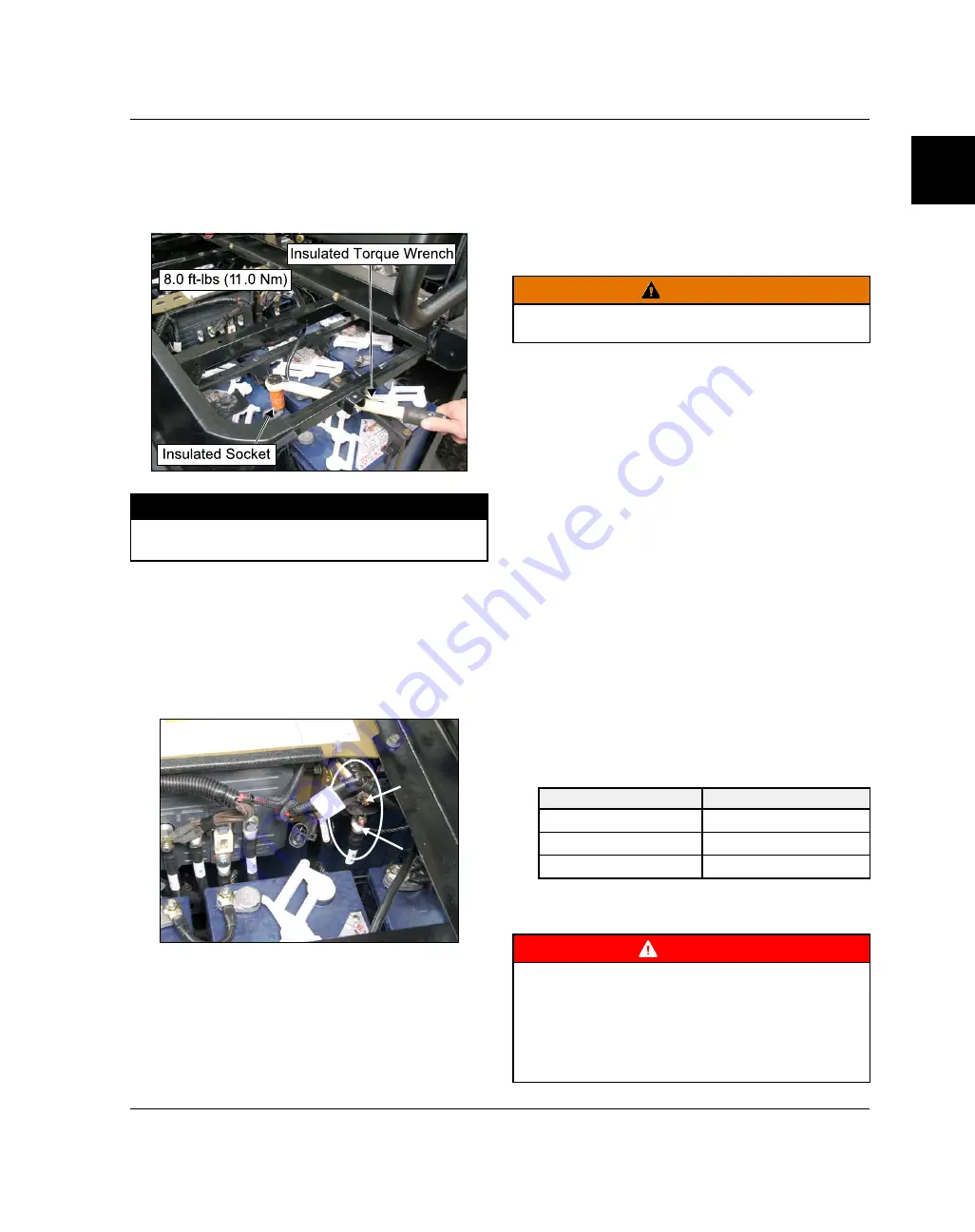
9926595 R01 - 2015-2016
RANGER
EV Service Manual
© Copyright Polaris Industries Inc.
1.21
terminal. Permanent battery damage can result from lack
of terminal maintenance.
Over-tightening
of
terminal
fasteners
can
cause
permanent damage to the battery.
TORQUE
Battery Cable Terminals:
8.0 ft-lbs (11.0 Nm)
Battery
Contactor Terminals:
8.0 ft-lbs (11.0 Nm)
BATTERY CONTACTOR FASTENER
TORQUE
Torque contactor fasteners using insulated tools as
described for the battery terminals above.
Loose
or
over-tightened
contactor
terminals
can
permanently damage the contactor.
BATTERY CLEANING (EXTERNAL
SURFACES)
1.
Turn key OFF.
2.
Remove seat and storage trays.
3.
Disconnect the main electrical connector.
4.
Check to be sure battery caps are in place and
securely latched in the closed position. SeeBattery
Water Level, page 1.22 for vent cap operation.
5.
Mix a solution of one tablespoon baking soda per
one cup of clean water. Wash battery case with
solution to remove acid residue, dirt, and debris.
CAUTION
Do not allow cleaning solution or tap water to enter the
batteries.
6.
Rinse thoroughly with a low pressure stream of water
until batteries are clean. Allow to dry. DO NOT use
pressure washers or compressed air to clean or dry
batteries or contaminants may be forced through the
battery cap vent and contaminate battery cells. Cell
contamination will reduce battery performance and
service life.
BATTERY TERMINAL CLEANING
1.
Disconnect the Main Power Connector, page 1.20.
2.
Using insulated tools, remove the battery cables for
cleaning (SeeBattery Cable Removal, page 1.31).
3.
Clean cables and terminals with a stiff wire brush.
Wash
with
soda/water
solution
(proportions
described below).
4.
Rinse well with tap water and dry off with clean shop
towels.
5.
Reinstall the battery cables (SeeBattery Cable
Installation, page 1.32) in order shown and torque
terminal nuts to 8.0 ft-lbs (10.8 Nm).
6.
Coat battery terminals with dielectric grease or
petroleum jelly.
BATTERY CLEANING SOLUTIONS
PARTS BAKING SODA PARTS WATER
1 Teaspoon (15cc)
1 Cup (.25 Liter)
4 Tablespoons (60cc)
1 Quart (1 Liter)
1 Cup (250cc)
1 Gallon (4 Liters)
BATTERY CHARGING
WARNING
Do not work in or around the battery compartment or on
any electrical component on the vehicle while charging
the batteries. The chassis of the vehicle is at ground
potential when the battery charging cord is connected
to an AC outlet. This increases the risk of accidental
short circuits to battery terminals or other wires caused
by tools or other objects.
Summary of Contents for RANGER EV 2015
Page 4: ......
Page 6: ......
Page 245: ...2015 2016 RGR EV LSV CHASSIS...
Page 246: ...2015 2016 RANGER EV CARGO BOX...
Page 247: ...2015 2016 RGR EV LSV...