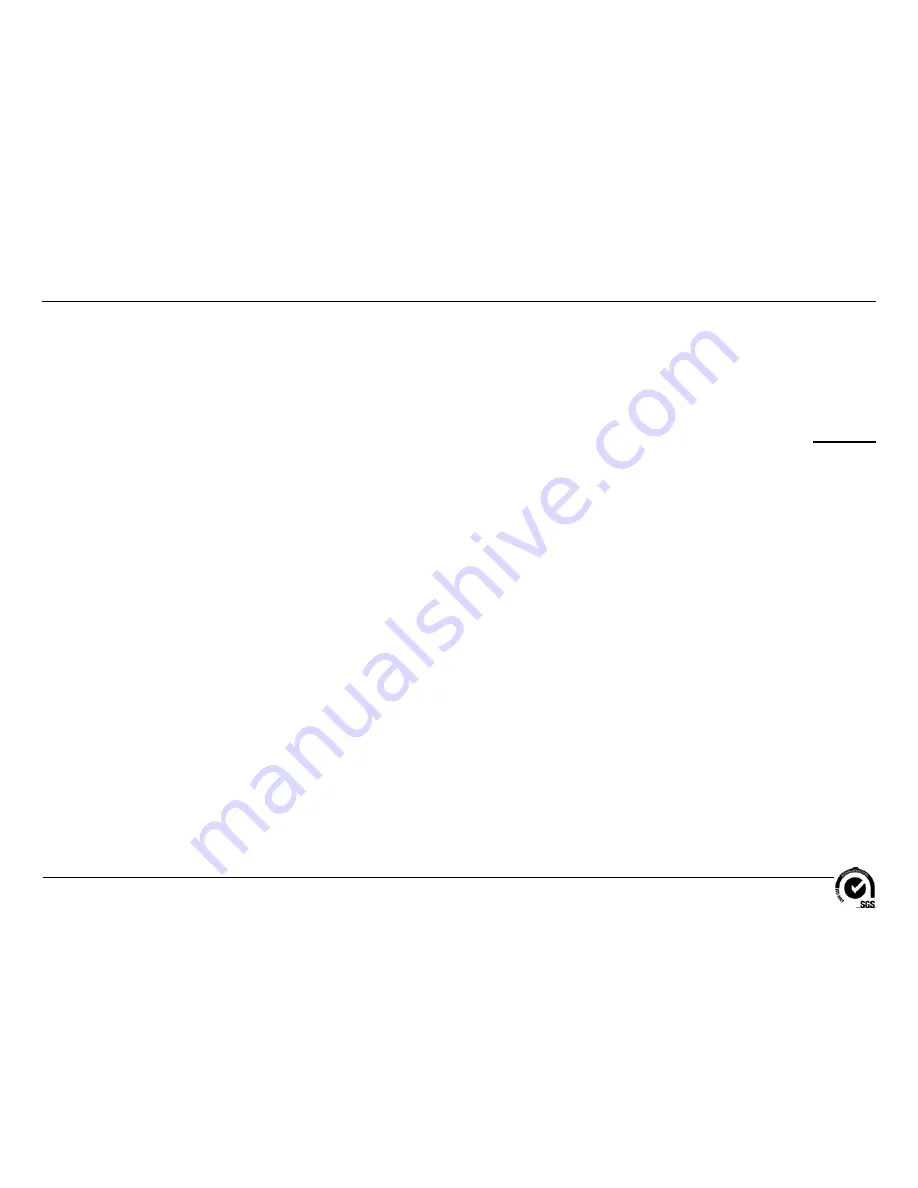
Model XX0596
ECN2463
Page 10 of 14
Installation Instructions
__
Notes Before You Begin:
Do not over tighten bolts during assembly, only snug
tighten them unless otherwise instructed.
Carefully read and understand these installation instructions before you
begin.
__Step 1:
Before attempting to assemble your equipment, please review all
installation information carefully. Should you experience any diffi culty during the
installation process, please call us at the telephone number shown on the last
page of these instructions.
__Step 2:
Separate and identify all components and hardware.
__Step 3:
Excavate footings as shown in the
Footing Details
.
Attach the spring to the anchor frame.
