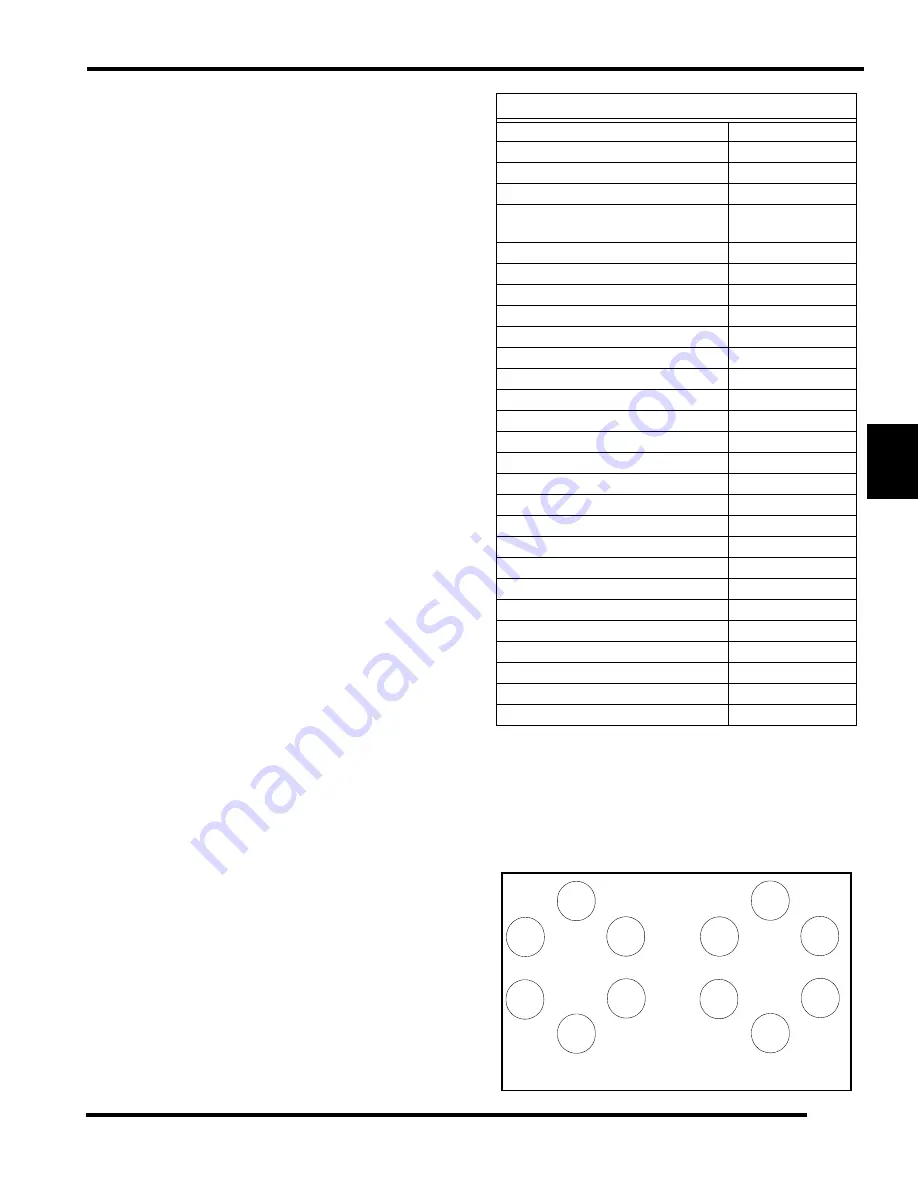
5.23
ENGINE
5
1.
Remove the spark plugs (1)
2.
Remove reed valve assembly. See “Reed Valve
Disassembly” on page 5.3.
3.
Remove the recoil and stator assembly. See “Recoil/Stator
Removal” on page 5.7.
4.
Remove the head bolts (2).
5.
Remove the head cover (10) and the rubber head seals (11).
6.
Remove the head (13) and cylinder o-rings (14).
