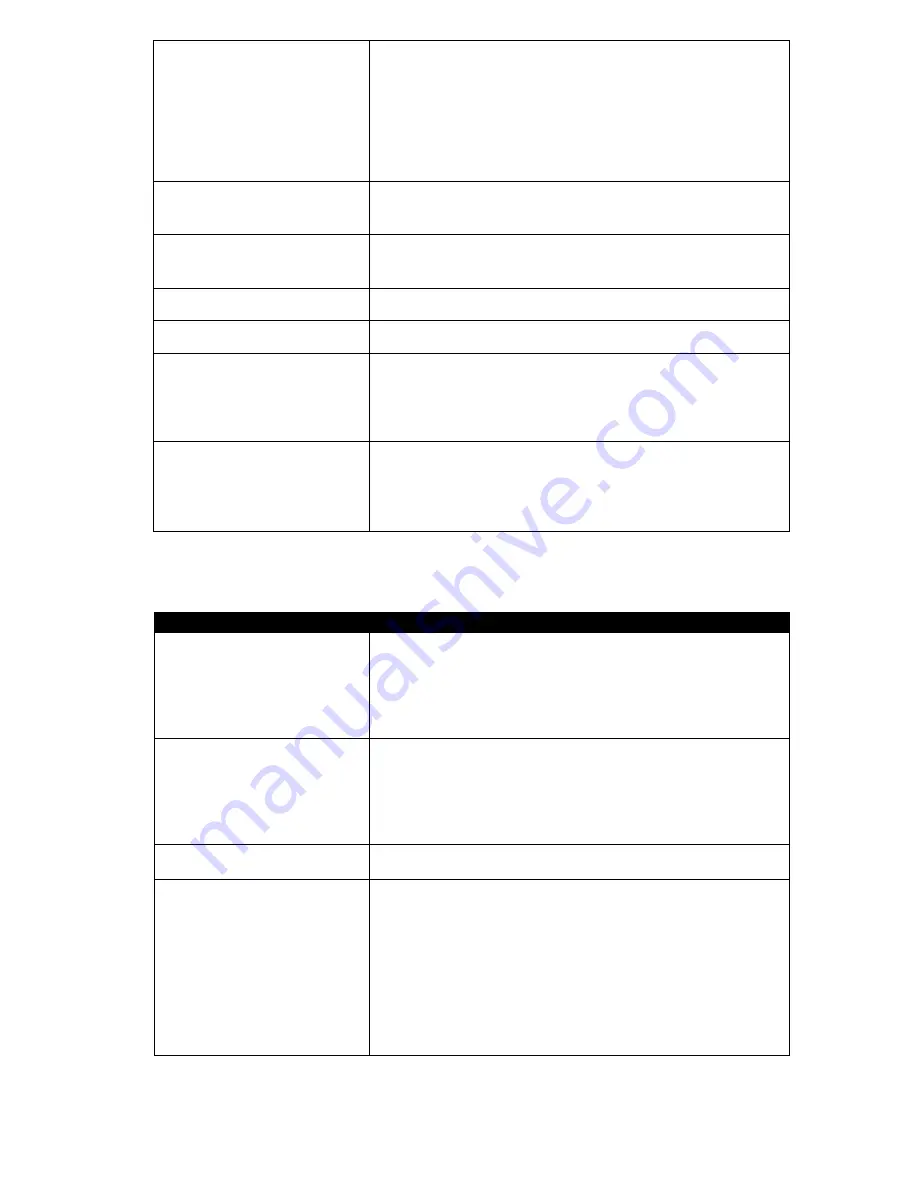
36
Return protection*
Group of parameters available after connecting return sensor,
responsible for protection of boiler return in hydraulic installation with 4
way valve equipped in mixer servomotor, point 9.1. It is not advised to
activate functions of return protection because it may cause frequent
stops in power of mixer cycle. Instead this it is recommended to use
bigger preset temperatures of boiler (70-75%) what in combination with
installation with 4 way valve (with servomotor) it will cause automatic
increase return temperature.
Min. boiler timep
Minimum preset boiler temperatur
ę which can be set in user menu and
minimum temp. which can be set automatically by controller, i.e. from
night reductions etc.
Max. biler time
Maximum
preset boiler temperaturę which can be set in user menu and
minimum temp. which can be set automatically by controller, i.e. from
night reductions etc.
Reserve boiler
Description in point 12.2
Alarms
Description in point 12.3
Boiler cooling temperature
Temperature of boiler cooling off.
Above this temperaturę the controller
activates HW pump and opens mixer cycles to allow boiler cooling off.
The controller activates HW pump if this temperature exceeds maximum
value. The controller will not open mixer cycle when
mixer setting
=
floor
active
Pump off by therm.
Options available
NO (CH boiler pump is not activated when room thermostat starts
operation),
YES (CH boiler pump is deactivated when room thermostat starts
operating)
14.3
CH and HW SERVICE SETTINGS
CH and HUW settings
CH activation temperature
Parameters determines the tempera
turę at which CH boiler pump is
activated. It protects the boiler against watering due to cooling off with
cold water returning from installation. Attention: Deactivating boiler pump
only does not guarantee boiler protection against watering and
consequently corrosion. Additional automatics should be used, i.e. 4 way
valve or 3 way thermostatic valve.
CH stand loading pause when HW l*
Available after connecting HW sensor. Prolonged feeding of HW silo
during priority HW deactivated may cause to overcooling of the CH
installation, because CH pump is deactivated. Parameter CH pump
pause during feeding HW prevents against periodical activating CH
pump during feeding HW silo. CH pump after this time will activate on
constant, programmed time of 30s.
Min. HUW temp. *
Available after CH sensor connecting. It is a parameter by which it can
be reduced setting too low preset HW temperature.
Max .HUW. temp. *
Available after connecting HW sensor. Parameter determines to what
maximum temperaturę HW silo will be heated during cooling the boiler in
alarm situations. It is a very important parameter, because setting too
high value of it may cause risk of scalding with HW. Too low value of
parameter will cause that during boiler overheating it will not be possible
to cool off the boiler to the HW silo. During design of HW installation, it is
necessary to take into account risk of damaging the controller. Due to
breakdown of the controller water in the silo can heat up to dangerous
temperature. It is necessary to use additional protection in the form of
thermostatic valves.
Summary of Contents for ecoMAX850P1-A
Page 2: ......
Page 4: ...4 ...
Page 7: ...USER MANUAL OF THE CONTROLLER ecoMAX850P A ...
Page 19: ...19 USER MANUAL OF CONTROLLER INSTALLATION AND SERVICE SETTINGS ecoMAX850P A ...
Page 45: ...45 ...
Page 46: ...46 ...
Page 47: ...47 ...