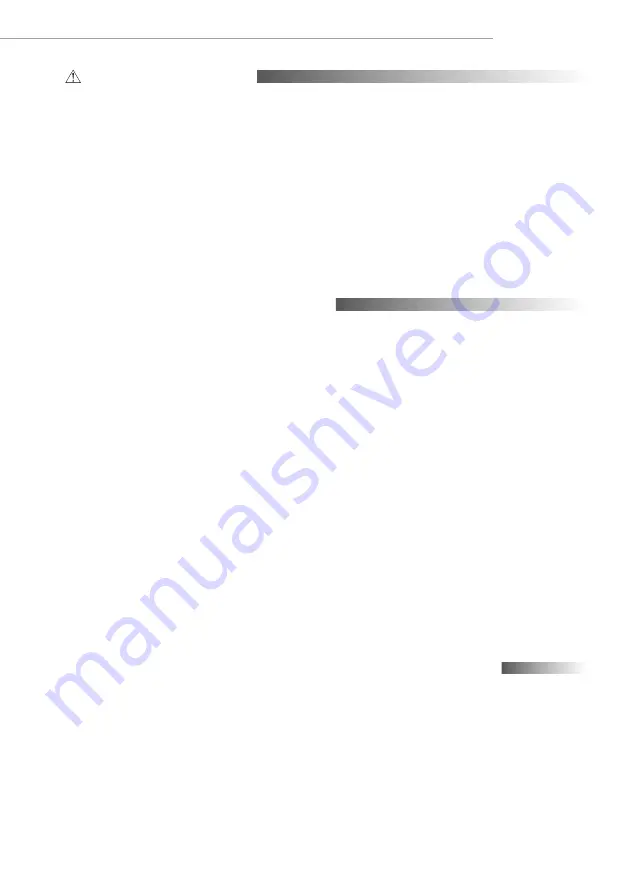
Safety Rules for Use
■ 1. Safety Rules for Manifold Type
■ 2. LED Digital Vacuum Pressure Sensor (Vacuum Switch)
■
Operating temperature range is 5-50
℃
. Do not operate the product out of the temperature range.
■
Compressed air contains many kinds of drains such as water, oxidized oil, tar and other foreign
substances. Dehumidify and improve the quality of air by using an after-cooler or a dryer, since those
drains seriously impair the performance of the vacuum generator.
■
Do not use lubricators.
■
Rusts in the pipes may cause malfunction. Place a filter with finer than 5
µ
m ahead of the air supply port.
■
Avoid using the vacuum generator under the condition of corrosive gas or inflammable gas. Also do not
use these gasses as a fluid.
■
Avoid sucking dusts, salt and iron powder as much as possible.
■
Do not operate Blow-off solenoid valve during a vacuum generation.
■
After adjusting the air rate and turn the locknut until it stops at the needle guide, additionally tighten the
locknut at 20-30
°
with a proper tool such as a pair of long-nose pliers. When this additional tightening
is not done, the locknut maybe loosened and result in damaging the needle and the thread part of
the locknut. Too much tightening may cause damage such as scraping off the knurling surface or a
deformation of female thread.
■
There is a possibility of a performance drop or a trouble by increasing mounting unit numbers on
manifold type due to the following reasons. Consult us for the solutions.
1. A drop of the vacuum performance due to insufficient supply air.
Countermeasures:
①
Check the supplied air volume.
②
Arrange the piping length as short as possible.
③
Use Fittings with larger size.
④
Use both R and L side ports for the supply pressure when the supply is
from one side only.
2. When there is a drop of the vacuum performance due to insufficient volume of exhaust port, or is an
exhaust air leaking out through the vacuum port.
→
Consult us for the solutions. There is a limit of station numbers to maintain the manifold performance
by a nozzle size or a vacuum performance of each mounting unit.
Reason (Silencer vent): A drop of the vacuum performance due to a large exhaust resistance caused
by insufficient volume of silencer exhaust.
Countermeasures:
①
Use silencers on both exhaust ports when a silencer is on one side.
②
Set an external silencer (Special order)
③
Exhaust individually from each mounting unit. (Special order)
④
Avoid any obstacles around the exhaust ports.
⑤
Reduce number of mounting units.
Reason (Tube exhaust): A drop of the vacuum performance is caused by large pipe resistance.
Countermeasures:
①
Use both exhaust ports when exhaust ports is on one side.
②
Arrange the piping length as short as possible.
③
Use Fittings with larger size.
④
Exhaust individually from each mounting unit. (Special order)
⑤
Reduce number of mounting units.
(
1
)
Pressure Setting Method
①
Turn on the power (Make sure the correct wiring and apply DC power to the vacuum pressure
sensor).
②
-1 Set the indicator switch at Pressure Setting Mode (ME
→
S1 / S2 and SW)
②
-2 (Vacuum switch with analog output)
Fully turn the hysteresis setting trimmer (HYS) in the counterclockwise direction in order to
minimize the hysteresis adjustment in advance.
③
Adjust the pressure adjusting trimmer (S1 / S2 and SW) with a flathead screwdriver to set at the
desired value.
④
Set the indicator switch at ME and apply pressure and check the actual operation.
(Vacuum switch with 2 switch output)
Switch output 1 (S1): Red LED turns ON at the pressure with more than the setting.
Switch output 2 (S2): Green LED turns ON at the pressure with more than the setting.
(Vacuum switch with analog output)
Switch output (SW): Red LED turns ON at the pressure with more than the setting.
http://www.pisco.com
Summary of Contents for VK Series
Page 26: ...Vacuum Generator Series ...