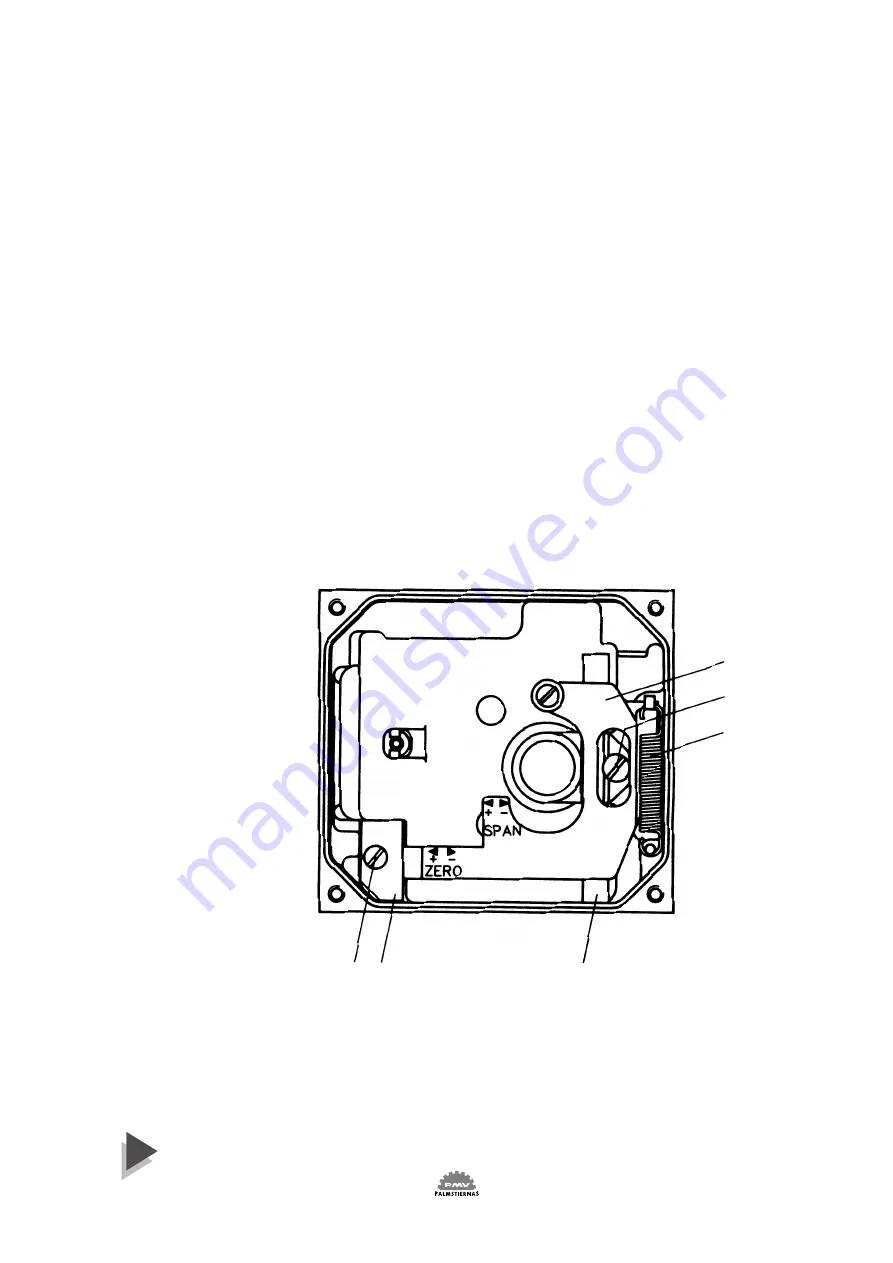
– 18 –
Manual P5/EP5 23740/98.10
Lower arm
O-rings
Once the front cover is removed, the lower arm can be easily accessed.
Remove the indicator, feedback spring and the cam.
Loosen screw 2 and remove twist stop 1.
Remove screw 3, lower arm 4, rod 5 and spring 6.
Check rod and lower arm for wear, replace if necessary. Clean the rod
and install it in the lower arm. The lower arm should move easily and
smoothly.
Install the lower arm and rod assembly into the positioner housing,
making sure that the spring 6 is attached properly to the lower arm
and positioner housing.
Secure the lower arm and rod assembly with the screw 3.
Check again that the lower arm moves smoothly.
Apply a small amount of grease on the small tongue on the lower arm,
then install and secure the twist stop.
Install cam, feedback spring, indicator and front cover.
With time and use, O-rings can become brittle. This can cause poor
operation and even failure of the positioner.
Always check O-rings when performing any work on the positioner
and replace bad O-rings.
A thin layer of silicon grease applied on the NBR (Black) O-rings
prolongs their life. On Q (red) O-rings, use a non silicon based grease.
6
2 1 5
4
3
Summary of Contents for EP5
Page 1: ... 1 Manual P5 EP5 23740 98 10 Manual P5 EP5 PMV Valve Control System alve Control System ...
Page 22: ... 22 Manual P5 EP5 23740 98 10 17 Exploded Drawing 98 9 84 ...
Page 24: ... 24 Manual P5 EP5 23740 98 10 Approvals E5 IS EU ...
Page 25: ... 25 Manual P5 EP5 23740 98 10 Approvals E5 EX EU ...
Page 26: ... 26 Manual P5 EP5 23740 98 10 Approvals E5 IS US E5 EX US 1 ...
Page 27: ... 27 Manual P5 EP5 23740 98 10 Approvals E5 IS US E5 EX US 2 ...
Page 29: ... 29 Manual P5 EP5 23740 98 10 FM ...
Page 30: ... 30 Manual P5 EP5 23740 98 10 CSA ...