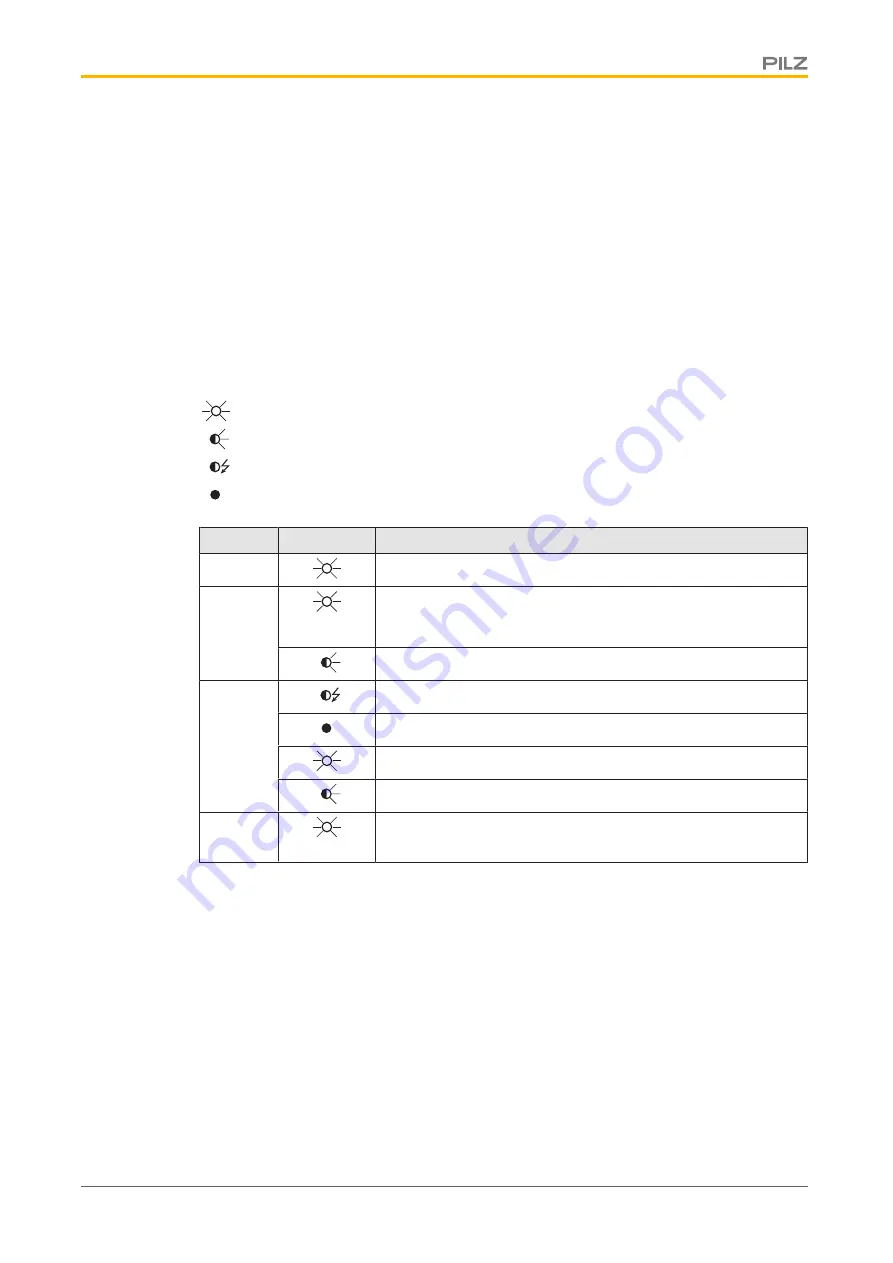
Operation
Operating Manual PNOZ ms4p
22109-EN-03
20
7
Operation
When the supply voltage is switched on, the PNOZmulti safety system copies the configur-
ation from the chip card.
The LEDs “POWER”, “DIAG”, “FAULT”, “IFAULT” and “OFAULT” will light up on the base
unit.
The PNOZmulti safety system is ready for operation when the "POWER" and "RUN" LEDs
on the base unit and the "READY" LED on the PNOZ ms4p are lit continuously.
7.1
LED indicators
Legend
LED on
LED flashes
LED flashes briefly
LED off
LED
LED status Meaning
POWER
Supply voltage is present.
FAULT
External fault leading to a safe condition; the fault is at the in-
cremental encoder inputs whose LEDs are flashing, e.g. short
across the contacts
Internal fault leading to safe condition
SHAFT
Encoder or wiring fault
Axis is in the normal range (no standstill, no overspeed)
Axis is signalling standstill
Axis is signalling overspeed
X12
Incremental encoder on terminal X12 is connected correctly