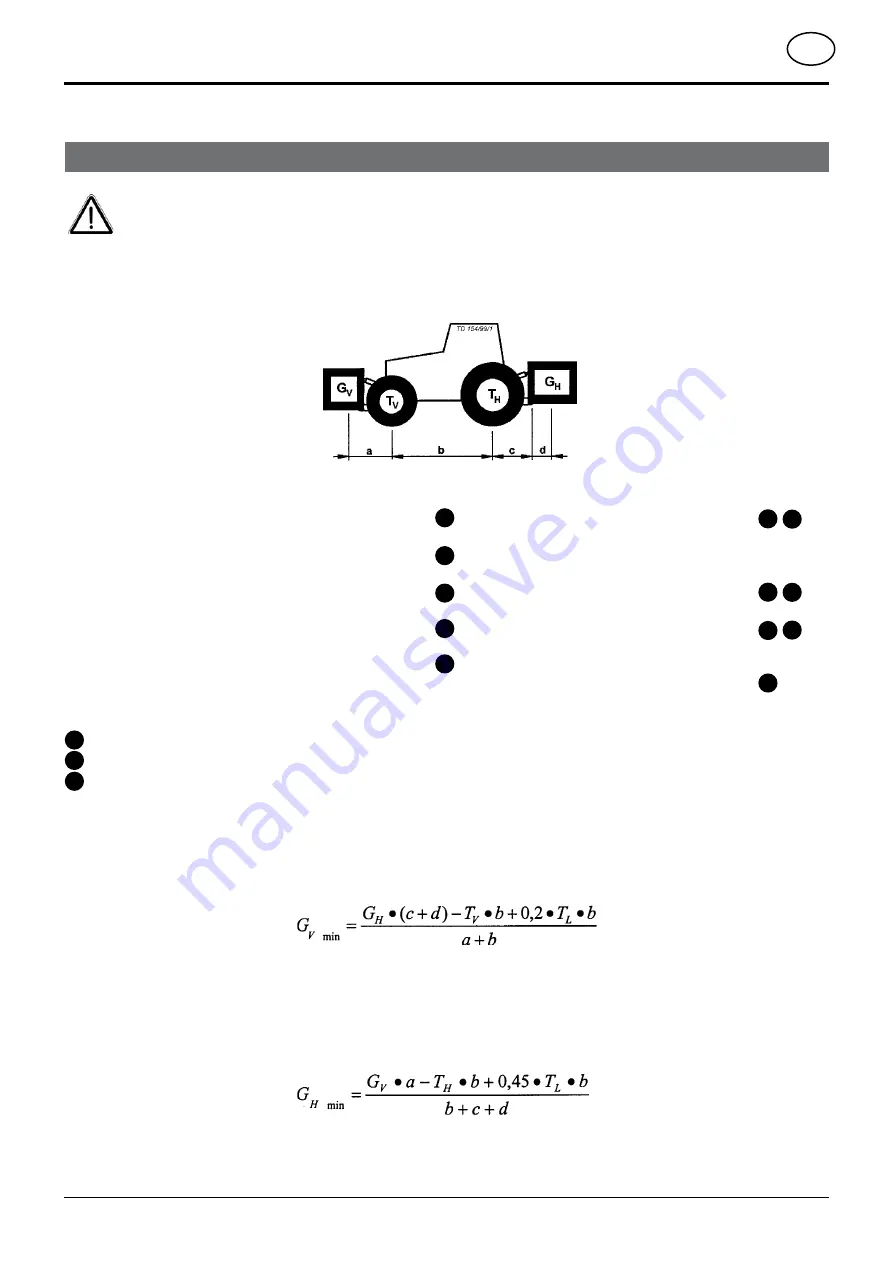
0000-GB zUSINFO / BA-EL ALLG.
GB
- z.42 -
iMPOrTanT! aDDiTiOnaL inFOrMaTiOn
see instruction handbook of the tractor
see price list and/or instruction handbook of the implement
to be measured
Consideration of rear mounted implement and front/rear combinations
1. CALCuLAtIon oF MInIMuM BALLAstInG At tHe Front G
v min
Record the calculated minimum ballasting which is needed at the front of the tractor into the table.
Front mounted implement
2. CALCuLAtIon oF tHe MInIMuM G
H min
Record the calculated minimum ballasting which is needed at the rear of the tractor into the table.
For the calculation you need the following data:
T
L
[kg]
T
V
[kg]
T
H
[kg]
G
H
[kg]
G
V
[kg]
unladen weight of tractor
front axle load of unladen tractor
rear axle load of unladen tractor
combined weight of rear mounted implement/rear
ballast
combined weight of front mounted implement/front
ballast
distance from centre of gravity for
combined front mounted implement/front
ballast to front axle centre
Tractor wheelbase
distance from rear axle centre to centre
of lower link balls
distance from centre of lower link balls
to centre of gravity for combined rear
mounted implement/rear ballast
a
[m]
b
[m]
c
[m]
d
[m]
2
3
1
1
1
1
1
2
2
2
3
3
1
3
2
Combination of tractor and mounted implement
The mounting of implements on the front or rear three point linkage shall not result in exceeding the maximum permissible weight,
the permissible axle loads and the tyre load carrying capacities ot the tractor. The front axle of the tractor must always to be loaded
with at least 20 % of the unladen weight of the tractor.
Make sure before buying an implement that these conditions are fulfilled by carrying out the following calculations or by weighing the
tractor/implement combination.
Determination of the total weight, the axle loads, the tyre load carrying capacity and the necessary
minimum ballasting