7.
Remove the VES assembly. See “Exhaust Valve
Disassembly” on page 5.3.
8.
Remove the cylinder nuts (15) and carefully remove the
cylinders (16) with a slight rocking motion.
9.
Remove the c-clips that hold the wrist pin into the piston.
10. Using the piston pin puller PN PU-45255 remove the piston
pins, and the piston (17) from the crankshaft rod.
11. Remove the water/oil pump assembly. See “500/600/700
Water/Oil Pump Cross Shaft Disassembly” on page 5.6.
12. If removing the engine mounting straps (these straps are
mounted to the engine and bulkhead) label the direction and
placement of each engine strap.
13. Remove the cylinder base gaskets (18) and replace them if
damaged.
14. Turn over the crankcase and remove the bottom crankcase
bolts (31).
15. Turn the crankcase assembly back over and remove the top
of the crankcase (20).
16. Remove the crankshaft assembly (22-29), and refer to the
General chapter for general engine component inspections
and measurement procedures
.
17. If new cases are to be installed make sure that the new
cylinder studs are installed to the correct length. See
“Cylinder Stud Installation” on page 5.5.
500/600 (Carbureted) Torques
When tightening bolts, nuts, or screws, a torque pattern may
need to be followed to ensure uniform equal tension is applied
to all fasteners. Proper torque application prevents fasteners
from loosening or breaking in critical service. It also minimizes
wear and eliminates premature or needless repair costs.
Following uniform torque application sequence patterns
ensures optimum performance from precision machined, close
tolerance assemblies.
The most common units of torque in the English system are ft-
lb (foot pounds) and in-lb (inch pounds). In the Metric system,
torque is commonly expressed in units of N-m (Newton
Meter).
1
=Apply Loctite 242 to threads of bolt.
2
= Apply Pipe sealant to threads.
3
= See torque sequence.
500/600 (Carbureted) Cylinder Head Torque
Pattern
ENGINE 500/600
SPARK PLUG
18 ft-lb (24 N-m)
CYLINDER HEAD
22ft-lb (30 N-m)
1
,
3
BLEEDER SCREW
70 in-lb (8 N-m)
THERMOSTAT HOUSING
9 ft-lb (12 N-m)
WATER TEMPERATURE SENSOR
18-40ft-lb
(24-54 N-m)
2
WATER INLET PIPE
75ft-lb (102 N-m)
2
DETIONATION SENSOR
168 in-lb(19 N-m)
CYLINDER BASE NUTS
32 ft-lb (43 N-m)
3
EXHAUST VALVE COVER BOLTS
12 ft-lb (16 N-m)
EXHAUST VALVE NUT
144 in-lb (16 N-m)
1
EXHAUST MANIFOLD BOLTS
22 ft-lb (30 N-m)
CARB ADAPTER BOLTS
108 in-lb (12 N-m)
OIL PUMP MOUNTING BOLTS
7 ft-lb (9 N-m)
CRANCASE PLUGS
10ft-lb (14 N-m)
2
WATER PUMP IMPELLER NUT
120 in-lb (14 N-m)
WATER PUMP COVER BOLTS
108 in-lb (12 N-m)
CRANKCASE 6mm
9ft-lb (12 N-m)
1
,
3
CRANKCASE 8mm
22ft-lb (30 N-m)
1
,
3
ENGINE STRAP to CHASSIS NUT
18ft-lb (24 N-m)
ENGINE STRAP to ENGINE BOLT
45 ft-lb (61 N-m)
STATOR BOLTS
60 in-lb(7 N-m)
1
TRIGGER COIL BOLTS
48 in-lb (5 N-m)
FLYWHEEL
90ft-lb (122 N-m)
1
RECOIL CUP BOLTS
108 in-lb (12 N-m)
RECOIL COVER COLTS
108 in-lb (12 N-m)
DRIVE CLUTCH BOLT
50 ft-lb(68 N-m)
7/16” ENGINE MOUNT STRAP BOLTS
45 ft-lb (61 N-m)
REAR MOTOR MOUNTS BRACKET
29 ft-lb (39 N-m)
1
2
3
4
5
6
7
8
9
10
MAG
PTO
12
11
Head Pattern
22 ft-lb (30 N-m)
Summary of Contents for 340 LX 2007
Page 4: ......
