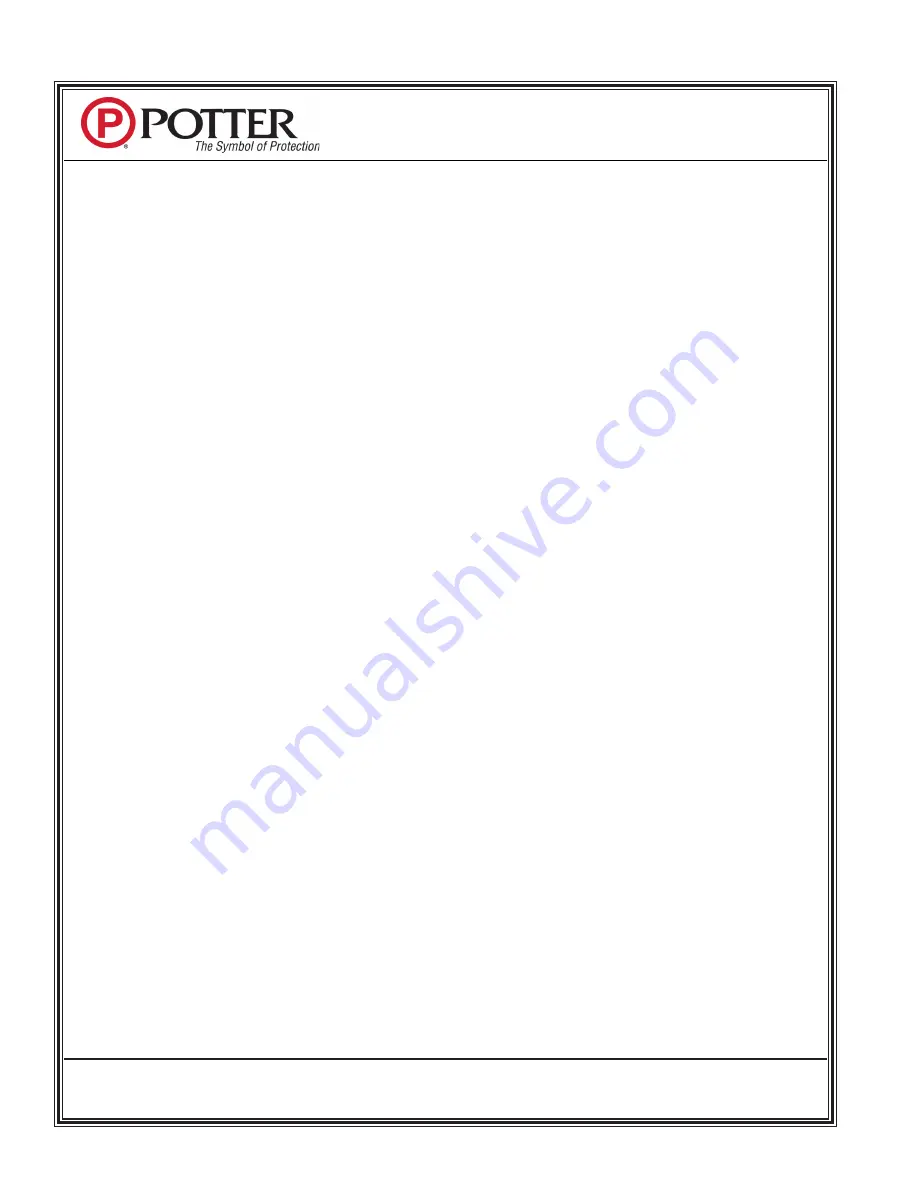
2
INS-2500 • 5403680 • REV C • 04/19
Potter Electric Signal Company, LLC
St. Louis, MO • (866) 956-0988
WARRANTY INFORMATION
GENERAL PROVISIONS & LIMITATIONS
Potter Electric Signal Company, LLC (the “Company”) warrants to each original purchaser (“Purchaser”) of its new products from the
Company or its Authorized Distributor that such products are, at the time of delivery to the Purchaser, made with good materials and
workmanship. No warranty is made with respect to:
1. Any product, which has been repaired or altered in such a way, in the Companies judgment, as to affect the product adversely.
