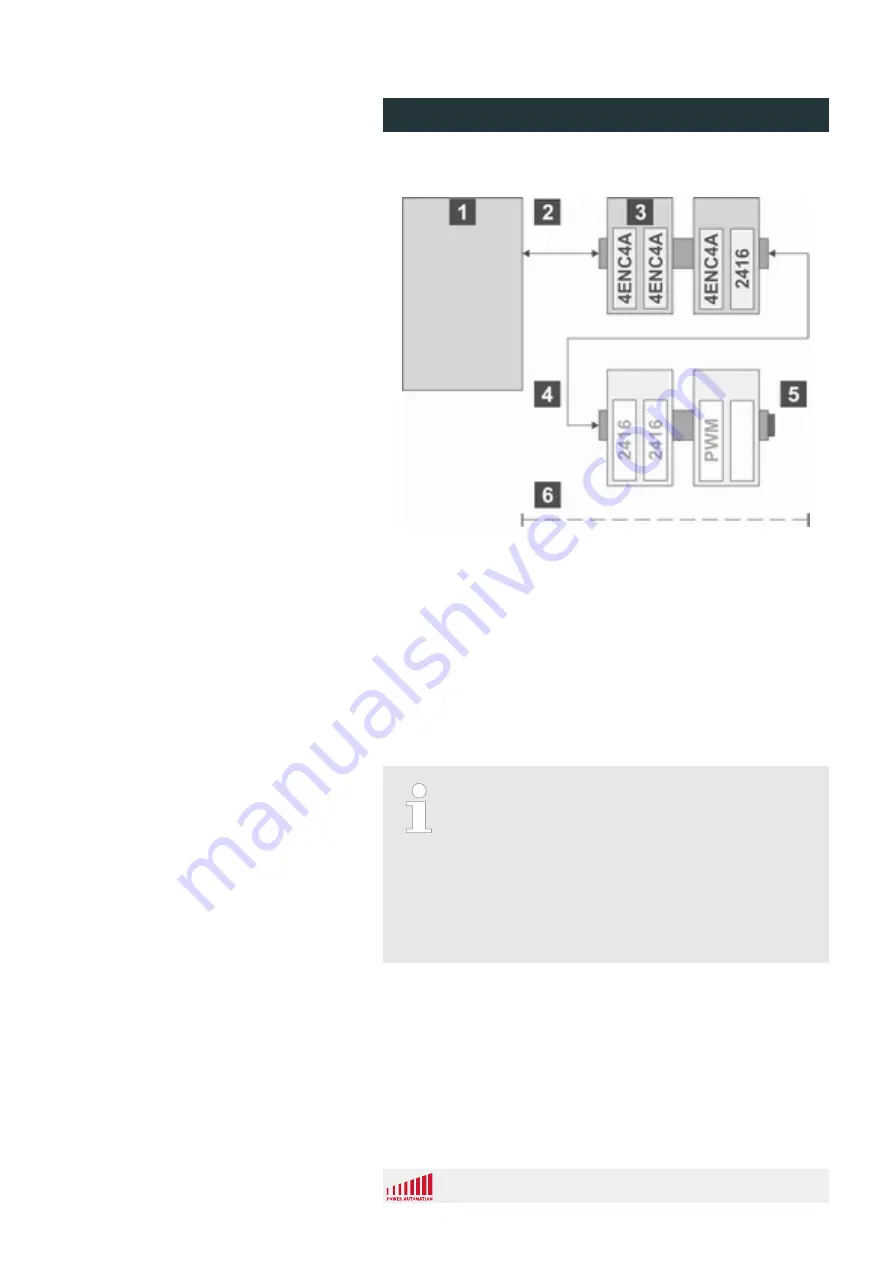
3.8.1 PAMIO boxes and modules
Fig. 37: PAMIO superbus schematic
1
control unit
2
PA superbus connection
3
PAMIO box with two analog axes modules
4
PA superbus connection
5
termination plug
6
max. chain length (14 PAMIO boxes/30 m (98 ft))
A PAMIO box consists of its housing, the PA superbus input and
output connectors as well as two plug-in-slots for I/O modules.
PAMIO boxes can be snapped onto DIN rails and plugged into
each other side by side or connected through optional cables. The
last box carries a termination plug.
Limited cable length
The limits for the I/O system are 31 I/O modules
(internal 2416 EL modules plus a maximum of 14
PAMIO boxes).
The maximum cable length from the control unit to the
last PAMIO box cannot exceed 30 m (98 ft). This has
to be considered as a maximum global length when
several PAMIO boxes are placed at different locations
and connected with interconnection cables.
I/O modules can be mounted where needed, without requiring bus
couplers. Each PAMIO module has its own watchdog timer for the
PA superbus, temperature and voltage monitoring as well as corre-
sponding LED displays on the front side.
Basic Description
PA 8000 EL CNC control unit
Design and function
24.09.2015 | 61
Summary of Contents for PA 8000 EL
Page 1: ...PA 8000 EL CNC control unit Installation instructions...
Page 6: ...PA 8000 EL CNC control unit Table of contents 24 09 2015 6...
Page 26: ...PA 8000 EL CNC control unit Safety 24 09 2015 26...
Page 64: ...PA 8000 EL CNC control unit Design and function 24 09 2015 64...
Page 72: ...PA 8000 EL CNC control unit Technical data 24 09 2015 72...
Page 78: ...Fig 42 Top bottom spacing PA 8000 EL CNC control unit Installation 24 09 2015 78...
Page 84: ...PA 8000 EL CNC control unit Installation 24 09 2015 84...
Page 99: ...Fig 48 RMA Form RMA Form PA 8000 EL CNC control unit Service and return process 24 09 2015 99...
Page 102: ...PA 8000 EL CNC control unit Dismounting and decommissioning 24 09 2015 102...
Page 106: ...PA 8000 EL CNC control unit Proof of change 24 09 2015 106...