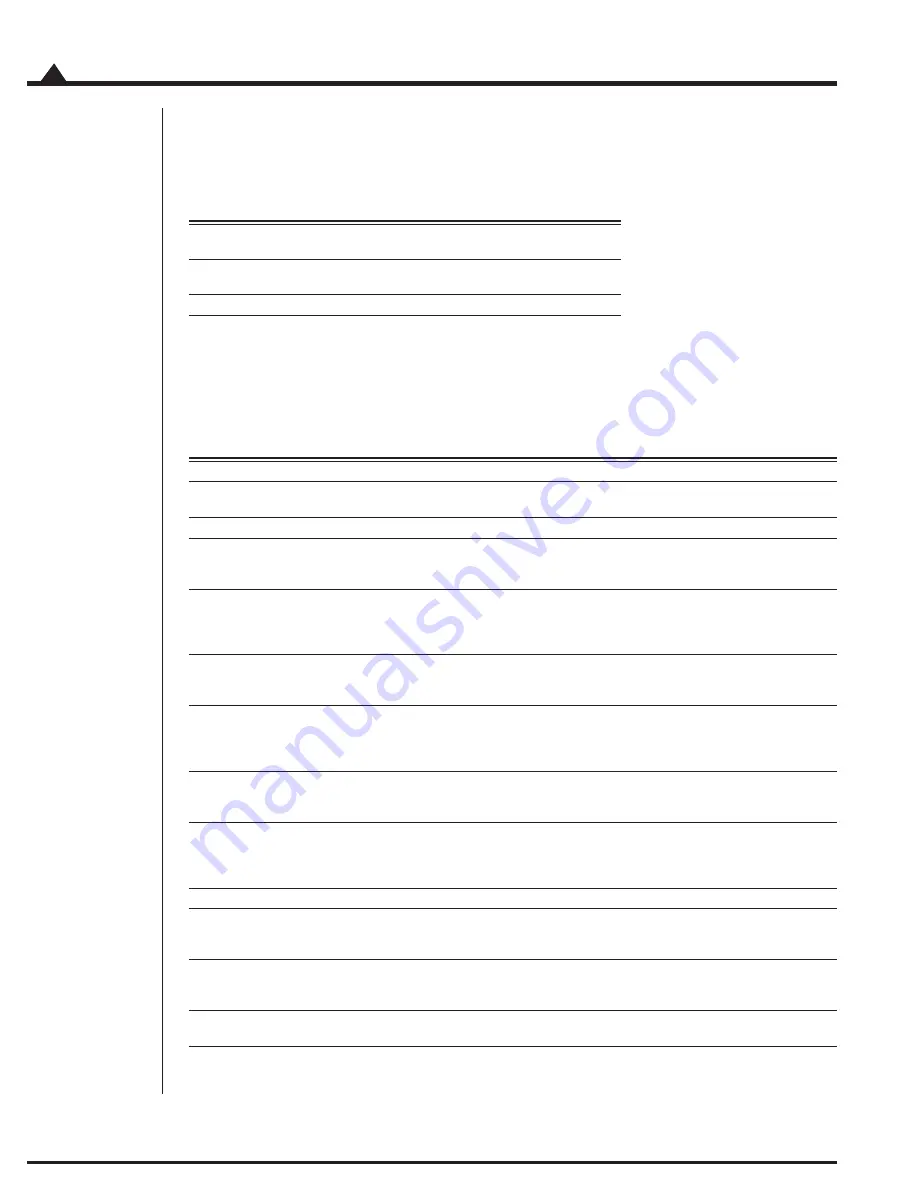
MC73110 Developer’s Kit Manual
16
Installation
2
2.7.2 Power Connector (J1)
The power connector provides power to the card. All other voltages used by the card are derived from this central
supply using an on-card DC-DC converter. The voltage provided at these connections matches the voltage at
which the motor will be driven.
Pin # Signal
Description
name
1
V+
18 - 48V. Current capacity specification should be
maximum motor drive + 1amp (to power the card)
2
PowerGnd Ground return for V+
2.7.3 Motor Feedback Connector (J2)
The motor feedback connector inputs various motor-related signals to the Developer’s Kit card. All these signals
are low power, low voltage digital or analog signals.
Pin # Signal
Description
1
+5V
This signal provides 5V.
This is often useful to power the encoder circuitry.
2
GND
This signal provides the digital return.
3
QuadA+
This input signal provides the high side of the differential quadrature input for encoder
phase A. For more information on connecting encoders see
section 2.6, Preparing the
Card for Installation, page 14.
If unused this signal may be left unconnected.
4
QuadA-
This input signal provides the low side of the differential quadrature input for encoder
phase A. When using a single-ended encoder, this pin should be left unconnected. For
more information on connecting encoders see
section 2.6, Preparing the Card for
Installation, page 14.
If unused this signal may be left unconnected.
5
QuadB+
This input signal provides the high side of the differential quadrature input for encoder
phase B. For more information on connecting encoders see
section 2.6, Preparing the
Card for Installation, page 14.
If unused this signal may be left unconnected.
6
QuadB-
This input signal provides the low side of the differential quadrature input for encoder
phase B. When using a single-ended encoder, this pin should be left unconnected. For
more information on connecting encoders see
section 2.6, Preparing theCard for
Installation, page 14.
If unused this signal may be left unconnected.
7
Index+
This input signal provides the high side of the differential quadrature input for the
Index signal. For more information on connecting encoders see
section 2.6, Preparing
the Card for Installation, page 14.
If unused this signal may be left unconnected.
8
Index-
This input signal provides the low side of the differential quadrature input for the Index
signal. When using a single-ended encoder, this pin should be left unconnected. For
more information on connecting encoders see
section 2.6, Preparing theCard for
Installation, page 14.
If unused this signal may be left unconnected.
9
GND
This signal provides the digital return.
10
HallA
These signals are the Hall sensor inputs. For logic “0”, the signal should be lower than
11
HallB
0.5V; for logic “1”, the signal should be greater than 1.5V.
12
HallC
13
This is the positive input signal for the analog tachometer signal. This signal represents
the instantaneous speed of the motor. The input range is +/- 60V. If unused this signal
may be left unconnected.
14
TachIn- (GND)
This is the negative input for the analog tachometer signal. The input range is +/- 60V.
If unused this signal may be left unconnected.