__Step 4:
Attach the spring to the anchor frame. See
Details A-1 and A-2
. Select
the see-saw anchor frame, and (1) one each of the following: spring, spring
wedge, 3/8" x 1-1/2" U-bolt, 3/8" x 2" U-bolt, and 1/2" x 2.94" U-bolt. Also select
the appropriate hardware. There are (6) six connections. Insert the spring wedge
between the end and next spring coil and rotate around until it is tight. The tabs
should be on the bottom, next to the end coil. Insert a 2.94" U-bolt over the second
spring coil and through the tabs on the wedge. Place the spring assembly on the
anchor frame mounting plate
as shown
and insert the U-bolt through the holes
in the mounting plate. Place a 2" U-bolt over the second coil and the end of the
bottom coil, and insert through the plate.
Note that the 2" U-bolt is inserted in the
outer two holes on the side of the mounting plate that has three holes arranged
in a straight line
. Position a 1-1/2" U-bolt over the bottom coil and insert it through
the plate. Attach the U-bolts to the plate as shown.
__Step 5:
Attach the spring top platform to the anchor frame. See
Detail B
. Select
(2) two spring top platforms and the appropriate hardware. There are (2) two
connections. Place the spring top platforms under the anchor frame and align
the holes. Attach as shown.
__Step 6:
Place the anchor frame into the prepared footing. Plumb and level.
Fully tighten
all
fasteners according to tightening torque specifi cations. Block and
brace for concrete. Pour concrete and allow 72 hours for concrete to completely
cure. Check frame to ensure that it is plumb and level after pouring concrete.
Attach the see-saw mounting plates to the anchor frame.
__Step 7:
Attach the see-saw mounting plates to the anchor frame. See
Detail
C
. Select both see-saw mounting plates, (1) one .99" O.D. cross shaft, and (2)
two of the following: 1" I.D. oilite bearings, shaft end caps, and 3/8" x 1" button
head bolts. Slide the cross shaft through the holes in the anchor frame mounting
plates and center. Slide a bearing, narrow side facing in, onto each end of the
cross shaft until fl ush against the mounting plate stub. With the mounting plates
angling inward over the frame, position the square hole in each plate onto the
square end of the shaft. Using loctite on the bolt threads, attach as shown.
Important Note
:
Ensure that the square portion of the cross shaft is fully seated
in the See-Saw mounting plate.
See
Detail C-1
.
Attach the cover panel mounting brackets to the frame
.
__Step 8:
Attach cover panel mounting brackets to the frame. See
Detail D
.
Select (4) four cover panel mounting brackets and the appropriate hardware.
There are (8) eight connections. Position each mounting bracket against the side
of the frame as shown. Ensure top of the bracket is level with the top of the frame.
Using loctite on the bolt threads, attach as shown.
Attach the frame to the mounting plates
.
__Step 9:
Attach the frame to the mounting plates. See
Detail E
. Select the frame
and the appropriate hardware. There are (12) connections. Position the see-saw
frame between the mounting plates with the spring mounting plate lined up with
the spring and, using loctite on the bolt threads, attach as shown.
Attach the frame to the spring.
__Step 10:
Attach the frame to the spring. See
Detail F
. Select (1) one of the
following: a spring wedge, 3/8" x 1-1/2" U-bolt, 3/8" x 2" U-bolt, and 3/8" x 2.94"
U-bolt. Also select the appropriate hardware. There are (6) six connections.
Position the see-saw frame spring mounting plate over top of the spring. Insert
a spring wedge between the end and next spring coil on the end of a spring and
rotate around until it is tight. The tabs should be on the top, next to the end coil.
Insert the 2.94" U-bolt up over the second spring coil and through the tabs on
the wedge. Position frame so the legs of the U-bolt stick up through the holes in
the spring mounting plate.
Note that the
2.94"
U-bolt is inserted in the outer two
holes on the side of the mounting plate that has three holes arranged in a straight
line. Spring must be mounted as shown in Detail F
. Place the 2" U-bolt up over
the second coil, and the end of the bottom coil. Position the 1-1/2" U-bolt over
the bottom coil and insert it up through the plate. Make attachments as shown.
Fully tighten connections.