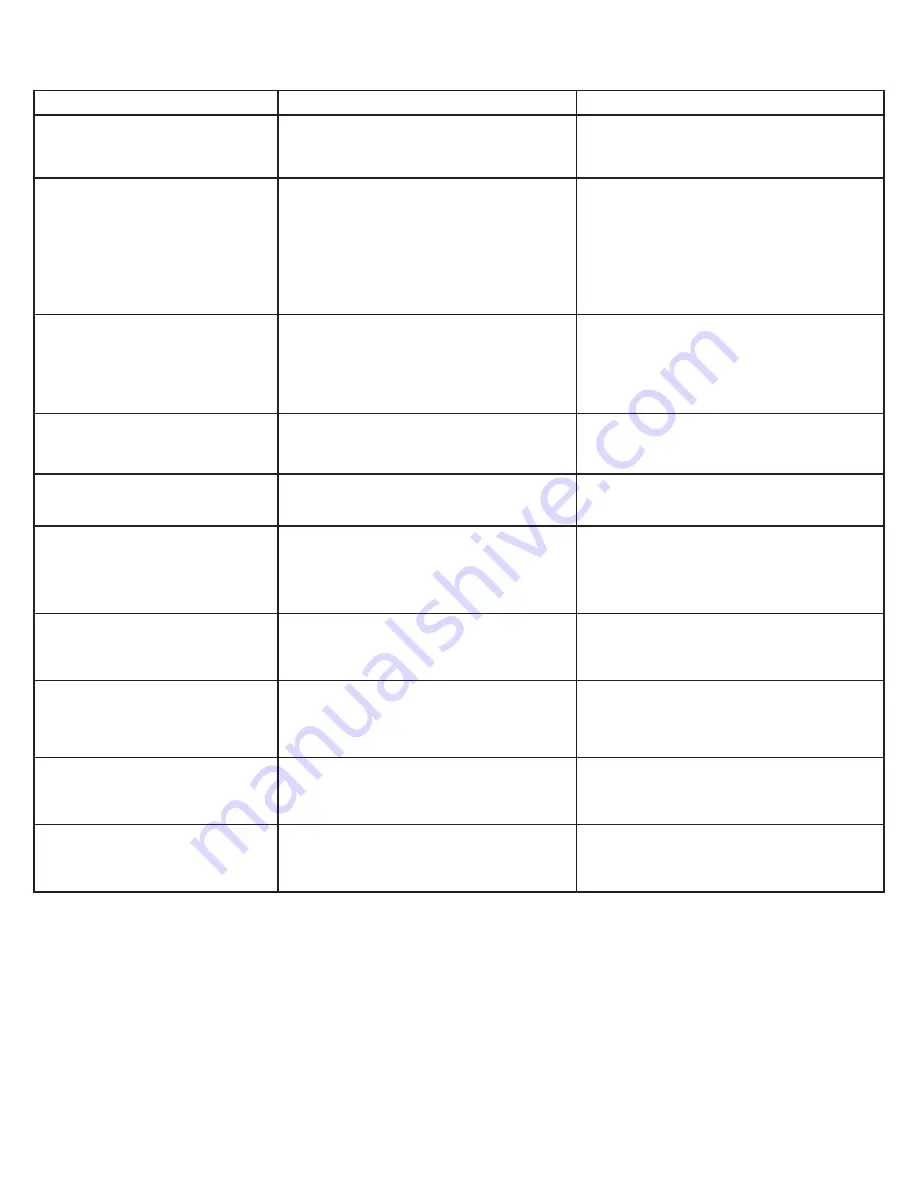
01-999-2534
Page 9
TROUBLESHOOTING:
The following guide is intended to help you diagnose and fix some of the most commonly encountered problems; by no means does
this guide cover all of the possible problems you may encounter. If you cannot diagnose and correct the problem, or if it persists,
contact qualified service personnel. All electrical work should be done by, or with the help of, a qualified electrician.
PROBLEMS / SYMPTOMS POSSIBLE CAUSE
CORRECTIVE ACTION
Water draining from the unit
1. Float valve out of adjustment
2. Float movement obstructed
3. Float valve non-functional
1. Adjust float to 2-2-1/2" water depth.
2. Free float from obstruction
3. Replace float assembly
Dry Media
1. Pump intake clogged
2. Non-functional water pump
3. Clogged water line
4. Water distributor clogged
5. Non-functional switch
6. Non-functional wiring
7. Water turned off to cooler
1. Remove obstruction
2. Replace water pump
3. Locate and free obstruction
4. Clear debris from water distributor
5. Replace switch
6. Repair or replace non-functional wiring
7. Turn on water supply
Motor does not start or no air
delivery
1. Electrical power disconnected
2. Circuit breaker tripped or fuse blown
3. Non-functional motor
4. Non-functional switch
5. Broken belt
1. Check power receptacle and cord
2. Determine cause and correct
3. Replace motor
4. Replace switch
5. Replace belt
Inadequate air delivery
1. Excessive belt tension
2. Blower wheel loose on motor shaft
3. Pads clogged
1. Adjust belt tension
2. Tighten wheel set screw
3. Replace pads
Noisy operation
1. Blower rubbing on housing
2. Motor or blower mounting screws loose
1. Reposition wheel
2. Tighten screws
Musty or unpleasant odor
1. Stale or stagnant water in cooler
2. Media pads clogged or mildewed
3. Media pads not completely wet before
starting fan motor
1. Drain, clean, and flush reservoir
2. Replace media pads
3. Turn pump ON for several minutes prior
to starting cooler
Motor cycles on & off
1. Low voltage
2. Motor shaft tight or frozen
3. Pad frame or air outlet grille removed
1. Check voltage
2. Replace motor
3. Re-install pad frame or air outlet grille
No power at convience outlet
1. Electrical power disconnected
2. Circuit breaker on unit tripped
1. Check power receptacle and cord
2. Reset circuit breaker and ensure the
max amp draw on the outlet is not being
exceeded
Remote does not work
1. Remote does not have line of sight to
unit.
2. Remote battery is dead
1. Remove any obstructions in the way of
the unit
2. Replace the remote battery
Poor bluetooth reception
1. Signal blocked by obstructions
2. Interference from wifi
1. Move unit
2. Turn wifi off on the device that is
connected to the unit
REPLACEMENT PARTS
When ordering replacement parts, always refer to the serial number and model number of your cooler. Use the part numbers listed in the
accompanying parts list, as illustrated in the diagrams for your model.