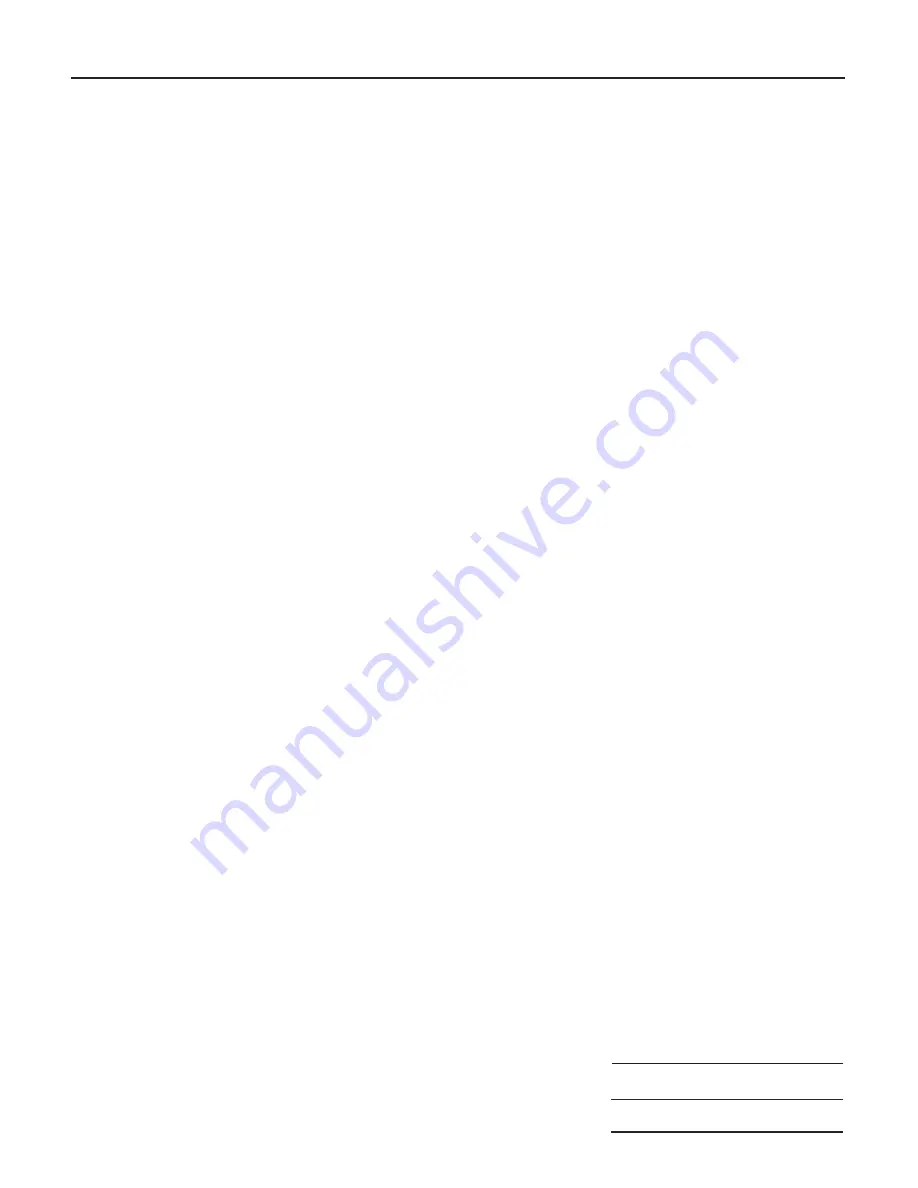
Operating Instructions
Use of Sockets
Use high quality, industrial impact sockets at all times. Ensure that sockets are rated to accept the full torque output
of the torque wrench that they are to be used with. Regularly check the socket for cracks and flaws, if any sign of
damage is evident, discard it immediately as a damaged socket breaking under load could cause equipment dam-
age or Operator injury.
Long reach or deep sockets are not recommended for use with hydraulic torque tools, as they tend to make the
wrench and socket unstable. However, some applications demand the use of long reach sockets, therefore it is
imperative that support is provided for both the socket and reaction facility. The same applies to socket accessories
such as extension bars, knuckle joints (not recommended), etc.
Setting Torque
Setting Up Prior to Operation
Setting up the equipment only takes a few minutes and some simple checks during set up will aid in the success of
the torquing operation.
• Obtain the torque value that is to be used for the tightening operation.
• Ensure that the bolt threads, nut threads and nut to flange contact faces are liberally coated with anti-seize lubri-
cant of known friction co-efficient. Ensure that the lubricant friction co-efficient matches that which has been used
to derive the torque value.
• Make sure that the torque wrench is suitable to deliver the required torque. Should the torque value exceed 80%
of the torque wrench output, consider using a higher capacity torque wrench.
• Use the ‘Pressure – Torque Conversion Chart’ for the particular torque wrench to be used (supplied with the
torque wrench) to obtain the required pump pressure.
• Make sure that the socket to be used is of the correct type and size. A poor fitting or oversize socket will damage
nuts, induce inaccurate bolt loads and possible cause operator injury.
• Place the proper size impact socket on the square drive and secure it properly with the locking ring and pin.
Make sure the square drive is fully engaged into the socket.
• Place the wrench and socket on the nut. Make sure the socket is fully engaged on the nut.
• Make sure the reaction arm is placed firmly against a stationary object such as an adjacent nut, flange, equip-
ment housing, etc.
NOTE: When positioning the wrench, make sure the hose connection will not hit any stationary object. This may
result in snapping a hose connection or breaking the coupler connection.
• Apply momentary pressure to the system to ensure proper wrench placement.
Setting Torque
Electric and Air Pumps
1. Make sure the system is fully connected and the proper power supply is available.
2. Use the Pressure/Torque conversion chart supplied with the wrench to find the required pressure setting.
NOTE: On electric or air pumps, this pressure is set on the pump.
3. Turn on the pump.
4. Press and hold the remote control button.
5. Check the pressure on the gauge.
6. Increase or decrease pressure as required by loosening the locking ring on
Sheet No.
6 of 12
Rev
Date: 16 July 2007