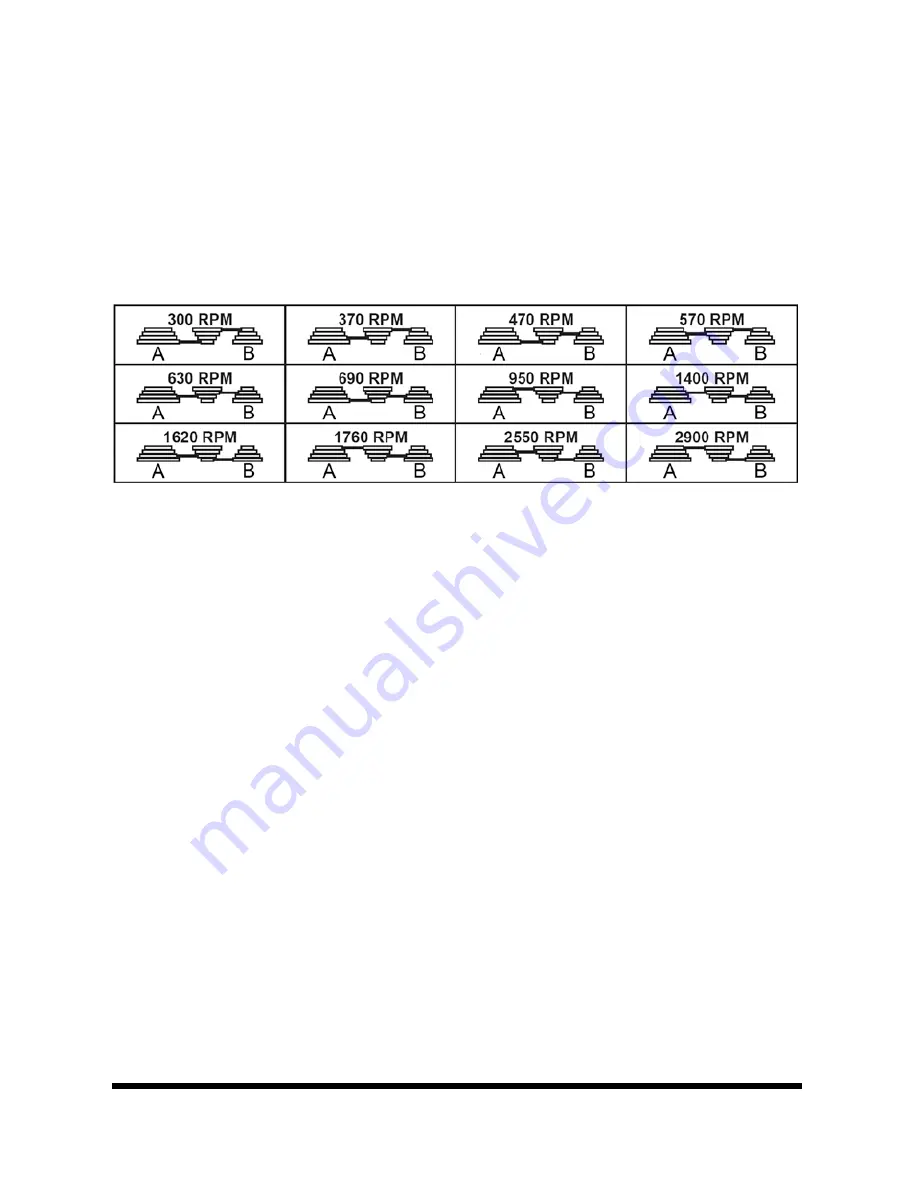
V 4.0
10 in. Bench-Top Drill Press
8654337
4.
When the Belts have been correctly positioned, tighten them by pushing
the Motor away from the Headstock until the belt deflects by approximately
1/2
in.
at its center when using reasonable thumb pressure. Lock this
position in with the two Motor Tension Knobs (#70).
5. You can change the drill speed can by repositioning the belts on the spindle
(A) and the motor (B). Chart 1 shows the belt arrangements for each drill
speed. A full chart is also located on the inside of the pulley cover.
DRILL BIT INSTALLATION
1. Insert the drill bit into the jaws of the chuck approximately 1 in., ensuring
that the jaws do not touch the flutes of the drill bit.
2. Before tightening the chuck, ensure that the drill bit is centered within the jaws.
3. Tighten the chuck securely with the included chuck key.
GENERAL OPERATING INSTRUCTIONS
WARNING! If the drill bit grabs and spins the workpiece, do not attempt to
stop the spinning with your hands, as it can cause an impact injury. Step
back and turn the drill press off. Wait for the spindle to stop turning before
dislodging the workpiece.
1. Check that the drilling depth will not allow the bit to touch the table. This
can damage the drill bit.
2. Place the workpiece on the table. Rotate the feed handles to bring the drill
bit down to the wood. Once the workpiece is in the correct position, clamp
it to the table.
a. If drilling a hole through the entire workpiece, place a scrap piece of
wood beneath the workpiece before positioning and clamping. This will
prevent the underside from splintering as the drill bit breaks through.
Chart 1
Visit www.princessauto.com for more information
13
Summary of Contents for 10 in. Bench-Top Drill Press
Page 20: ...Perceuse à colonne d établi de 10 po ...
Page 21: ...Perceuse à colonne d établi de 10 po ...
Page 22: ......
Page 23: ......
Page 24: ......
Page 25: ......
Page 26: ......
Page 27: ......
Page 28: ......
Page 29: ......
Page 30: ......
Page 31: ......
Page 32: ......
Page 33: ......
Page 34: ......
Page 35: ......
Page 36: ......
Page 37: ......
Page 38: ......
Page 39: ......
Page 40: ......