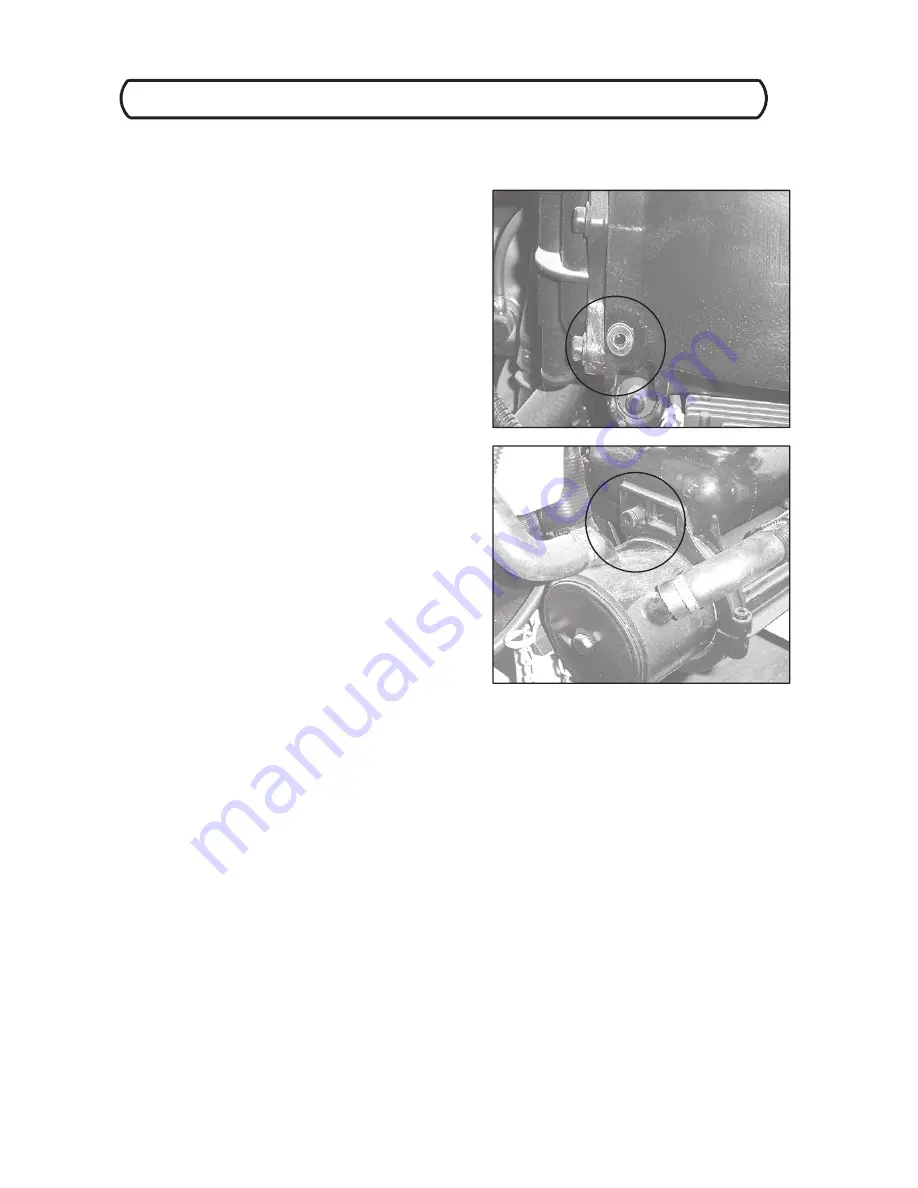
MAINTENANCE
2.25
2004 Four Stroke PWC Service Manual
Drain Plugs
A drain plug is located on the front of the intercooler and on the back of the intake manifold.
1. Intercooler drain plug. Apply marine grade silicone
to threads when reinstalling. Hand tighten.
1. Intake manifold drain plug. Apply marine grade
silicone to threads when reinstalling. Hand tighten.
The drain plugs are designed to allow any water inside of the intercooler or air intake to escape in the event where
the watercraft has rolled over and taken on water.
NOTE: Never operate the watercraft without the drain plugs installed! Severe engine damage may
occur.
Summary of Contents for msx 110
Page 1: ...msx 110 msx 150 Four Stroke Personal Watercraft Service Manual ...
Page 230: ...WIRING DIAGRAMS MSX 110 150 Chassis Harness 62456_Foldouts 3 5 04 8 34 PM Page 1 ...
Page 231: ...WIRING DIAGRAMS MSX 110 150 Engine Harness 62456_Foldouts 3 5 04 8 34 PM Page 2 ...
Page 232: ...WIRING DIAGRAMS MSX 110 150 Engine Harness 62456_Foldouts 3 5 04 8 34 PM Page 3 ...