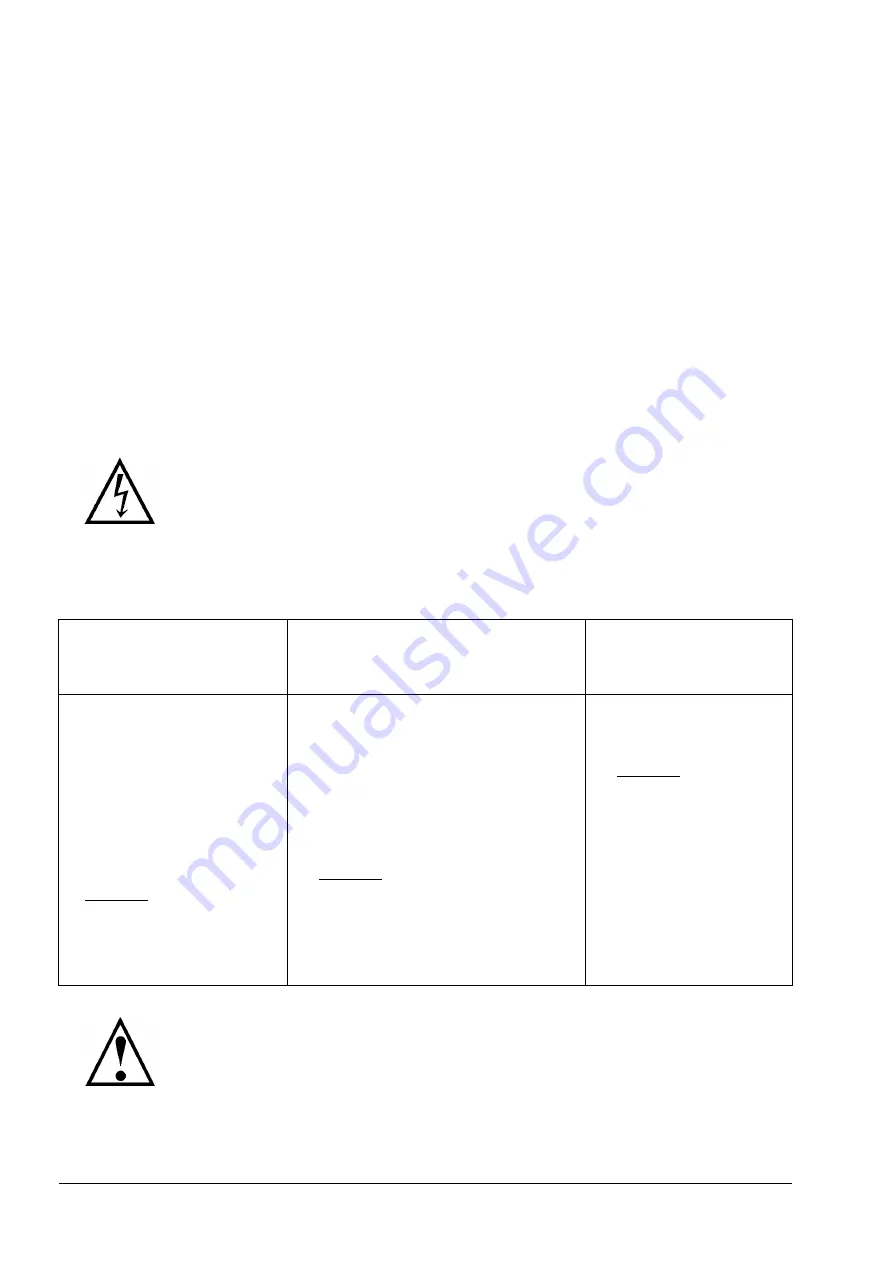
PONNDORF Gerätetechnik GmbH
Leipziger Strasse 374
D - 34123 Kassel
Operation manual
Hose Pump type
P_high pressure 65
Page 23 of 26
Version 002_GB / 05.2017
7. Maintenance / Service
There are no sophisticated procedures of maintenance necessary for Ponndorf Hose
Pumps.
Nevertheless there have to be made regular inspections in order to avoid any decrease of
capabilities of the pump (e.g. suction capacity / discharge head / flow rate).
7.1 Changing the pump hose
When changing the pump hose please consider chapter 6.4 (Installing / changing of the
pump hose).
Remove power from the pump by removing the main fuses before doing
any cleaning / maintenance / assembly operations !
7.2 Maintenance
Filling of lubricant bath
Rotor bearings
Inspection glass
• check on sufficient liquid
level (max. 25 liter
approx.)
• see also page 23
(chapter
6.5, picture 13)
• interval:
every 300 hours of
operation
• check on proper seat
of bearings
• check on inadmissible
development of heat
• check on inadmissible
noise development of bearings
• interval:
every time when
changing the pump
hose respectively every 500
hours of operation
• check on intactness
• interval:
every 500 hours of
operation
In case of wear characteristics mentioned above rotor bearings must be
replaced!