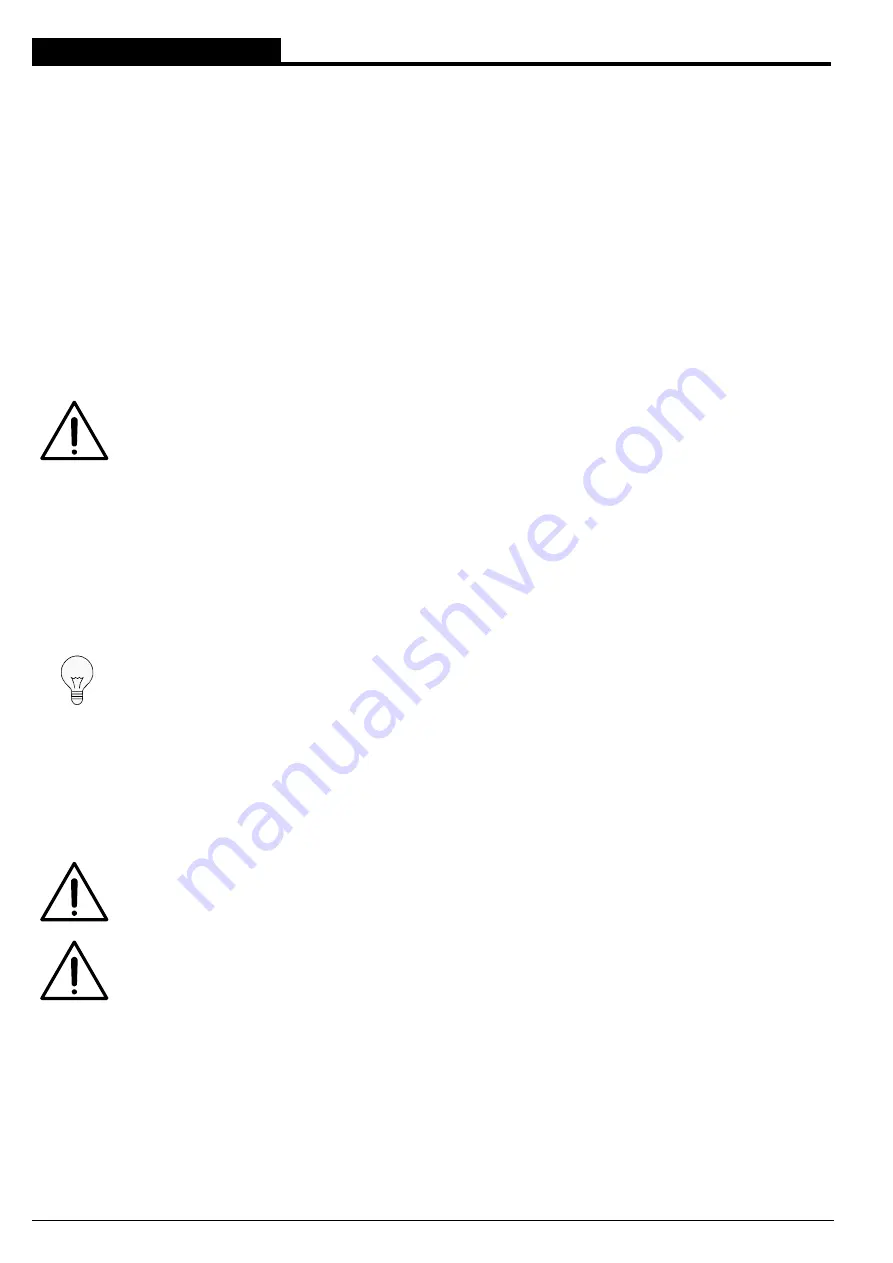
Integrative notes to the operating manual for magnetic coupling centrifugal pumps conforming to the ATEX 94/9/CE directive TCK... - TBK... – TBAK…
16
7 – OPERATIONAL RISKS
As required by the ATEX 94/9/EC certification for the use in zones classified such as Zone 1 and Zone 2, the pump is
not provided with redundant safety systems combined one with the other, with the exception of the system with double
mechanical seals.
