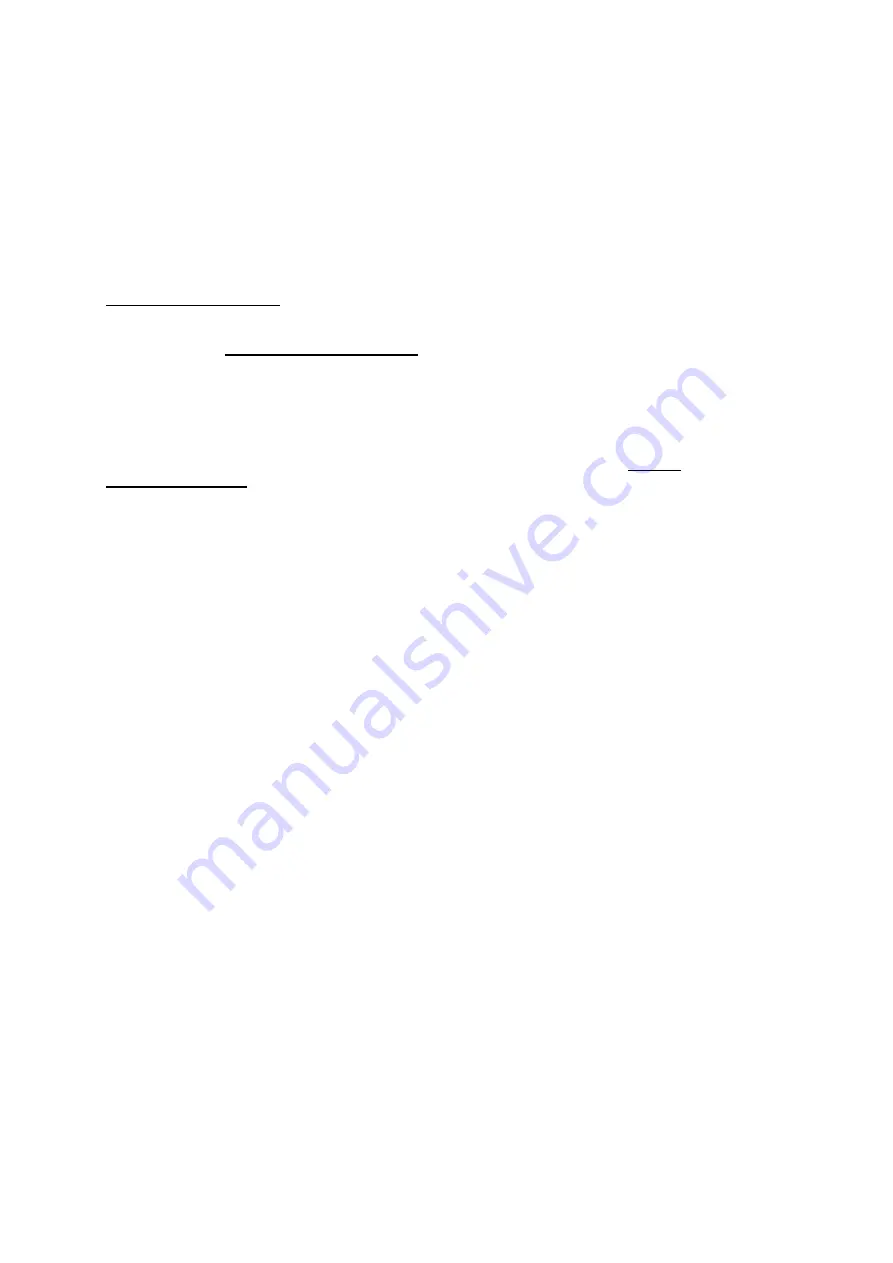
Workbook 4
Controller SIGMATEK - Boiler control
36
4 GUARANTEE AND LIABILITY FOR DEFECTS
The manufacturer provides guarantee:
- for the boiler on a period of 24 months from the date of putting into operation, however, no longer than
30 months from the date of shipment from the manufacturing plant
- for the boiler body on a period of 60 months from the date of putting into operation
- ceramic parts are not covered by the warranty. Its durability is dependent on the way of operation of boiler and their
guaranteed durability is 12 months.
GUARANTEE CONDITIONS
1) User is obliged to ensure installation of the boiler and putting it into operation only by an
authorized servicing organization which has the manufacturer's accreditation and the user is also
obliged to send the
letter of guarantee number 1
to the manufacturer's address immediately
after the product has been put into operation.
2) The boiler has to be operated only within these Instructions for operation and only prescribed fuel
may be used (wood pellets -
φ
6-8.5 mm), free from any admixtures and foreign object. Alternative fuel must be approved
by the boiler manufacturer.
3) If the user wants to claim any form of guarantee, he/she has to submit duly filled in
letter of
guarantee number 2
.
4) The user is obliged to demonstrate that the product was maintained in regular intervals which are
described in the chapter "MAINTENANCE". Regular annual maintenance has to be done by trained person who is also
responsible for the record of it within 14 days (list is part of manual) / service intervention or repaired has to be correctly
recorded and sanded to a manufacturer.
5) Every notification of defect has to be done in writing to the address of the manufacturer
immediately after having been ascertained.
The manufacturer reserves the right of product innovations, which may not be part of this manual.
Important:
Recommended hydraulic connections are principled diagrams created by manufacturer on the basis of
practical experience in the operation of boilers KP.
The user can use the application unchanged as well as in particular modification to the best solution of
heating system.
This is primary responsibility of the designer and implementer of the heating system -
which is why the
Ponast company cannot take over the guarantee for the functionality of a particular solution of heating
system.
5 DISPOSAL OF PRODUCT AFTER TEH END OF ITS SERVICE LIFE
Disposing of the Product is done in accordance with the generally applicable regulations.
The following main kinds of waste will be generated after the end of the product´s service life:
Control unit with sensing and control elements
– waste code 200136, category O.
Summary of Contents for Sigmatek
Page 1: ......
Page 16: ...Workbook 4 Controller SIGMATEK Boiler control 15 3 3 1 2 Menu users settings ...
Page 21: ...Workbook 4 Controller SIGMATEK Boiler control 20 Actual values Configuration ...
Page 28: ...Workbook 4 Controller SIGMATEK Boiler control 27 Load from USB Save on USB ...
Page 33: ...Workbook 4 Controller SIGMATEK Boiler control 32 ...
Page 35: ...Workbook 4 Controller SIGMATEK Boiler control 34 ...
Page 36: ...Workbook 4 Controller SIGMATEK Boiler control 35 i ...
Page 38: ...37 Picture No 7 Circuit diagram control unit ...
Page 39: ...38 Picture No 8 Circuit diagram module HZS 533 ...
Page 40: ...39 Picture No 9 Circuit diagram HZS 533 HZS 53 ...