2. Any product, which has, in the Companies judgment been subjected to negligence, accident, improper storage, improper installation
or application.
3. Any product, which has not been operated or maintained in accordance with the recommendations of the Company.
4. Components or accessories manufactured, warranted and serviced by others.
5. Any reconditioned or prior owned product.
Claims for items described in 4 above should be submitted directly to the manufacturer.
WARRANTY PERIOD
The Company’s obligation under this Warranty is limited to repair or, at its option, replacing during normal business hours at the designated
facility of the Company, any part that in its judgment proved not to be as warranted within the applicable Warranty Period as follows.
COMPONENTS
All non-consumable components are warranted for 12 months from the date of purchase. Consumable are not covered under warranty. The
unit must have been installed by either a factory authorized distributor or agent in accordance with the factory recommendations taking into
account all other local site conditions not originally noted to the factory. The unit must be operated and maintained in accordance with the
Factory recommendations and original design conditions. Failure to provide such proof of the above may void warranty.
LABOR TRANSPORTATION & INSPECTION
The Company will repair or replace any product or part thereof which in the Companies judgment is proved to be not as warranted. Labor
costs are not covered under warranty.
All costs of transportation of product, labor or parts claimed not to be as warranted and, of repaired or replaced parts to or from factory
shall be borne by purchaser. The Company may require the return of any part claimed not to be as warranted to one of its facilities as
designated by the Company, transportation prepaid by Purchaser, to establish a claim under this warranty.
Replacement parts provided under the terms of the warranty are warranted for the remainder of the Warranty Period of the product upon
which installed to the same extent as if such parts were original components.
DISCLAIMER
THE FOREGOING WARRANTY IS EXCLUSIVE AND IT IS EXPRESSLY AGREED THAT, EXCEPT AS TO TITLE, THE
COMPANY MAKES NO OTHER WARRANTIES, EXPRESSED OR IMPLIED OR STATUTORY, INCLUDING ANY IMPLIED
WARRANTY OR MERCHANTABILITY.
THE REMEDY PROVIDED UNDER THIS WARRANTY SHALL BE THE SOLE, EXCLUSIVE AND ONLY REMEDY AVAILABLE
TO THE PURCHASER AND IN NO CASE SHALL THE COMPANY BE SUBJECT TO ANY OTHER OBLIGATIONS OR
LIABILITIES. UNDER NO CIRCUMSTANCES SHALL THE COMPANY BE LIABLE FOR SPECIAL, INDIRECT, INCIDENTAL OR
CONSEQUENTIAL DAMAGES, EXPENSES, LOSSES OR DELAYS HOWSOEVER CAUSED.
No statement, representation, agreement, or understanding, oral or written, made by any agent, distributor, representative or employee of
the Company which is not contained in this Warranty will be binding upon the company unless made in writing and executed by an officer
of the Company.
This warranty shall not be effective as to any claim which is not presented within 30 days after the date upon which the product is claimed
not to have been as warranted. Any action for breach of this warranty must be commenced within one year after the date upon which the
cause of action occurred.
Any adjustment made pursuant to this warranty shall not be construed as an admission by the Company that any product was not as
warranted.
PROMPT DISPOSITION
The Company will make a good faith effort for prompt correction or other adjustment with respect to any product, which proves to
be defective within the warranty period. Before returning any product, write or call the distributor, agent or authorized company from
which the product was purchased, describing defect and giving date and number of original invoice, as well as proof of Factory supplied
consumable and proof of scheduled maintenance. Title and risk of loss pass to buyer upon delivery to the common carrier.
PRODUCT SUITABILITY
Many States, Localities and Countries have codes and regulations governing sales, construction, installation, and/or use of products for
certain purposes, which may vary from those in neighboring areas. While Potter attempts to assure that its products comply with such
codes, it cannot guarantee compliance, and cannot be responsible for how the product is installed or used. Before purchase and use of a
product, please review the product application, and national and local codes and regulations, and be sure that the product, installation, and
use will comply with them.