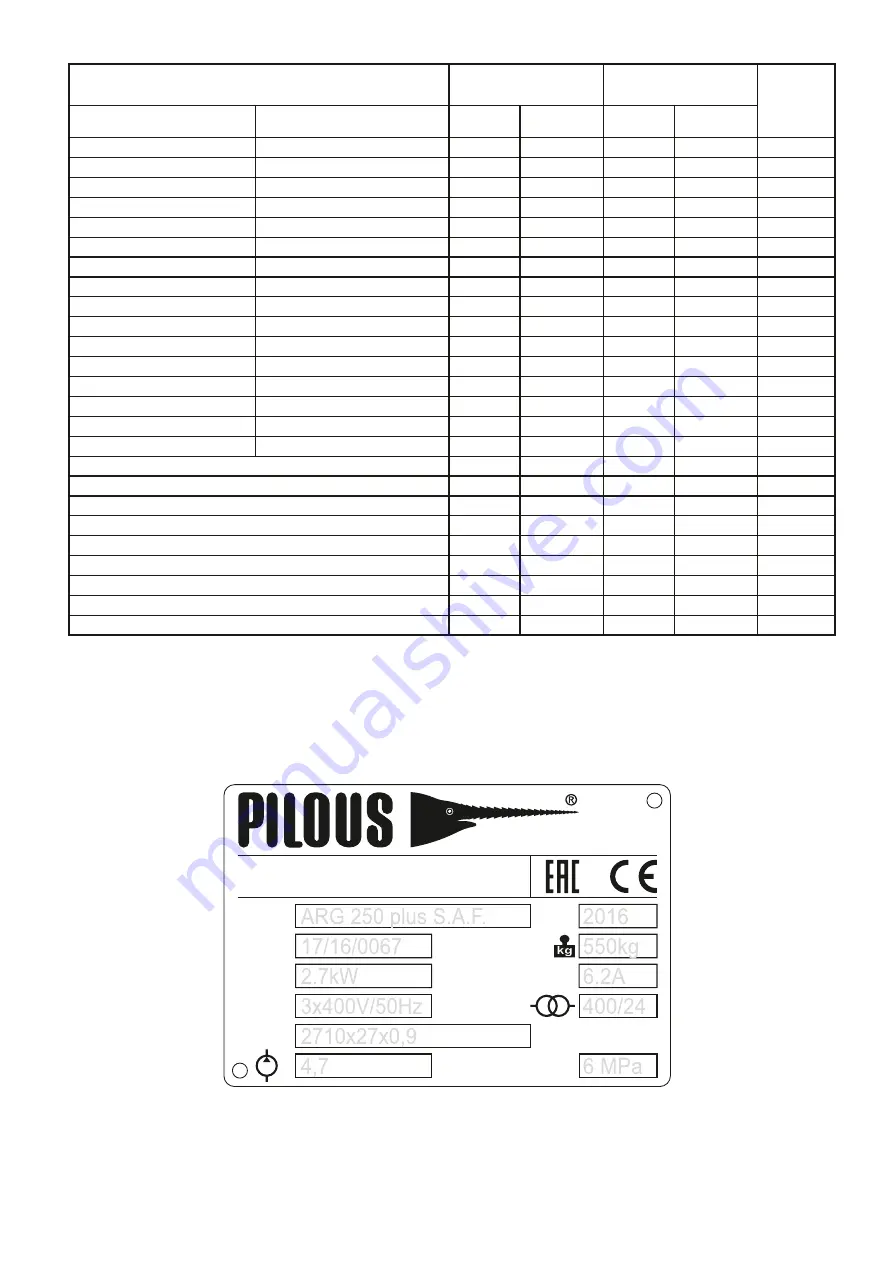
11 107 - 11 110
11 500 - 11 600 / 12 020 - 12 060
13 250 / 14 260 / 15 260
14 100 / 15 220
14 220 / 15 124
17 020 - 17 042
17 115
17 253 - 17 255
19 150 / 19 192 - 19 312
19 422 / 19 452 / 19 721 / 19 740
19 436
19 662
19 721
19 802 - 19 860
INCONEL, HASELLOY, NIMONIC, INCOLOY
Heat-treated steel
Cast steel
Grey cast iron
Copper, bronze, tin bronze
Red bronze
Aluminium bronze
Aluminium alloy castings
Al 99%, thermoplastics, plastics
11 301 - 11 420 / 12 010 - 12 020
19 063 - 19 083 / 15 142 / 16 142
ČSN
Material
Cooling
oil
volume
(%)
10-15
10
10-15
5-10
3
10-15
10-15
5-10
15
5-10
5-10
3
do not
15-20
5
3
15-20
5
40
25
3
10
10-15
do not
do not
Arm descent speed
into the cut
(mm/min)
ø 100-330 mm
55-20
30-20
35-25
28-15
28-15
55-30
12-4
18-2
6-1
30-25
20-8
21-10
14-5
4-2
16-6
21-10
4-2
23-12
55-25
140-55
85-55
70-45
70-45
55-30
140-55
ø 0-100 mm
190-60
125-35
125-38
125-30
125-30
190-60
75-15
100-20
40-7
125-35
120-25
90-23
62-15
25-5
70-1
90-23
25-5
76-25
190-60
450-150
300-90
230-75
230-75
190-60
450-150
Recommended blade speed
(m/min)
ø 100-330 mm
70-90
40-70
50-70
40-60
30-60
60-80
30-40
30-50
30
40-70
30-60
30-50
30-40
30
30
30-50
30
30-40
30-60
80-90
60-90
60-90
30-60
30-70
50-80
ø 0-100 mm
70-90
50-80
60-90
50-70
50-70
60-90
40-50
40-50
30-40
60-90
50-70
40-60
30-40
30
30-40
40-60
30
40-50
30-70
80-90
70-90
70-90
40-70
40-80
50-90
In general
Free-cutting steel
Structure/construction steel
Cementing steel
Spring steel
Bearing steel
Alloy steel
NIRO steel
Valve steel
Heat-resistant steel
Refining steel
Non-alloy tool steel
Alloy steel
Hammer steel
Nitriding steel
Tool steel for hot processing
High speed steel
9. Nameplate
The data are only illustrative
MANUFACTURER
MANUFACTURER`S ADDRESS
MACHINE MODEL
SERIAL NUMBER
TOTAL WATTAGE
OPERATING VOLTAGE
SAW BLADE SIZE
VOLUMETRIC FLOW
YEAR OF MANUFACTURE
MACHINE WEIGHT
RATED CURRENT
CONTROL VOLTAGE
MAXIMUM SYSTEM PRESSURE
3
dm /min
p
max
Pilous-pásové pily, spol. s r.o.
Producer
Železná 9, 619 00 Brno, CZ
Address
Blade
Q
Model
Serial No.
P
U
Year
I
Summary of Contents for ARG 330 plus S.A.F.
Page 2: ......