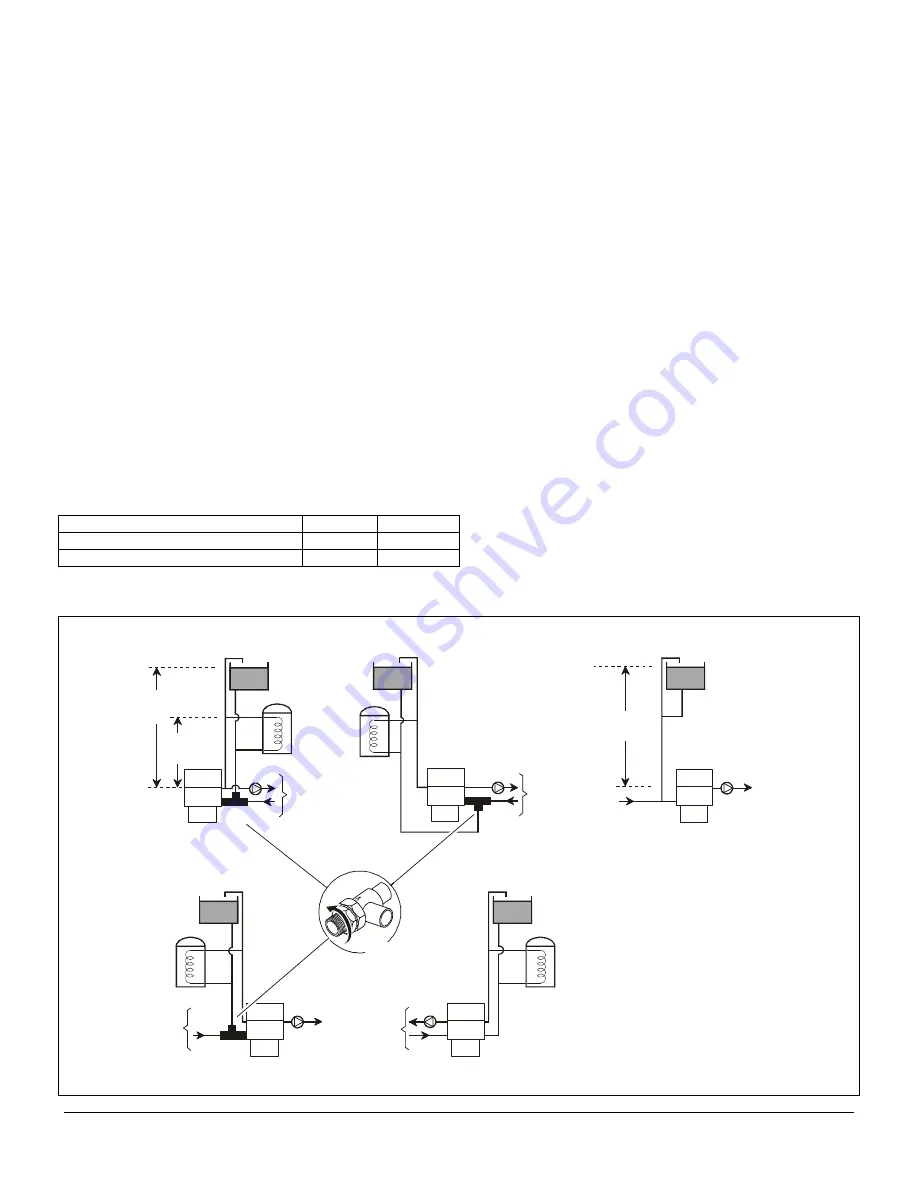
3. Installation Requirements – Page 7
To size the expansion vessel it is first necessary to calculate
the volume of water in the system in litres. The following
volumes may be used as a conservative guide to calculating
the system volume.
Boiler Heat Exchanger:
4 litres
Small Bore Pipework:
1 litre per kW of system
output
Micro Bore Pipework:
7 litres
Steel Panel Radiators:
8 litres per kW of system
output
Low Water Capacity Radiators:
2 litres per kW of system
output
Hot Water Cylinder:
2 litres
If the system is extended, the expansion vessel volume may
have to be increased unless provision has been made for
extension. Where a vessel of the calculated size is not
available, the next available larger size should be used.
The boiler flow temperature is controlled at approximately
82°C.
The vessel size can now be determined from the information
in Table 1 where V = System volume in litres.
Cylinder
The hot water cylinder must be an indirect coil type or a
direct cylinder fitted with an immersion calorifier suitable for
operating at a gauge pressure of 0.3 bar (5 lbf/in
2
) in excess
of safety valve setting. Single feed indirect cylinders are not
suitable for sealed systems.
Method of Make-up
Provision shall be made for replacing water loss from the
system either:
i)
from a make-up vessel or tank mounted in a position
higher than the top point of the system, and connected
through a non-return valve to the system on the return
side of the hot water cylinder or the return side of all
heat emitters. or
ii)
where access to a make-up vessel would be difficult by
using the mains top up method or a remote automatic
pressurisation and make-up unit as shown in
Figs. 7 & 8.
Mains Connection
There shall be no connection to the mains water supply or to
the water storage tank which supplies domestic hot water
even though a non-return valve, without the approval of the
Local Water Authority.
Vessel Charge Pressure (bar)
0.5
1.5
Filling Point
Initial System Pressure (bar)
1.0
1.0
The system shall be fitted with a filling point at low level
Expansion Vessel Volume (litres)
V x 0.11
V x 0.087
which incorporates a stop valve to BS 1010 and a double
Table 1.
check valve (approved by the National Water Council) to be
fitted in this order from the system mains, see Fig. 7.
Flow
Flow
Return
Return
Central
Heating
Central
Heating
In
je
c
to
r
T
e
e
In
je
c
to
r
T
e
e
1.2
Metres
Min.
30.5
Metres
Max.
Water Level
Heat
Exchanger
Heat
Exchanger
Flow
Return
Central
Heating
Flow
Return
Central
Heating
Heat
Exchanger
30.5M Max.
0.9M Min.
Water Level
Flow
Fully
Pumped
System
Return
Heat
Exchanger
Heat
Exchanger
BBU Open Vented
System Variants
All Systems Illustrated
Can Be Fitted To The
Other Side Of the Boiler
On Combined Gravity
D.H.W. Pumped Heating
Systems The Injector
Tee Is To Be Fitted
Directly To The Boiler.
The Tee On The
Combined Flows Is
To Be Fitted As Close
To The Boiler As Possible
B
B
4
5
0
0
4
C
Injector Tee
can be installed
in any direction
see Fig 14
Fig 3
Summary of Contents for Housewarmer 45
Page 17: ...4 Installation Page 17 ...
Page 25: ...8 Electrical Diagrams Page 25 ...
Page 34: ...Installation Page 7 ...
Page 35: ...Installation Page 8 ...