the
dock leveler frame, NEVER to the platform.
ALWAYS stand clear of dock leveler lip when
working in front of the dock leveler.
Post safety warnings and barricade the work
area at dock level and ground level to prevent
unauthorized use of the dock leveler before
installation has been completed.
Only trained installation professionals with the
proper equipment should install this product.
Summary of Contents for VS series
Page 44: ...42 4111 0008 April 2017 June 2017 Centra Power Hydraulic Components PARTS A B E D F G I H C ...
Page 47: ...45 4111 0008 April 2017 June 2017 This page was left intentional left blank PARTS ...
Page 53: ...51 4111 0008 April 2017 June 2017 PARTS This page was left intentional left blank ...