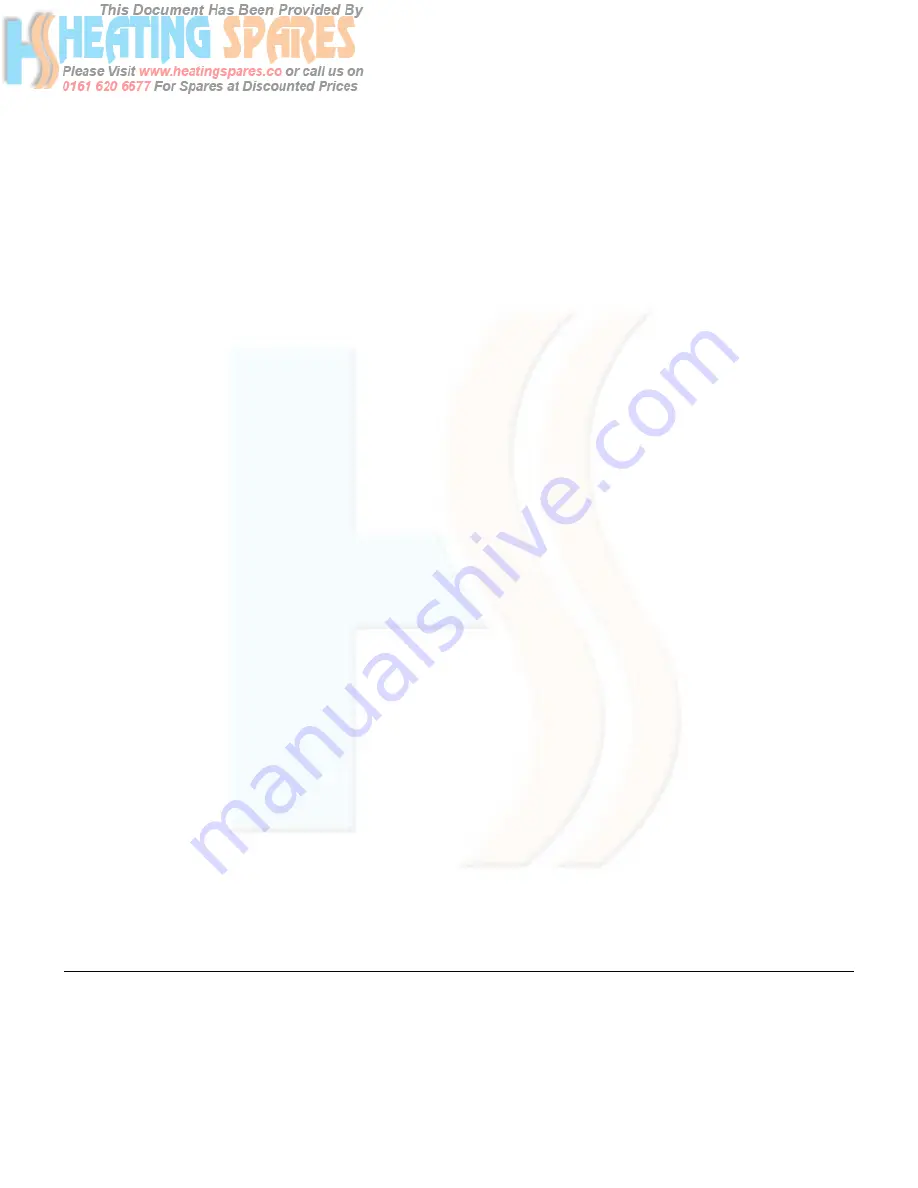
Supplied By www.heating spares.co Tel. 0161 620 6677
6 GENERAL
Manual No. 405/0101
GENERAL - PAGE 6
In the event of an electrical fault after installation of the appliance, preliminary electrical systems checks must be carried out
i.e. Earth Continuity, Short Circuit, Polarity and Resistance to Earth.
2.6
AIR SUPPLY
The room in which the boiler is installed does not require a purpose provided air vent.
If the boiler is installed in a cupboard or compartment, permanent air vents are required in the cupboard or compartment,
one at high level and one at low level, either direct to the outside air or to a room. Both high level and low level air vents
must communicate with the same room or must be on the same wall to outside air. Both the high level and low level vent
must each have a free area as stated below. The free area of each vent may be halved if the ventilation is provided directly
from outside.
Ultra Dv 30: 110 cm²
Ultra Dv 40: 140 cm²
Ultra Dv 50: 180 cm²
Ultra Dv 60: 210 cm²
Ultra Dv 80: 264 cm²
If the boiler is installed in a cupboard or compartment with a door, allow at least 50 mm clearance between the front of the
boiler and the door for air movement.
2.7
FLUE SYSTEM
The flue/terminal assembly supplied with the boiler is 500 mm long.
A 1 m flue extension is available, if required.
Under no circumstances should the total flue length exceed 3 m. A 3 m length flue would comprise of three 1m kits, one of
which would be cut down to 500mm.
The following method should be used to determine the flue length.
Rear flue
A = C + 28 mm
Side flue
A = B + C
where: A = Required flue length.
B = Inside wall to the side of the white case plus (+) 30 mm.
C = Finished wall thickness.
2.8
LOCATION OF BOILER
The boiler is not suitable for external installation.
The boiler must be mounted on a flat wall which is sufficiently robust to take the weight of the boiler.
The boiler is suitable for installation to a combustible wall e.g. wood cladding, provided that the flue duct is not closer than 25
mm to combustible material. A metal sleeve should be installed to surround the flue duct to provide a 25 mm annular space.
Further guidance is given in BS5440:1:1990, sub-clauses 3.3 and 4.2.5.
If the boiler is to be installed in a timber framed building it should be fitted in accordance with the British Gas publication -
“Guide for Gas Installation in Timber Framed Housing” reference DM2. If in doubt advice must be sought from the local
region of British Gas or from Potterton Myson.
The boiler may be installed in any room, although particular attention is drawn to the requirements of the current IEE Wiring
Regulations and, in Scotland, the electrical provisions of the Building Standards applicable in Scotland with respect to the
installation of the boiler in a room containing a bath or shower.
Where a room-sealed appliance is installed in a room containing a bath or shower, any electrical switch or appliance control,
utilising mains electricity should be so situated that it cannot be touched by a person using the bath or shower.
Where the installation of the boiler will be in an unusual position, special procedures may be necessary and BS6798 and
BS5546 give detailed guidance on this aspect.
A cupboard or compartment used to enclose the boiler must be designed and constructed specifically for this purpose. An
existing cupboard or compartment may be used provided that it is modified for the purpose. Details of essential features of
cupboard/compartment design including airing cupboard installations are given in BS6798 and BS5546 and should be
complied with.
The boiler requires only the clearances stated in the Technical Data, page 4, after installation. If it is felt that extra space is
required for installation any adjacent kitchen units or fitments may have to be removed.
The boiler must be installed so that the flue terminal is exposed to the external air. It is important that the position of the
terminal allows the free passage of air across it at all times.
The minimum acceptable spacings from the terminal to obstructions, corners and ventilation openings are shown on the
following page.