The use of the pump therefore presents residual operational risks for which special rules of application, installation and
monitoring are required. The description of these risks is shown in the following paragraphs, together with the
prescriptions of how to avoid these risks.
7.1 – INTAKE OF FOREIGN BODIES
The intake of foreign bodies into the pump must be avoided by cleaning carefully the
suction piping
before starting the
plant and by using suitable filters, in
the event
that
foreign bodies
are present in
the liquid pumped (the TCT series is
built for accepting the passage of foreign bodies of a certain size
)
. However, exact
relevant
in
formation
must be given
for de
termining
the type and the characteristics of the pump to POMPETRAVAINI). Cleaning of the filters must be
carried out regularly by authorized and skilled persons
at
the time intervals established by the user according to his
own experience.
The
requirements
are shown in Chapter 9 under paragraph 9.2.1 of the Operator’s Manual.
RESIDUAL RISK: The intake of foreign bodies into the pump may cause friction and overheating
between the impeller and the pump body and even seizing of the pump components. Also the
electric motor will be subject to higher power input and overheating. This influences also all
components of the electric power cable which may become overheated, create sparking and
burning, if not correctly dimensioned or installed for absorbing this higher power input.
7.2 – DRY RUNNING
The pump must NEVER be run in a dry state. In order to prevent the running of the pump without liquid pumped, either
at least one monitoring system of the liquid delivery rate must be installed in downstream position of the pump or a
monitoring system for the power input into the electric motor. The monitoring system must emit signals to the operator or
control cutting-out of the pump, if it is in a dry state. Such installation is compulsory for all pumps conforming to Group II,
Category 2, but it is also very much advisable on pumps of Group II, Category 3.
The installation of a measuring instrument for the out flowing delivery rate from the pump is advisable to
prevent operation against any obstruction on the delivery side, as described in the following paragraph
7.3. These accessories must be chosen among the ones certified according to the ATEX 94/9/EC
Directive for a grade of protection at least equal or higher to that of the pump which will be monitored.
The correct selection and installation is completely at the account of the end-user, if such systems have
not yet been installed and supplied by POMPETRAVAINI. For further information about the right choice
and installation, please contact POMPETRAVAINI.
During any dry running, all rubbing surfaces inside of the pump will not be lubricated and the heat developed will not be
dissipated by the liquid pumped. When running in a dry state, inside of the pump there is a sudden temperature increase
on some of its components. Due to the consequences of thermal expansion, there might by higher friction or seizing of
the moving parts, requiring higher electric power input to the motor which therefore absorbs more electric current and
may overheat itself.
RESIDUAL RISK: In case of dry running, due to internal frictions, some surfaces of the pump
may become hot and reach temperatures much higher than the Tx temperature for which the
pump has been classified.
After a long period of dry running, the mechanical seal – if it has not been correctly lubricated
and cooled - may no longer be able to contain the liquid pumped. The pump must be stopped
and the mechanical sealing system replaced.
7.3
–
OPERATION AGAINST OBSTRUCTION AT THE DELIVERY SIDE
The pump must
NEVER
run against any obstructions on the delivery
pipe
. The obstructions may depend on different
causes, such as complete closing of the delivery-flow control valve of the pump in delivery.
The adjustment valve on the delivery
pipe
of the pump
only
for start-up and stopping must be set to completely closed
position and only for a certain time established according to the indications in Chapter 11 under paragraph 11.3 of
the Operator’s Manual.
In order to make sure that the pump is not running against any obstacle on the delivery
pipe
, at least one monitoring
system (flow gauges, flow meters, pressure gauges, etc.) must be installed in downstream position
on
the delivery
side of the pump. The monitoring system must have a signal for the operator or a control on the pump