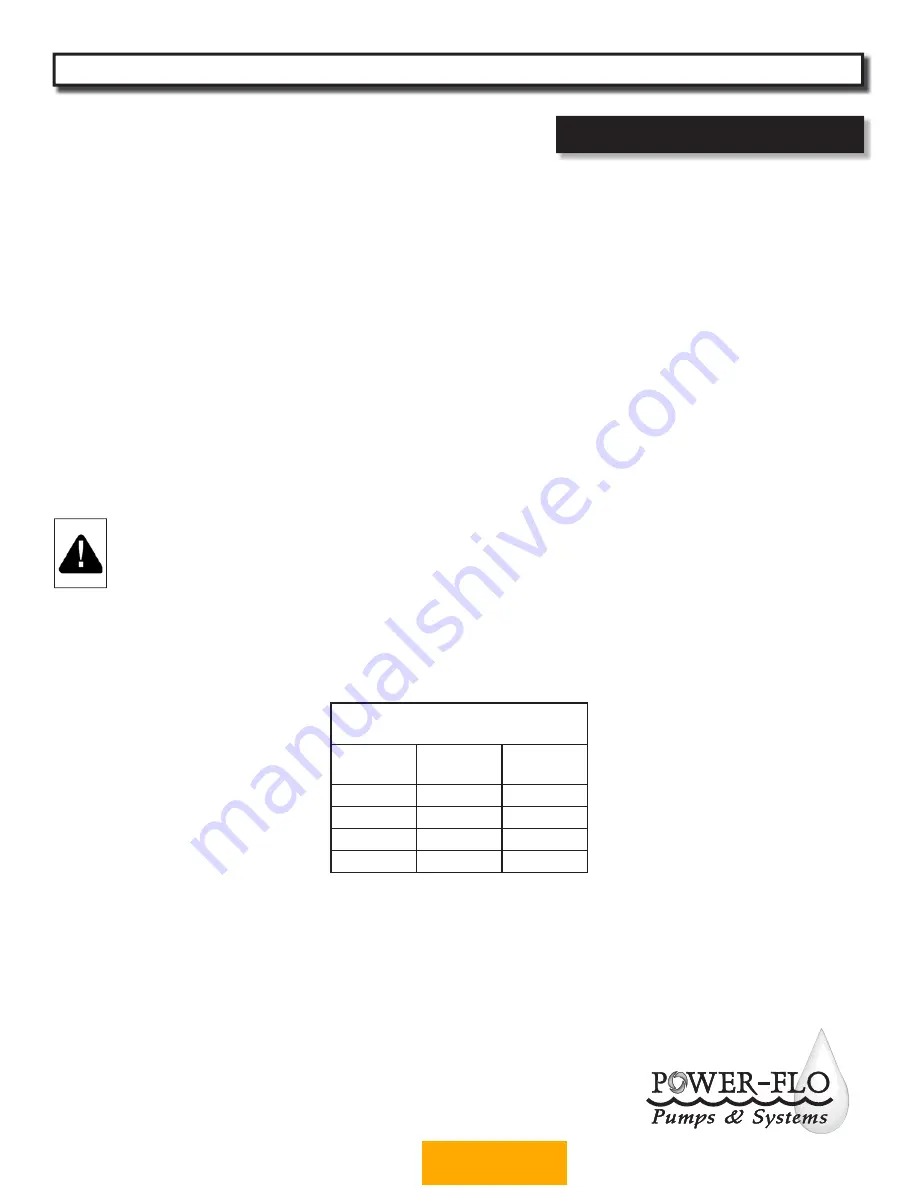
Power-Flo Pumps & Systems • 877-24PUMPS • www.powerfl opumps.com
13
Overload Protection:
Single Phase
- The stator in-winding
overload protector used is referred to
as an inherent overheating protector
and operates on the combined eff ect
of temperature and current. This means
that the overload protector will trip out
and shut the pump off if the windings
become too hot, or the load current
passing through them becomes too high.
IMPORTANT ! -
The overload will then
automatically reset and start the pump
up after the motor cools to a safe
temperature. In the event of an overload,
the source of this condition should be
determined and corrected immediately.
WARNING! - DO NOT LET
THE PUMP CYCLE OR RUN IF
AN OVERLOAD CONDITION
OCCURS !
Three Phase -
The Normally Closed
(N/C) thermal sensor is embedded in the
motor windings and will detect excessive
heat in the event an overload condition
occurs. The thermal sensor will trip when
the windings become too hot and will
automatically reset when the pump
motor cools to a safe temperature. It is
recommended that the thermal sensor
be connected in series to an alarm device
to alert the operator of an overload
condition, and/or the motor starter coil
to stop the pump. In the event of an
overload, the source of this condition
should be determined and repaired.
DO
NOT LET THE PUMP CYCLE OR RUN IF
AN OVERLOAD CONDITION OCCURS!
Moisture Sensors -
A normally open
(N/O) sensor rated of 1 watt @330K
ohms, 500 volt, is installed in the pump
seal chamber which will detect any
moisture present. It is recommended
that this detector be wired in series to
an alarm device or motor starter coil to
alert the operator that a moisture detect
has occurred. In the event of a moisture
detect, check the individual moisture
sensor probe leads for continuity, (∞
resistance = no moisture) and the
junction box/control box for moisture
content. These situations may induce
a false signal in the moisture detecting
circuit. If none of the above test prove
conclusive, the pump(s) should be pulled
and the source of the failure repaired.
IF
A MOISTURE DETECT HAS OCCURRED
MAINTENANCE SHOULD BE
PERFORMED AS SOON AS POSSIBLE!
If current through the temperature sensor
exceeds the values listed, an intermediate
control circuit relay must be used to
reduce the current or the sensor will not
work properly.
TEMPERATURE SENSOR ELECTRICAL
RATINGS
Volts
Continuous
Amperes
Inrush
Amperes
110-120
3.00
30.0
220-240
1.50
15.0
440-480
0.75
7.5
600
0.60
6.0
Wire Size:
If longer power cable is required consult
a qualifi ed electrician for proper wire
size.
Pre-Operation
1.
Check Voltage and Phase -
Compare
the voltage and phase information
stamped on the pump name plate.
2.
Check Pump Rotation
- Improper
motor rotation can result in poor
pump performance and can damage
the motor and/or pump. Check
rotation on three phase units by
momentarily applying power and
observe
the
“kickback”.
“Kickback” should always be in a
counter-clockwise direction as
viewed from motor end or opposite
to impeller rotation. Incorrect rotation
for Single-Phase pumps is unlikely.
If the rotation is incorrect contact
factory.
3.
Name Plate
- Record the information
from the pump name plate to
drawing in front of manual for future
reference.
4.
Insulation Test
- An insulation
(megger) test should be performed
on the motor. Before the pump is put
into service. The resistance values
(ohms) as well as the voltage (volts)
and current (amps) should be
recorded.
5.
Pump-Down Test
- Be sure pump
has been properly wired, lowered into
the basin, sump or lift station, check
the system by filling with liquid and
allowing the pump to operate through
its pumping cycle. The time needed to
empty the system, or pump-down
time along with the volume of water,
should be recorded.
Installation & Service
PF6NC & PF6NC-H
Submersible Non-Clog Pumps
BACK TO INDEX