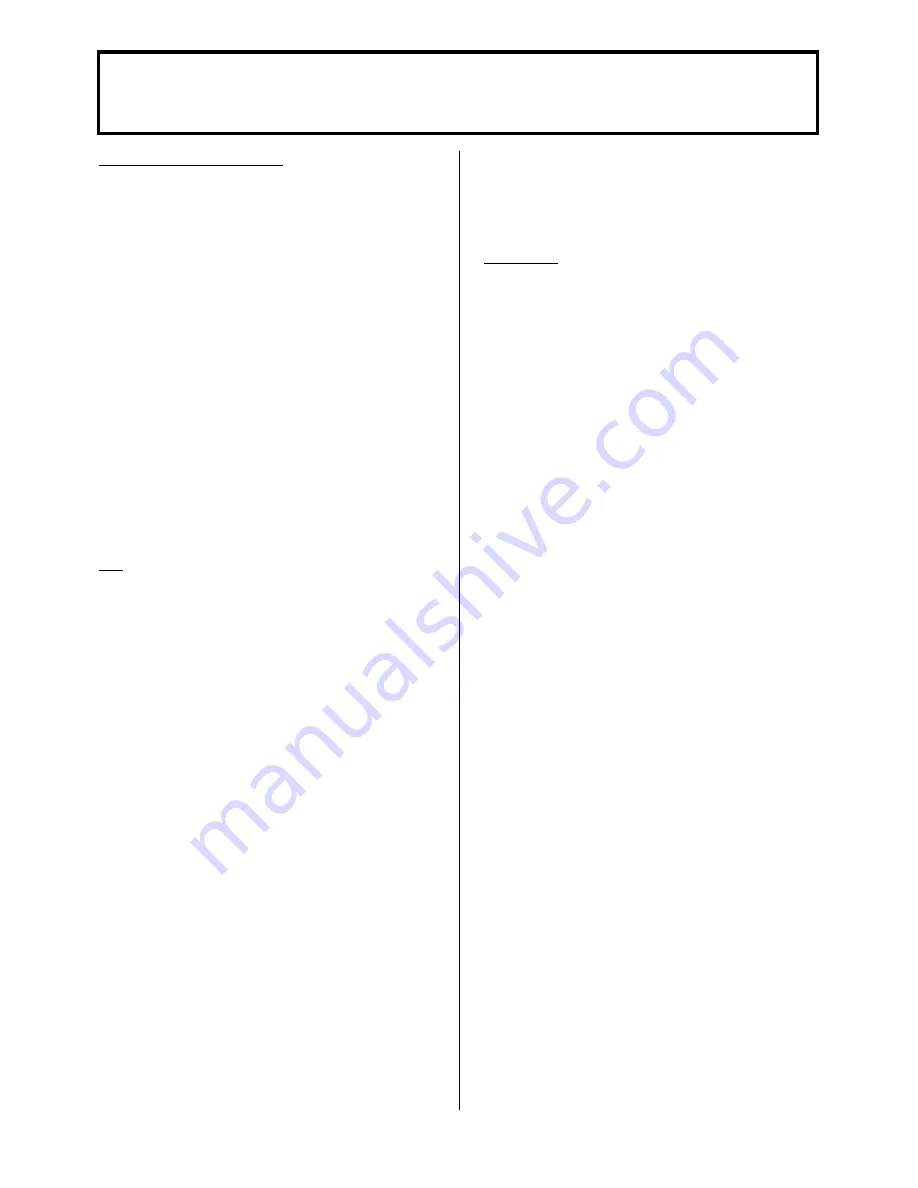
SECTION 2
POTTERTON COMMERCIAL PRODUCTS DIVISION
INSTALLATION, OPERATION AND MAINTENANCE MANUAL
PAGE 4
PARAMOUNT
General Safety Precautions
Installation of System:
Important:
The boiler must
be commissioned following completion of installation.
Operations of an un-commissioned appliance may
cause injury to personnel and damage to the boiler
unit would invalidate the warranty.
Commissioning must only be carried out by
personnel approved and competent to do so. This
facility is available from Potterton Commercial
Service Offices.