Page 40: ...NOTES MODEL SPECIFICATIONS 1 36...
Page 51: ...2 11 GENERAL 2 SPECIAL TOOLS Special Tools...
Page 52: ...2 12 GENERAL...
Page 53: ...2 13 GENERAL 2...
Page 54: ...2 14 GENERAL...
Page 80: ...NOTES MAINTENANCE 3 26...
Page 91: ...4 11 FUEL DELIVERY 4 Throttle Opening Vs Fuel Flow VM only...
Page 104: ...NOTES FUEL DELIVERY 4 24...
Page 114: ...5 10 ENGINE 500 600 Touring WideTrak LX Touring WideTrak...
Page 146: ...NOTES ENGINE 5 42...
Page 170: ...NOTES CLUTCHING 6 24...
Page 214: ...NOTES FRONT SUSPENSION STEERING 8 20...
Page 259: ...10 11 CHASSIS HOOD 10...
Page 260: ...NOTES CHASSIS HOOD 10 12...
Page 272: ...11 12 BATTERY ELECTRICAL SYSTEMS ELECTRIC START GEN II EDGE System Schematic...
Page 277: ...11 17 BATTERY ELECTRICAL SYSTEMS 11 System Schematic 600 700 CFI...
Page 286: ...11 26 BATTERY ELECTRICAL SYSTEMS Chassis Relay...
Page 288: ...11 28 BATTERY ELECTRICAL SYSTEMS Vehicle Speed Sensor...
Page 293: ...11 33 BATTERY ELECTRICAL SYSTEMS 11 CFI Power System CFI Ignition Injection Power...
Page 294: ...11 34 BATTERY ELECTRICAL SYSTEMS CFI Crank Position System CFI Safety Stop System...
Page 295: ...11 35 BATTERY ELECTRICAL SYSTEMS 11 CFI Full Load Fuel Injectors CFI Part Load Fuel Injectors...
Page 296: ...11 36 BATTERY ELECTRICAL SYSTEMS CFI Chassis Power CFI Ignition Coils...
Page 297: ...11 37 BATTERY ELECTRICAL SYSTEMS 11 CFI TBAP Sensor CFI TPS Engine Temp Sensors...
Page 298: ...11 38 BATTERY ELECTRICAL SYSTEMS CFI Exhaust Solenoid CFI Knock Sensor...
Page 299: ...11 39 BATTERY ELECTRICAL SYSTEMS 11 CFI Fuel Pump CFI Diagnostic Connections...
Page 300: ...11 40 BATTERY ELECTRICAL SYSTEMS CFI MFD Circuits CFI MFD Power Circuits...
Page 301: ...11 41 BATTERY ELECTRICAL SYSTEMS 11 CFI Fuel Level Circuit CFI Vehicle Speed Circuit...
Page 302: ...11 42 BATTERY ELECTRICAL SYSTEMS CFI Mode Set Switch CFI PERC Switch...
Page 318: ...12 1 Wiring Diagrams 2007 340 550 GEN II EDGE Models...
Page 319: ...12 2 Wiring Diagrams 2007 Wide Trak...
Page 320: ...12 3 Wiring Diagrams 2007 500 XCSP...
Page 321: ...12 4 Wiring Diagrams 2007 600 HO Carbureted 1 of 2...
Page 322: ...12 5 Wiring Diagrams 2007 600 HO Carbureted 2 of 2...
Page 323: ...12 6 Wiring Diagrams 2007 600 HO Carbureted Hood Harness...
Page 324: ...12 7 Wiring Diagrams 2007 600 700 CFI 1 of 2...
Page 325: ...12 8 Wiring Diagrams 2007 600 700 CFI 2 of 2...
Page 327: ...12 10 Wiring Diagrams...