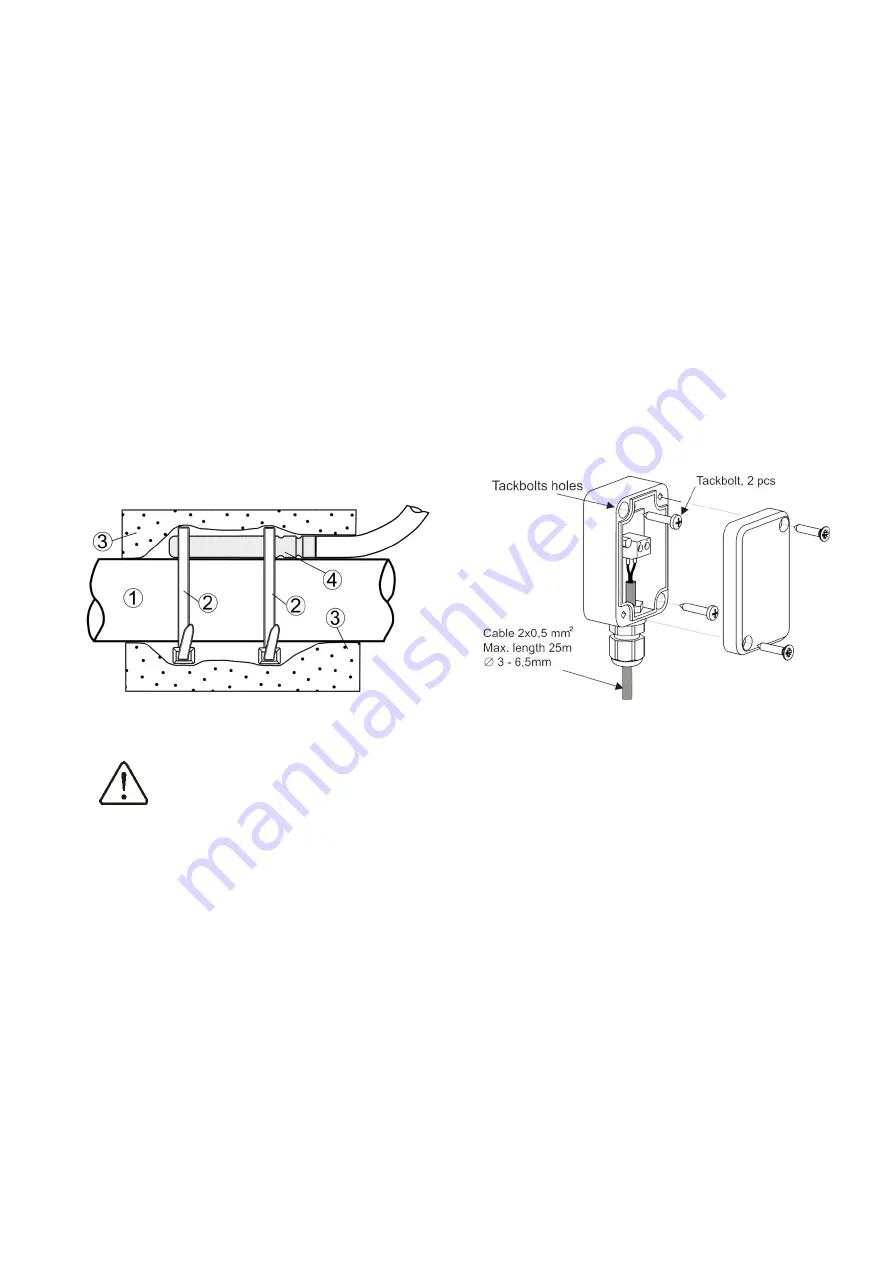
26
12.9
Connection of temperature
sensors
Regulator works with sensors - type CT4 and
CT2S only. Use of other sensors is not
allowed.
Sensor wires may be extended using wires of
cross-section area not less than 0,5mm
2
.
Total length of wires of each sensor should
not exceed 15m.
Insert boiler temperature sensor into
thermometer well fastened to boiler shell.
Fasten feeder temperature sensor to the
surface of feeder screw tube. Insert
temperature sensor of HUW container into
thermometer well welded to the container.
The best way to mount mixer temperature
sensor is to insert it into a sleeve located in
the stream of flowing water, however, it is
also allowed to fasten the sensor in a contact
manner provided that the sensor and the
pipe are properly heat-insulated.
Mounting temperature sensor: 1 - pipe, 2 –
clamps, 3 - thermal insulation, 4 - temperature
sensor.
Sensors shall be protected against
loosening from surfaces they are
mounted to.
Make sure thermal contact between the
sensors and the surface which temperature is
measured is good. Apply thermal paste to
improve the contact. Pouring sensors with oil
or water is not allowed.
Sensor wires should be separated from
power supply wires. Otherwise, temperature
indications may be erroneous. Min. distance
between these wires should be 100mm.
Do not allow sensor wires to contact hot
parts of the boiler and heating system. Wires
of temperature sensors are heat resistant to
the temperature not exceeding 100°C.
12.10
Connection of weather sensor
Regulator works with weather sensors type
CT6-P only. Fasten the weather sensor on
the coldest wall of the building - usually it is
a roofed area of north wall. The sensor
should not be exposed to direct sunlight or
rainfall. Install the sensor at the height of
min. 2m above ground level in the location
away from windows, chimneys and other
heat
sources,
which
may
interfere
temperature measurements (min. distance:
1,5m).
Use cable of wire with cross section area of
min. 0,5mm
2
and length of up-to 25m to
connect the sensor. Wire polarization is
irrelevant. Connect other cable end to
regulator terminals.
Bolt the sensor to the wall using erection
bolts. Holes for bolts are accessible upon
removal of sensor housing lid.
12.11
Connecting exhaust sensor
The exhaust sensor should be fitted in the
boiler flue. The gap between the sensor and
the flue should be sealed. The sensor should
be installed by a qualified fitter, while
observing regulations applicable for chimney
systems. The emission sensor should be
connected to the sensor terminals acc. to
The emission sensor lead cannot touch hot
elements of the boiler and the flue, the
temperature of which exceeds 350°C. The
emission sensor should be installed in such
distance from the boiler at which it is not
directly exposed to flames, and where the
emission temperature does not exceed
450°C.
Summary of Contents for ecoMAX860P3-LZ
Page 6: ...6 ...
Page 7: ...INSTRUCTION MANUAL ecoMAX860P3 LZ ...
Page 17: ...INSTALLATION AND SERVICE SETTINGS ecoMAX860P3 LZ ...
Page 41: ...41 ...
Page 42: ...42 ...
Page 43: ...43 ...
Page 44: ...ul Wspólna 19 Ignatki 16 001 Kleosin Poland plum plum pl www plum pl ...