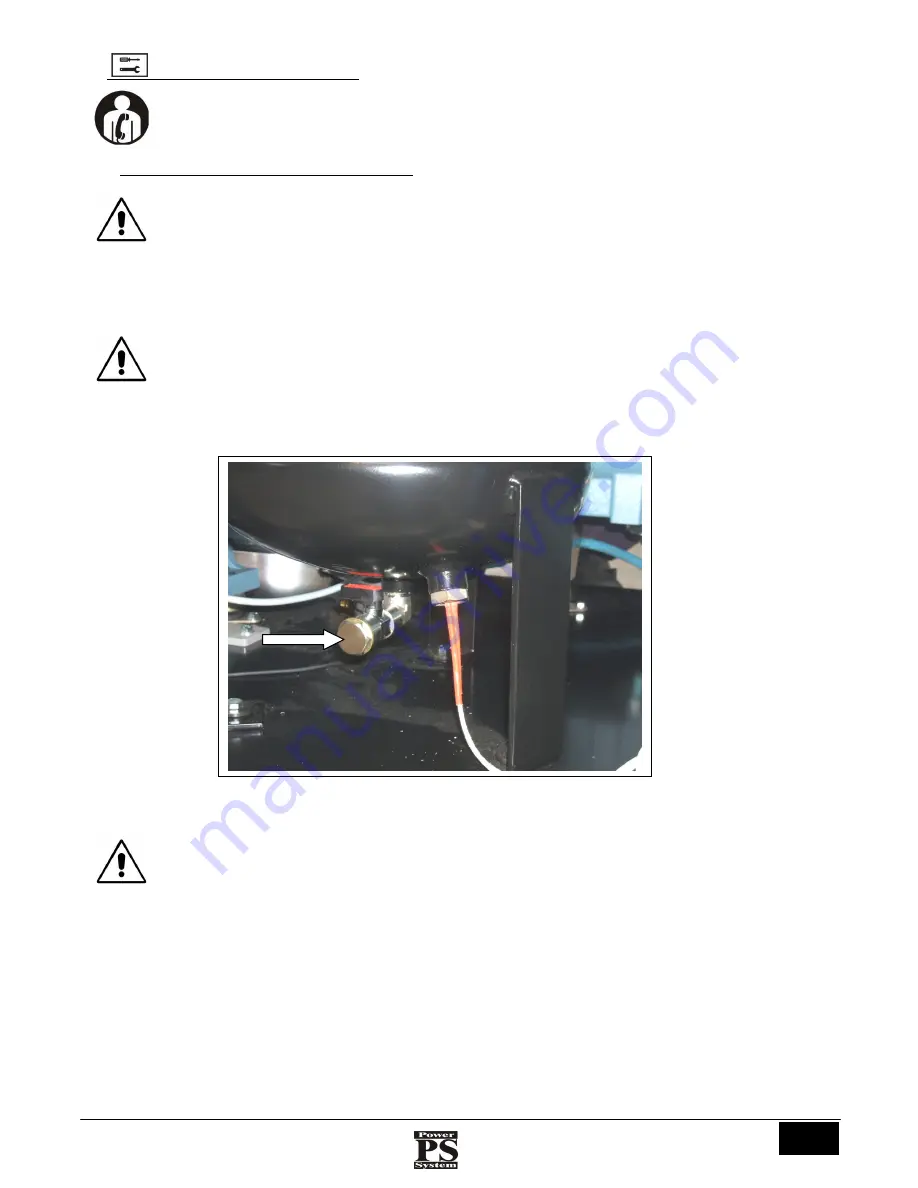
Istruzioni per l’uso e manutenzione
Cod. OQ7.5ARG114 – GB
Emiss. 19-01-11 Rev. 0 - Agg. /
45
POWER SYSTEM SRL
Via dell’Emigrante, 11/13 - 36040 Brendola (VI) Italia
25
SPECIAL MAINTENANCE
By special maintenance we mean all the activities aimed at maintaining the conditions of use and operation of the
equipment with various types of intervention performed exclusively by the manufacturer’s technician.
25.1 CHANGING THE OIL AND THE OIL FILTER
ALWAYS CHECK THE OIL LEVEL WITH THE MACHINE SWITCHED OFF
.
Procedure to be followed for changing the oil and the oil filter:
1. Stop the machine with the stop pushbutton on the electronic board.
2. Switch off the power: turn the isolating switch to “0” position and block it with the padlock.
3. Ensure that there is no pressurized air or oil in the oil reservoir.
AIR AND OIL UNDER HIGH PRESSURE CAN CAUSE SERIOUS INJURY. SHUT DOWN THE
COMPRESSOR AND RELIEVE THE SYSTEM OF ALL PRESSURE BEFORE REMOVING VALVES,
CAPS, PLUGS, FITTINGS, BOLTS AND FILTERS.
4. Always completely empty the circuit. (It is best to do this operation when the oil is still hot since it is more fluid and will drain
better).
5. To drain the circuit just unscrew the cap and turn on the tap
6. When you have finished draining, remember to close the cap and turn off the tap and fill the tank with oil up to the reference mark
(fig. 11).
USED OIL MUST BE DISPOSED OF IN CONFORMITY WITH THE LOCAL REGULATIONS IN FORCE.
7. Fill the tank to the required level (fig. 11 green zone). When the compressor starts the level will fall because the oil will fill the
parts of the circuit; keep the oil level above the minimum mark.
8. During idling or after stopping, some oil will return to the tank and the oil level may increase as a result.
DO NOT DRAIN ANY OIL TO ADJUST THE LEVEL. The next time it starts, the oil will fill the system again and the level will
indicate the using conditions.
DO NOT OVERFILL OR THERE WILL BE OIL LEAKS (in the event of excess oil, the indicator in fig. 11 will be in the yellow
zone).
9. Use only CLEAN containers and funnels so that no dirt gets into the tank. Store the oil in a clean place. Changing the oil
incorrectly does not offer any advantage.
10. Start the machine, let it run under load for about 5 minutes, check the oil level and ensure that there are no leaks.