Importan
t: The boiler unit is supplied in accordance
with Potterton Commercial quality assurance plan
registered to meet the requirements of BSN ISO
9002. A condition of the supply of the appliance for
compliance with this is the return of the appliance
commissioning report.
Electrical Installation:
The electrical installation
work must be carried out by a qualified electrician.
Gas Installation:
Boiler installation as well as
commissioning, servicing and maintenance must be
carried out by an approved gas installer. For use
with natural gas (G20) nominal supply pressure
20 mbar (LPG option available).
Use
The POTTERTON PARAMOUNT wall hung
condensing boiler is available in three sizes with
outputs from 40 kW to 80 kW.
They are CE marked for use on Natural Gas (LPG)
on open vented systems (min 1 bar) and are suitable
for use on sealed systems with a maximum operating
pressure of 3 bar (40 kW), 4 bar (60 and 80 kW).
Refer to relevant British Standards and Codes of
Practice for installation of condensing boilers on
sealed systems. The heat exchanger consists of
aluminium – silicon alloy, which allows very compact
and lightweight boiler construction. The fully pre-
mixed burner works in a modulating range between
25% and 100%. Therefore the boiler is adapted to
the particular heat requirements of the circuit. The
gas/air ratio control ensures uniform CO
2
emissions
and low NOx. This is obtained by comparing the
target boiler temperature and actual boiler
temperature. If there is a difference between these
two values then the internal microprocessor
calculates a new fan speed. The change in fan
speed in turn changes the combustion chamber static
pressure which is monitored by the gas/air ratio
controller and the gas rate is adjusted thus
maintaining the correct gas to air in the boiler. This
ensures that a uniform gas/air ratio is maintained
over the total range of the boiler modulation and that
constant CO
2
values are achieved.
For optimum utilisation condensing boilers should be
operated at a low return temperature. However the
PARAMOUNT will also work at design temperatures
of 70/50
°
C in the condensing mode as the return
water temperature is below dew point (dew point is
53
°
C at 8.5% CO
2
).
They fulfil EN 483 and EN 677, Type C.
Installation types B
23
, B
33
, C
13x
, C
33x
, C
43x
, C
63x
.
Emission value group G 61. Category II
2H3P.
Installation
Before starting work a risk assessment should be
carried out in the boiler house and its access to
ensure a safe installation and working environment.
Any person installing or working on the boiler
must
be qualified and attention is drawn to the mandatory
requirements of C.O.R.G.I. registration for all gas
installers.
Manual Handling:- Any person or persons moving or
lifting the boiler or any part thereof should be trained
in manual handling techniques and if necessary use
suitable lifting equipment to reduce the risk of injury
to themselves or other people.
The installation should comply with relevant British
Standard Specifications, Codes of Practice and
current Building Regulations, together with any
special regional requirements of the Local
Authorities, Gas Undertaking and Insurance
Company. All electrical wiring must comply with
I.E.E. Regulations for the Electrical Equipment of
Buildings. The installation of the boiler must be in
accordance with the relevant requirements of:
Health and Safety at Work Act 1974
Building Regulations 2000
Electricity at Work Regulations 1989
Management of H&S at Work Regulations 1998
Manual Handling Regulations 1992
Model Water By-Laws 1986
BS 7671: 1992 – Requirements for Electrical
Installations, IEE Wiring
Regulations Sixteenth Edition
BS 5440: 2000: Part 1 - Specifications for Installation
of Flues
BS 5440: 2000: Part 2 – Specifications for Installation
of Ventilation for Gas Appliances.
BS 6644: 1991 – Installation of Gas Fired Hot Water
Boilers for inputs between 60 kW and 2MW.
BS 7074: 1989: Part 2 – Application Selection and
Installation of Expansion Vessels and Ancillary
Equipment for Sealed Water Systems.
BS 6880: 1988 – codes of Practice for Low
Temperature Hot Water Systems.
EN 677: 1997 – Gas Fired Central Heating Boilers for
Condensing Boilers with a nominal heat input not
exceeding 70 kW.
CP 342:2 – Centralised Hot Water Supply
Gas Safety (Installation and Use) Regulations 1998.
IM/II – Flues for Commercial and Industrial Gas Fired
Boilers and Air Heaters
IGE/UP/1
– Soundness Testing and Purging
Procedure for Non Domestic Installations.