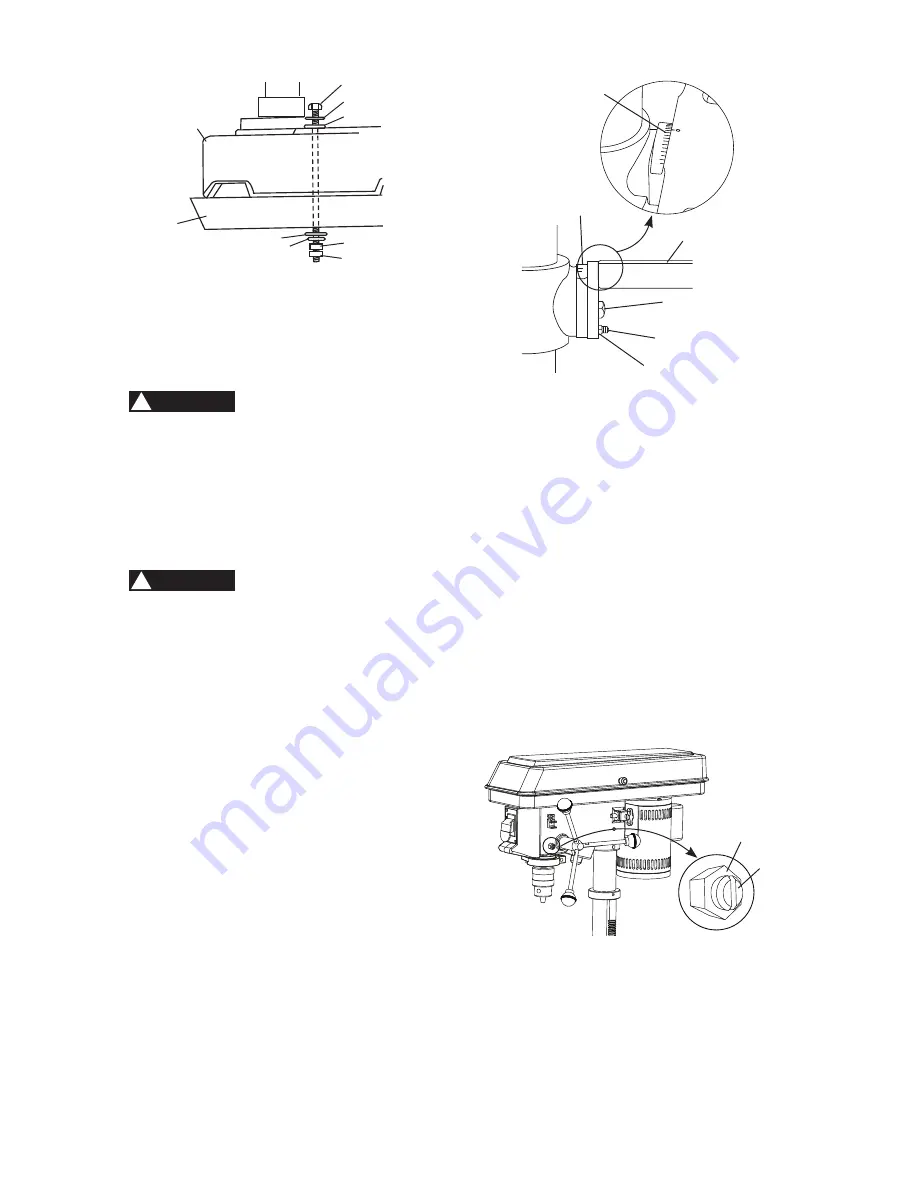
17
Fig. M
SPINDLE / QUILL (FIG. N)
Rotate the feed handles counterclockwise
to lower spindle to its lowest position. Hold
the chuck and move it front to back. If there
is excessive play, proceed with the following
adjustments:
1. Loosen the lock nut (1) located on the
right side of the drill press by using a
10 mm wrench.
2. Turn the screw (2) clockwise to eliminate
the play, using a slotted screwdriver, but
without obstructing the upward movement
of the spindle. (A little play in the spindle
is normal.)
3. Tighten the lock nut (1).
Fig. N
Fig. L
ADJUSTMENTS INSTRUCTIONS
NOTE:
All the adjustments for the operation
of the drill press have been completed at the
factory. Due to normal wear and use, some
occasional readjustments may be necessary.
To avoid injury from an accidental start,
ALWAYS make sure the switch is in the
“OFF” position, the switch key is removed,
and the plug is not connected to the power
source outlet before making adjustments.
BEVEL DRILLING (FIG. M)
To prevent personal injury, always
disconnect the plug from the power
source when making any adjustments.
NOTE:
A bevel scale has been included
to measure approximate bevel angles. If
precision is necessary, a square or other
measuring tool should be used to position
the table. To use the bevel scale (1):
1. TIGHTEN the nut (2) on the locking pin (3)
using a 10 mm or adjustable wrench
clockwise to RELEASE the locking pin (3)
from the table support.
2. Loosen the bevel lock bolt (4) using a
17 mm or adjustable wrench.
3. Tilt the table (5) to desired bevel angle
that will shown on the bevel scale (1).
4. Tighten the bevel lock bolt (4).
5. To return the table to horizontal position,
loosen the bevel lock bolt (4), return the
table (5) to the 0° position.
6. Return the nut (2) on locking pin (3) to the
OUTSIDE END OF THREADS. Gently
tap locking pin (3) until it is seated in the
mating hole of the table bracket. Hand
tighten the nut (2).
WARNING
!
1
2
5
3
4
6
7
8
9
WARNING
!
5
2
4
1
1
3
1
2