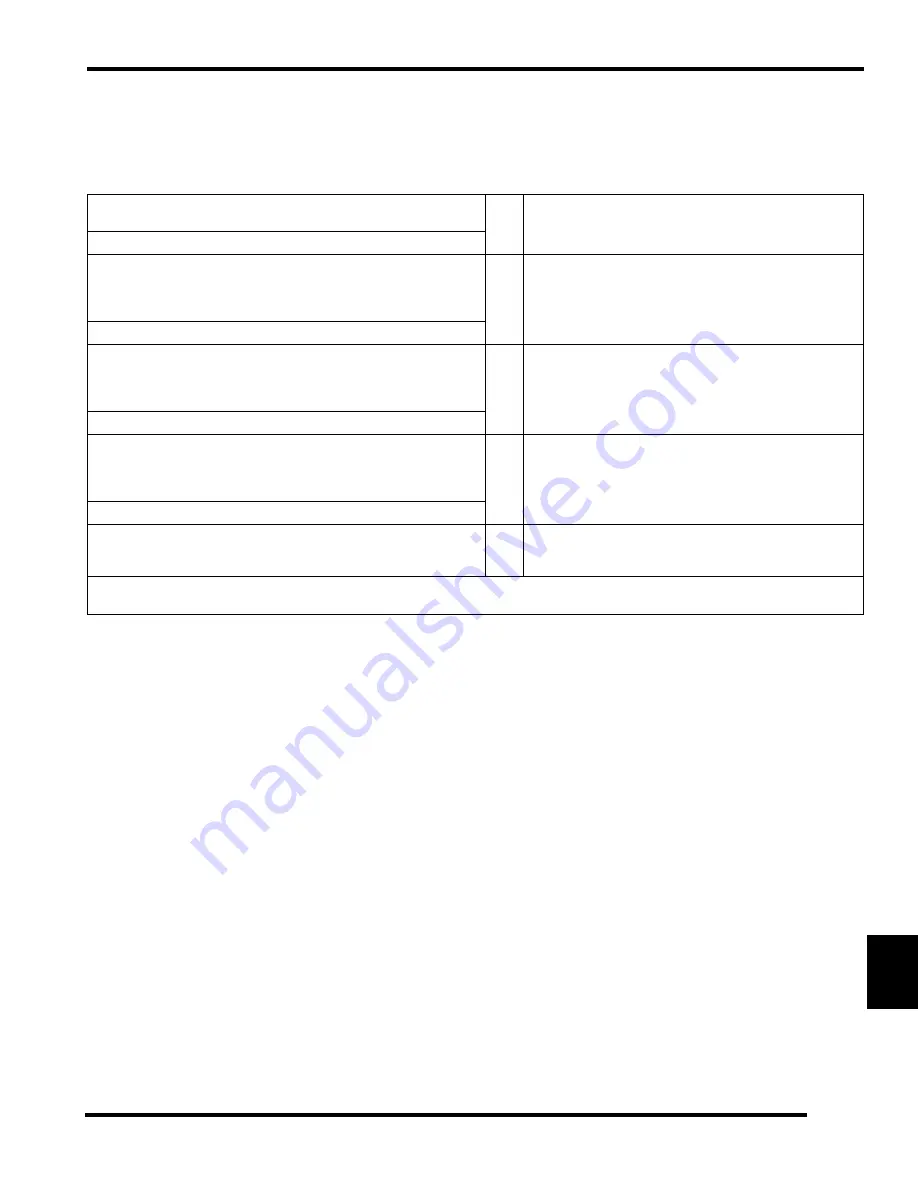
11.15
BATTERY & ELECTRICAL SYSTEMS
11
Dynamic Testing
NOTE: Be sure the engine crankshaft turns freely
before proceeding. Use a digital multimeter during
tests.
Static Testing
1.
Remove starter motor and disassemble. (See page 11.11
for exploded view) Mark end covers and housing for
proper reassembly.
2.
Remove pinion retaining snap ring, spring and pinion gear.
3.
Remove brush end bushing dust cover.
4.
Remove housing through bolts.
5.
Slide brush end frame off end of starter.
NOTE: The electrical input post must stay with the
field coil housing.
6.
Slide positive brush springs to the side, pull brushes out of
their guides and remove brush plate.
7.
Clean and inspect starter components.
NOTE: Some cleaning solvents may damage the
insulation in the starter. Care should be exercised
when selecting an appropriate solvent. The brushes
must slide freely in their holders. If the commutator
needs cleaning, use only an electrical contact
cleaner and/or a non-metallic grit sandpaper.
Replace brush assembly when worn to 5/16, (.8 cm)
or less.
Starter Housing / Field Coil Testing
1.
Using a digital multimeter, measure resistance between
starter input terminal and insulated brushes. The reading
should be.3 ohms or less.
2.
Measure resistance between insulated brushes and field coil
housing. The reading should be infinite.
3.
Inspect insulated brush wire and field coil insulation for
damage. Repair or replace components as required.
Armature Testing
1.
Using a digital multimeter, measure resistance between
each of the segments of the commutator. The reading
should indicate.3 ohms or less.
2.
Measure resistance between commutator and armature
shaft. Reading should be infinity.
3.
Place armature in a growler. With the growler on, position
a hacksaw blade lengthwise 1/8, (.03 cm) above armature
coil laminates. Rotate armature 360
_
. If hacksaw blade is
drawn to the armature on any pole, the armature is shorted
and must be replaced.
Test battery voltage. Is the battery voltage equal to or greater than
12.8 Vdc?
NO
Remove battery, test and/or service. Install a fully
charged shop battery to continue the test and continue
with left column
YES
Disconnect two-pin harness from starter solenoid. Connect black
multimeter probe to the engine or ground, then the red probe to the
red harness wire at solenoid. Rotate ignition key to the start
position. Meter should read battery voltage. Does it?
NO
With black tester lead on ground, check for voltage at
large relay terminal, circuit breaker in and out terminals,
and across both sides (red and red/white) of the ignition
switch with switch on start. Repair or replace any
defective parts.
YES
Reconnect the solenoid harness. Connect black probe to battery
positive terminal and red probe to solenoid end of battery to
solenoid cable. (B) Page 13.9. Turn key to start position. The
reading must be less than.1V DC. Is it?
NO
Clean battery to solenoid cable ends or replace cable.
YES
Connect black tester lead to solenoid end of solenoid to starter
cable and red tester lead to starter end of same cable. (D) Page
13.9. Turn key to start position. The reading must be less than.1V
DC. Is it?
NO
Replace starter solenoid.
YES
Connect black tester lead to starter frame. Connect red tester lead
to battery negative (-) terminal. (E) Page 13.9. Turn key to start
position. The reading should be less than.1V DC. Is it?
NO
Clean ends of engine to battery negative cable or replace
cable.
If all these tests indicate a good condition, yet the starter still fails to turn, or turns slowly, the starter must be remove for static testing
and inspection.
Summary of Contents for 340 LX 2007
Page 4: ......
Page 40: ...NOTES MODEL SPECIFICATIONS 1 36...
Page 51: ...2 11 GENERAL 2 SPECIAL TOOLS Special Tools...
Page 52: ...2 12 GENERAL...
Page 53: ...2 13 GENERAL 2...
Page 54: ...2 14 GENERAL...
Page 80: ...NOTES MAINTENANCE 3 26...
Page 91: ...4 11 FUEL DELIVERY 4 Throttle Opening Vs Fuel Flow VM only...
Page 104: ...NOTES FUEL DELIVERY 4 24...
Page 114: ...5 10 ENGINE 500 600 Touring WideTrak LX Touring WideTrak...
Page 146: ...NOTES ENGINE 5 42...
Page 170: ...NOTES CLUTCHING 6 24...
Page 214: ...NOTES FRONT SUSPENSION STEERING 8 20...
Page 259: ...10 11 CHASSIS HOOD 10...
Page 260: ...NOTES CHASSIS HOOD 10 12...
Page 272: ...11 12 BATTERY ELECTRICAL SYSTEMS ELECTRIC START GEN II EDGE System Schematic...
Page 277: ...11 17 BATTERY ELECTRICAL SYSTEMS 11 System Schematic 600 700 CFI...
Page 286: ...11 26 BATTERY ELECTRICAL SYSTEMS Chassis Relay...
Page 288: ...11 28 BATTERY ELECTRICAL SYSTEMS Vehicle Speed Sensor...
Page 293: ...11 33 BATTERY ELECTRICAL SYSTEMS 11 CFI Power System CFI Ignition Injection Power...
Page 294: ...11 34 BATTERY ELECTRICAL SYSTEMS CFI Crank Position System CFI Safety Stop System...
Page 295: ...11 35 BATTERY ELECTRICAL SYSTEMS 11 CFI Full Load Fuel Injectors CFI Part Load Fuel Injectors...
Page 296: ...11 36 BATTERY ELECTRICAL SYSTEMS CFI Chassis Power CFI Ignition Coils...
Page 297: ...11 37 BATTERY ELECTRICAL SYSTEMS 11 CFI TBAP Sensor CFI TPS Engine Temp Sensors...
Page 298: ...11 38 BATTERY ELECTRICAL SYSTEMS CFI Exhaust Solenoid CFI Knock Sensor...
Page 299: ...11 39 BATTERY ELECTRICAL SYSTEMS 11 CFI Fuel Pump CFI Diagnostic Connections...
Page 300: ...11 40 BATTERY ELECTRICAL SYSTEMS CFI MFD Circuits CFI MFD Power Circuits...
Page 301: ...11 41 BATTERY ELECTRICAL SYSTEMS 11 CFI Fuel Level Circuit CFI Vehicle Speed Circuit...
Page 302: ...11 42 BATTERY ELECTRICAL SYSTEMS CFI Mode Set Switch CFI PERC Switch...
Page 318: ...12 1 Wiring Diagrams 2007 340 550 GEN II EDGE Models...
Page 319: ...12 2 Wiring Diagrams 2007 Wide Trak...
Page 320: ...12 3 Wiring Diagrams 2007 500 XCSP...
Page 321: ...12 4 Wiring Diagrams 2007 600 HO Carbureted 1 of 2...
Page 322: ...12 5 Wiring Diagrams 2007 600 HO Carbureted 2 of 2...
Page 323: ...12 6 Wiring Diagrams 2007 600 HO Carbureted Hood Harness...
Page 324: ...12 7 Wiring Diagrams 2007 600 700 CFI 1 of 2...
Page 325: ...12 8 Wiring Diagrams 2007 600 700 CFI 2 of 2...
Page 327: ...12 10 Wiring Diagrams...